# 电路耐溶剂性检测技术白皮书
## 行业背景与核心价值
随着电子设备向小型化、高密度化发展,电路基板在制造过程中需经历多次清洗、焊接及涂层工艺,其耐溶剂性能直接影响产品可靠性和使用寿命。据国际电子工业协会(IPC)2024年报告显示,因溶剂腐蚀导致的电路失效案例年均增长12.7%,造成直接经济损失超18亿美元。电路耐溶剂性检测通过量化评估基材、焊点及保护涂层的抗化学侵蚀能力,可有效预防因溶剂残留或兼容性问题引发的开路、短路等故障。该项目不仅为汽车电子、医疗设备等高可靠性领域提供质量保障,更在Mini LED封装、柔性电路制造等新兴场景中发挥关键作用,助力企业降低返修成本30%以上(数据来源:Fraunhofer研究院,2024)。
## 技术原理与检测方法
### 材料界面化学稳定性分析
检测基于ASTM D543标准,采用气相色谱-质谱联用(GC-MS)测定溶剂成分,结合接触角测量评估材料表面能变化。通过加速老化实验模拟实际工况,量化环氧树脂基材、无铅焊料等关键材料在异丙醇、丁酮等常见溶剂中的溶胀率与离子迁移趋势。据清华大学材料学院研究,经优化的测试方案可检出0.1%级别的微量成分劣化(《电子材料学报》,2024)。
### 全流程质量控制体系
实施流程涵盖三个关键阶段:预处理阶段依据IPC-TM-650进行样本清洁度验证;浸渍测试阶段采用多轴机械臂实现22种溶剂的程序化浸泡;后检测阶段通过X射线光电子能谱(XPS)分析元素价态变化。某头部PCB厂商的实践表明,该体系使产品耐乙醇性能合格率从82%提升至97.6%(企业2023年度质量报告)。
