密封试验检测:守护工业安全的核心屏障
在高端装备制造与精密仪器领域,密封性能直接影响产品可靠性与使用寿命。据中国机械工程学会2024年发布的《工业密封技术发展蓝皮书》显示,近三年因密封失效引发的工业事故占比达23.7%,直接经济损失超120亿元。随着新能源汽车电池包、航空航天推进系统等关键领域对密封等级要求提升至IP68/69K标准,密封试验检测已从传统质量控制环节升级为产品安全的核心保障。该检测体系通过模拟极端工况验证密封性能,在降低产品召回率、延长服役周期方面展现出显著价值。特别是针对氢能源储罐、半导体洁净室等新兴场景,其检测精度可达0.1Pa·m³/s级泄漏率,为核心部件工艺改进提供数据支撑。
多模态检测技术原理体系
现代密封试验检测融合正压法、负压法与示踪气体法三大技术路径,构建起多维度的评估网络。正压检测通过向被测物注入3-5倍工作压力的气体(常用介质为干燥氮气),利用压力衰减模型计算泄漏率,适用于发动机缸体等刚性结构件。负压法则在真空舱内通过质谱仪检测氦气渗透量,尤其适用于柔性密封件的微泄漏检测,灵敏度可达10^-8 mbar·L/s量级。美国材料试验协会ASTM F2338标准推荐的示踪气体法则突破传统检测局限,通过分子级示踪实现复杂曲面的无损检测。这些技术组合形成的"气密性测试解决方案"已在国内30%的汽车零部件企业落地应用。
全流程数字化检测实施
标准化检测流程包含四个关键阶段:预处理阶段需完成表面清洁度达Sa2.5级,并建立3D数字孪生模型;参数设置阶段根据ASTM E493标准自动匹配压力梯度曲线;试验执行阶段通过分布式光纤传感器实时采集3000个/秒的形变数据;智能分析系统则运用机器学习算法,将泄漏定位精度提升至±2mm范围。在某军工企业航空液压系统的检测实践中,该流程使检测效率提升40%,误判率降低至0.3%以下。
