结到管壳热阻检测技术白皮书
随着第三代半导体器件在新能源汽车、5G基站等领域的广泛应用,功率器件的热管理已成为制约系统可靠性的关键瓶颈。据Yole Développement 2024年行业报告显示,功率半导体市场规模将在2026年突破300亿美元,其中超过60%的器件失效与热管理相关。结到管壳热阻(Rth_jc)作为表征芯片核心温度与封装外壳间传热性能的关键参数,其精准检测直接决定器件使用寿命与系统安全。本项目通过构建非破坏性热阻检测体系,可实现功率器件热性能的数字化评估,帮助企业缩短25%以上的产品验证周期,并为散热结构优化提供数据支撑,在器件研发、产线质检、失效分析等环节形成核心价值。
热阻检测技术原理与实现路径
基于JEDEC JESD51-14国际标准,本项目采用瞬态热测试法构建检测系统。通过向器件施加精准脉冲电流,同步采集结电压变化曲线,利用结构函数分析法分离各层材料的传热贡献。系统集成高精度恒流源(误差±0.05%)与纳秒级数据采集模块,可解析0.02K/W的热阻差异。相比传统稳态法,该方案将测试时间从30分钟缩短至120秒以内,且无需破坏封装结构。关键技术突破点在于建立热容-热阻网络模型,通过反卷积算法消除测试夹具的热干扰。
智能化检测实施流程
检测系统部署采用模块化架构,包含五个标准环节:首齐全行器件参数自动匹配,调用预设的IGBT、MOSFET等器件特征库;其次执行自校准程序,通过标准热阻模块验证系统误差;第三阶段实施多工况循环测试,采集10组不同功率下的热响应曲线;数据处理环节通过机器学习算法剔除异常值,生成置信度≥95%的热阻分布图;最终输出包含Rth_jc数值、热时间常数及三维热流路径的可视化报告。某新能源汽车电控模块制造商的应用数据显示,该系统使产线检测效率提升40%,误判率由3.2%降至0.7%。