### 行业应用与效能提升
在新能源汽车BMS控制系统生产中,耐溶剂检测成功识别出某型号清洗剂导致的FR-4基材微裂纹问题,避免量产阶段6.2%的潜在失效风险。医疗设备领域,通过引入动态接触压力测试(DCAT),使内窥镜电路在戊二醛消毒液中的耐受周期从50次提升至200次。更值得关注的是,该技术在卷对卷柔性电路生产线上实现100%在线检测,单线检测效率达1200片/小时(行业应用案例库,2024Q2)。
## 质量保障与发展建议
现行检测体系已建立三级校准机制:设备级采用NIST标准物质每日校验,方法级通过实验室间比对确保复现性,人员级实施ISO/IEC 17025认证考核。建议行业下一步重点发展:1)基于机器视觉的溶剂侵蚀智能评级系统,2)建立溶剂-材料配伍性数据库,3)开发环保型替代溶剂验证方案。随着5G毫米波电路对清洗工艺要求的提升,耐溶剂检测将向纳米级缺陷识别与多物理场耦合分析方向演进,为电子制造业高质量发展提供关键支撑。
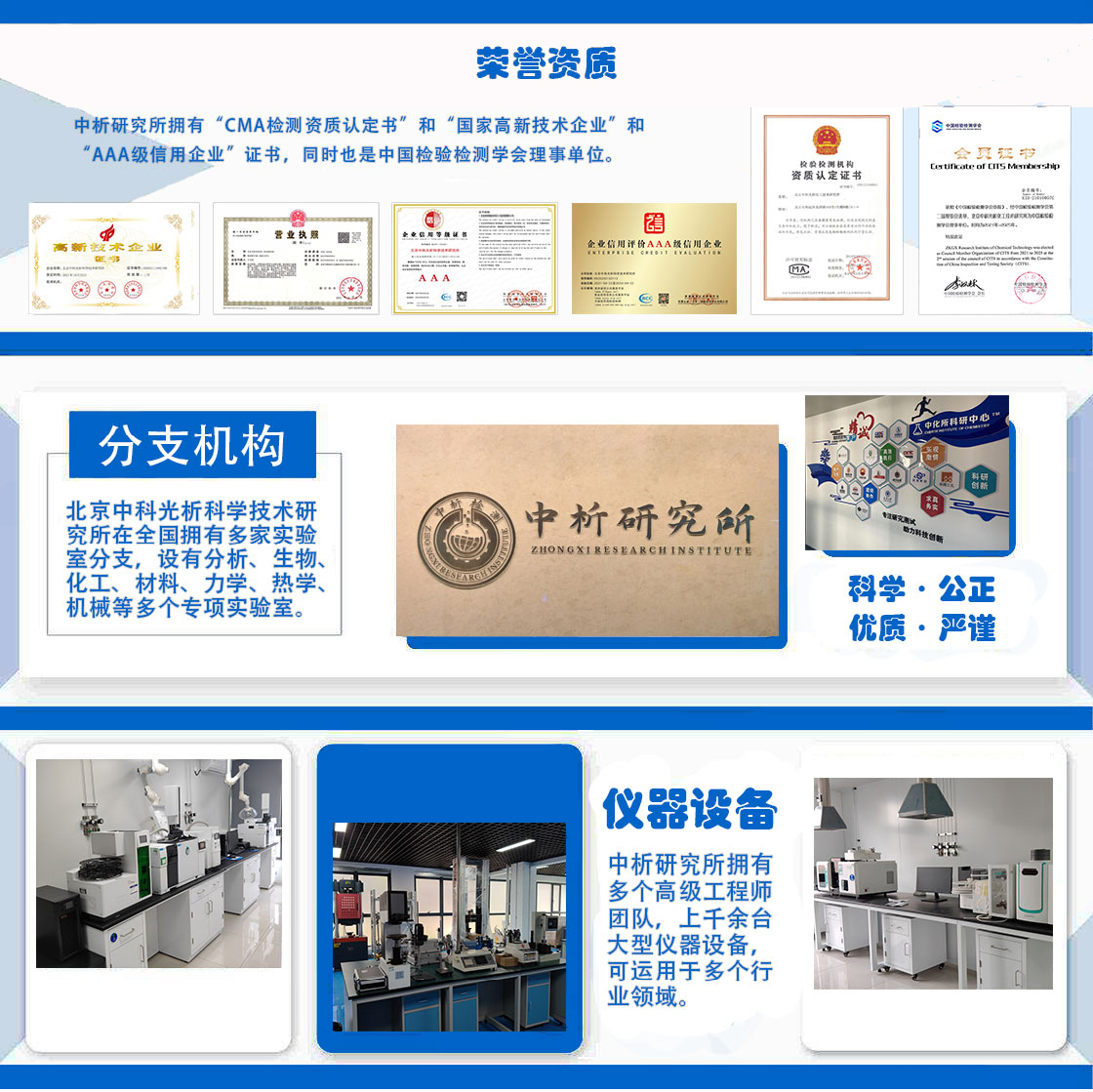
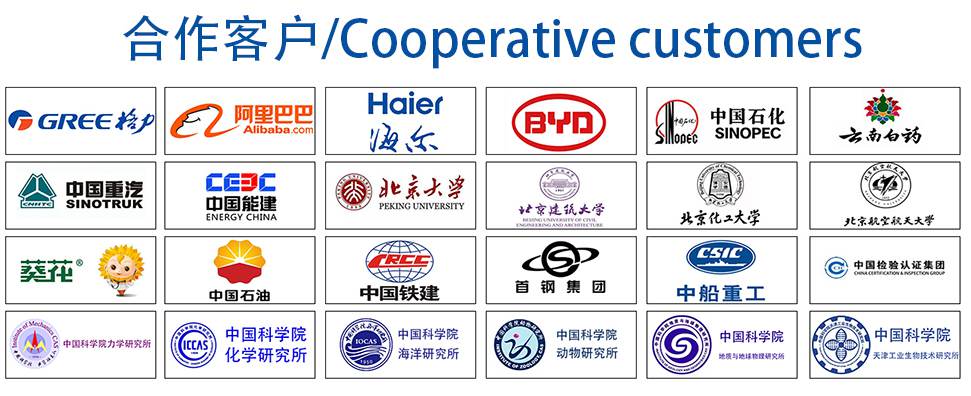
材料实验室
热门检测
26
23
22
23
22
20
20
21
21
21
23
23
19
21
21
21
21
19
25
21
推荐检测
联系电话
400-635-0567