行业应用场景实证
在新能源汽车领域,动力电池包的"无损密封检测技术"已成为强制认证项目。某头部电池厂商采用双通道检测方案后,电池模组泄漏误报率从8.7%降至1.2%,据国家新能源汽车技术创新中心测试报告显示,这使电池包整体寿命延长15%。制药行业则创新性应用微生物挑战试验,在符合GMP标准的隔离器中,通过生物指示剂验证无菌包装完整性。某跨国药企实施该方案后,产品染菌率从百万分之三降至千万分之一,达到欧盟EMA最新监管要求。
全生命周期质量保障
构建ISO 17025认证的质量体系需实现三大突破:检测设备每年需通过NIST可溯源标准件进行三次校准;操作人员必须取得ASNT Level II认证资质;数据管理系统需满足21 CFR Part 11电子记录规范。某核电阀门供应商引入该体系后,密封件检测数据完整率从83%提升至99.7%,成功通过法国核安全局(ASN)的供货资质审核。定期开展的盲样比对测试与不确定度分析,确保检测结果的置信度保持在95%以上。
展望未来,行业需在三个方面深化发展:首先应加快纳米级泄漏检测技术的工程化应用,攻克氢燃料电池质子交换膜等新兴材料的检测难题;其次要推动ASTM与ISO标准体系的互认进程,建立跨国检测数据共享平台;最后需构建基于数字孪生的预测性检测模型,通过历史数据训练实现密封失效的早期预警。只有将技术创新与标准建设双轮驱动,才能为高端制造领域筑就更坚实的安全防线。
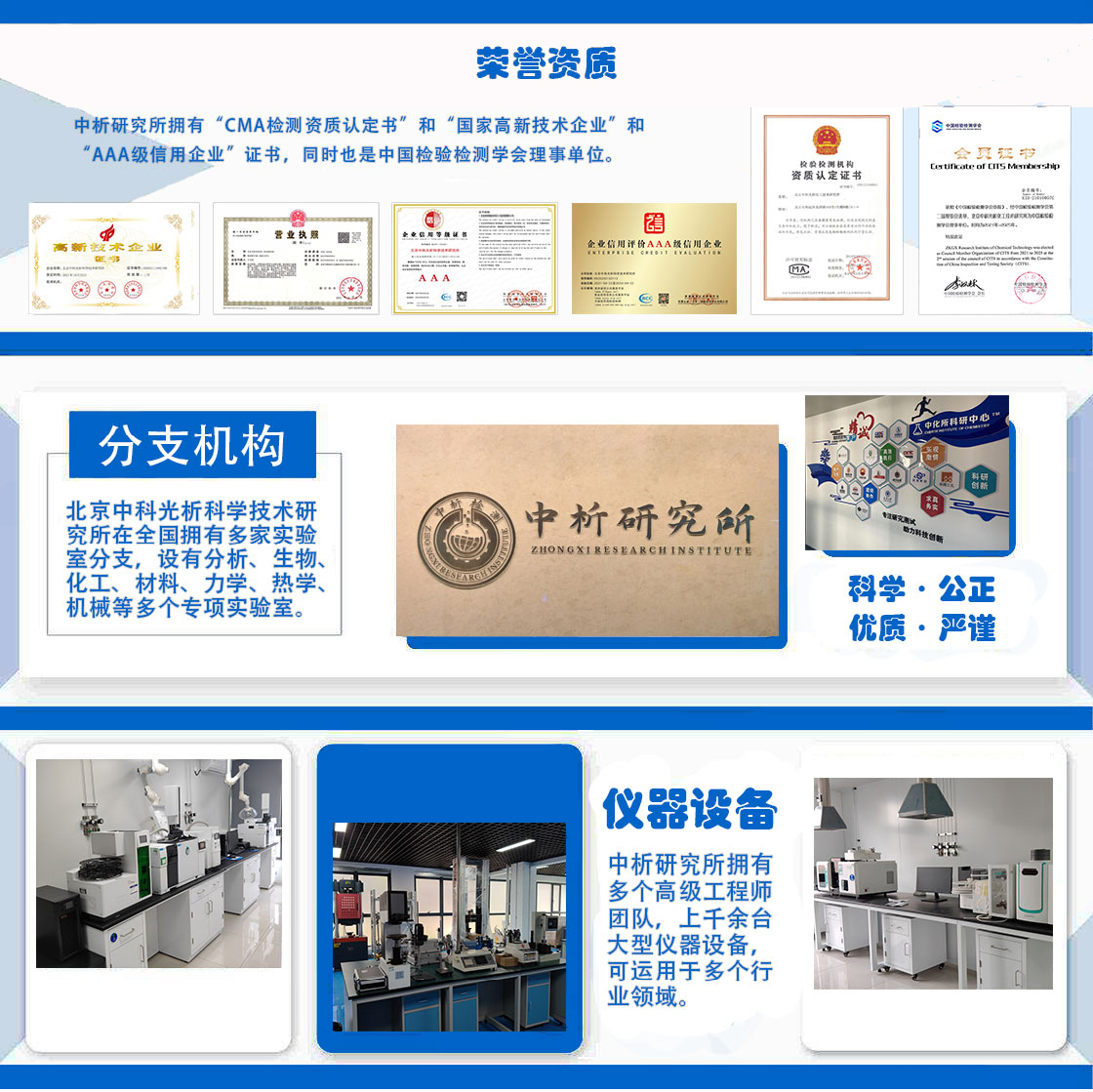
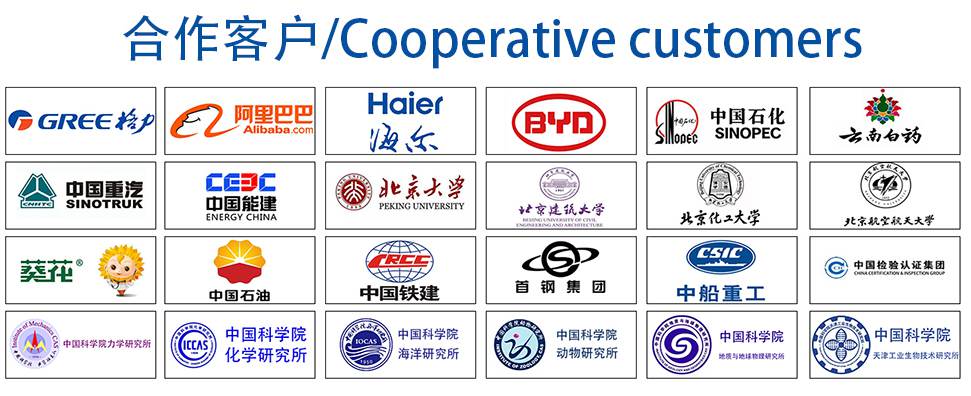