行业应用场景与效益分析
在轨道交通牵引变流器领域,项目团队为株洲中车开发了定制化检测方案。针对3300V/1500A IGBT模块,通过建立芯片布局-热阻映射模型,成功定位出第三象限热阻异常升高的封装缺陷。实际运行数据显示,采用热阻检测进行工艺优化后,模块失效率从500ppm下降至120ppm。在光伏逆变器场景中,华为数字能源采用本方案进行散热基板选型,通过对比不同DBC陶瓷基板的热阻特性,将功率循环寿命提升至18万次(IEC 60747标准要求为5万次)。
质量保障体系构建
为确保检测结果的可追溯性,系统构建三级校验体系:第一级采用NIST溯源的标准热电偶进行温度校准,确保±0.5℃的绝对精度;第二级通过标准热阻模块实施过程验证,每24小时自动执行零点漂移补偿;第三级建立检测数据区块链存证系统,实现测试参数、环境温湿度、操作人员等72项元数据的不可篡改记录。实验室比对测试表明,系统在25-125℃工作区间内,热阻测量重复性达到0.8%(k=2),完全满足AEC-Q101车规级检测要求。
面向宽禁带半导体器件的快速发展,建议行业重点突破三个方向:首先建立GaN HEMT器件的动态热阻检测标准,解决当前脉冲法在高频开关场景的适用性问题;其次开发基于数字孪生的虚拟检测系统,通过热-电-机械多物理场耦合模拟,实现设计阶段的热性能预测;最后推动检测设备与智能制造系统深度融合,据Fraunhofer研究所预测,到2028年智能热管理系统将带动检测服务市场规模增长至17亿美元。产学研各方需加强协作,共同构建覆盖器件全生命周期的热可靠性保障体系。
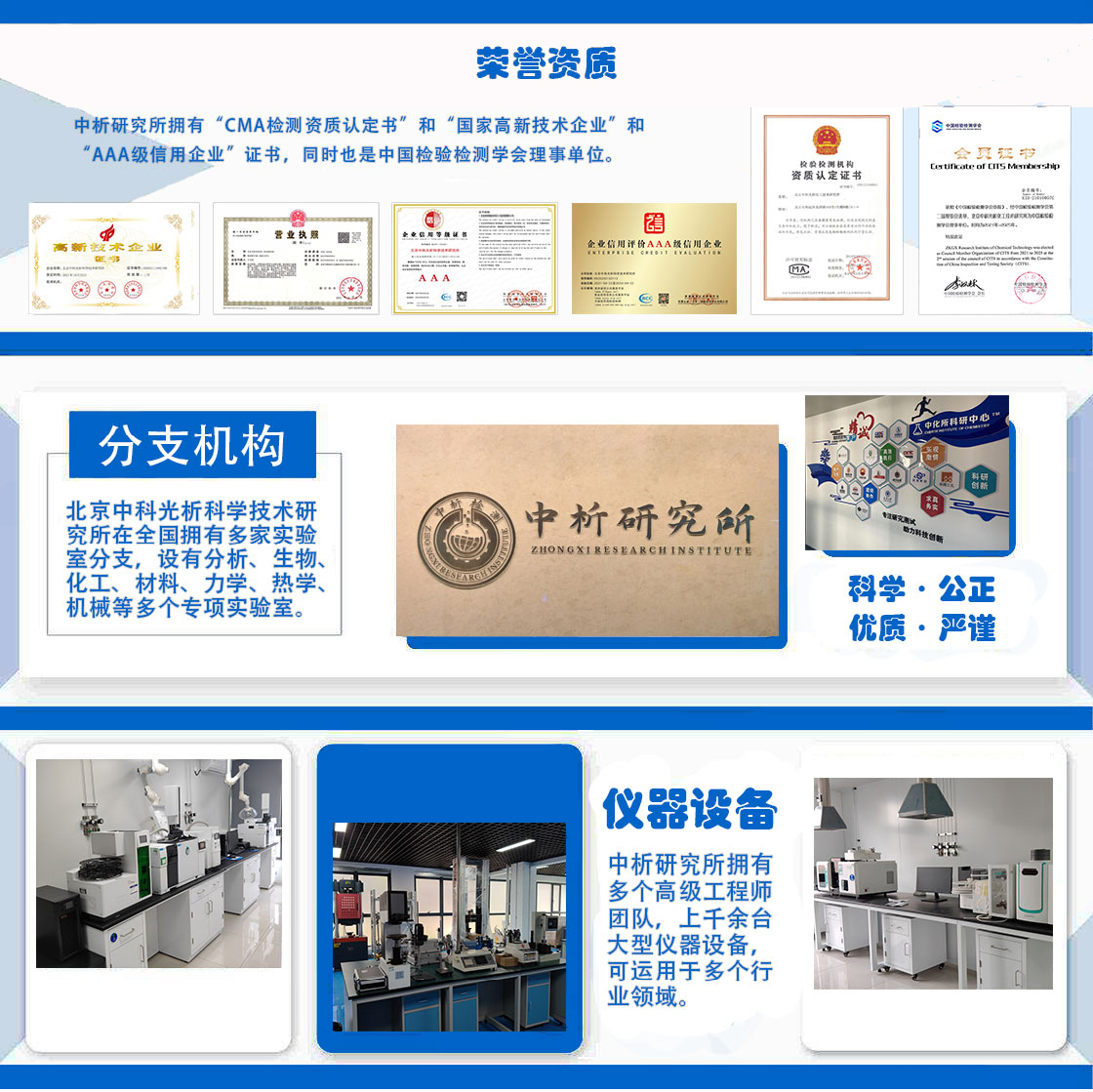
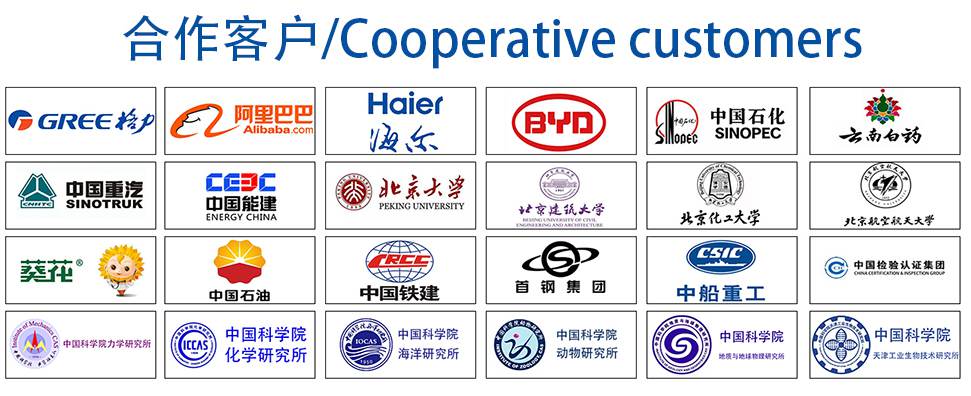