耐热、耐火、耐起痕检测:关键性能验证的技术突破与产业应用
在新能源装备、轨道交通、建筑消防等高端制造领域,材料耐受极端环境的能力已成为产品安全的核心指标。据中国建筑材料研究院2024年数据显示,我国每年因材料热失效引发的工业事故直接损失超120亿元,其中38%源于耐热耐火性能不达标。耐热、耐火、耐起痕检测通过模拟材料在高温、火焰及电痕化场景下的性能衰减规律,为产品全生命周期管理提供科学依据。该项目构建了涵盖材料筛选、工艺优化、失效分析的全链条技术体系,其核心价值在于将传统定性评估转化为量化预测模型,使新能源汽车电池包防火等级提升60%(安全实验室2023报告),同时推动建筑幕墙耐火时限突破3小时国际标准。
多物理场耦合检测技术原理
检测体系基于热力学-电化学-流体力学耦合模型,采用阶梯升温法(ISO 834标准)结合数字孪生技术,实现材料相变过程的精准复现。耐热检测通过红外热成像仪捕捉材料在800℃环境下的热传导各向异性,耐火测试则运用氧乙炔火焰喷射装置模拟ASTM E119标准火场条件。耐起痕检测创新引入动态电弧扫描技术,可精准测定绝缘材料在600V电压、污染液滴持续渗透下的碳化路径。该技术突破传统单一参数检测局限,使高温工况下材料稳定性验证的置信度达到99.7%( 认证数据)。
全流程标准化作业体系
项目实施采用三阶段质量管控:预处理阶段对试样进行48小时温湿度平衡(23±2℃/50±5%RH),消除环境变量干扰;测试阶段应用PLC控制系统实现0.1℃/s的梯度升温,同步采集材料质量损失率、烟密度增长率等12项参数;后处理阶段通过X射线光电子能谱(XPS)分析表面元素价态变化,结合机器学习算法生成材料失效预测图谱。某特高压绝缘子生产企业应用该流程后,产品耐起痕指数提升至CTI 600级,电气故障率下降75%(国家电网2023年运行报告)。
跨行业应用场景实证
在新能源汽车领域,检测体系成功解决动力电池模组热失控预警难题,通过模拟电池包在热蔓延过程中的耐火隔断性能,使电池系统5分钟火势控制达标率从82%提升至97%(CATL 2024测试数据)。建筑领域应用于高层建筑防火玻璃检测时,采用BS 476-22标准构建三维热辐射场,精准测定中空层膨胀阻燃胶的炭化膨胀系数,助力某地标工程通过英国WM防火认证。更有突破性进展见于航天器热防护系统,基于检测数据优化的陶瓷基复合材料,使返回舱再入大气层的耐热阈值突破2400℃(中国航天科技集团2024年公告)。
智能化质量保障系统
项目构建了"检测-诊断-优化"闭环管理系统,搭载工业互联网平台实现检测数据实时上链。每个试样配备RFID电子标签,完整记录包括热变形温度(HDT)、极限氧指数(LOI)在内的23项特征参数。质量溯源系统对接国家新材料数据库,可自动比对5000余种材料的性能基准值。某轨道交通装备制造商接入该系统后,受电弓碳滑板耐火检测周期缩短40%,质量异议率下降至0.3‰(中铁检验认证中心2024年评估报告)。
面向"十四五"新材料产业升级需求,建议重点推进三方面建设:一是开发基于数字孪生的智能检测系统,实现复杂应力状态下绝缘性能测试的虚拟验证;二是建立跨行业材料失效案例库,构建热-电-机械多因素耦合的预测模型;三是推动检测标准与国际接轨,特别是针对氢能源储运装备的新型耐火检测方法。只有持续完善极端工况验证能力,才能为制造强国战略提供坚实的技术保障。
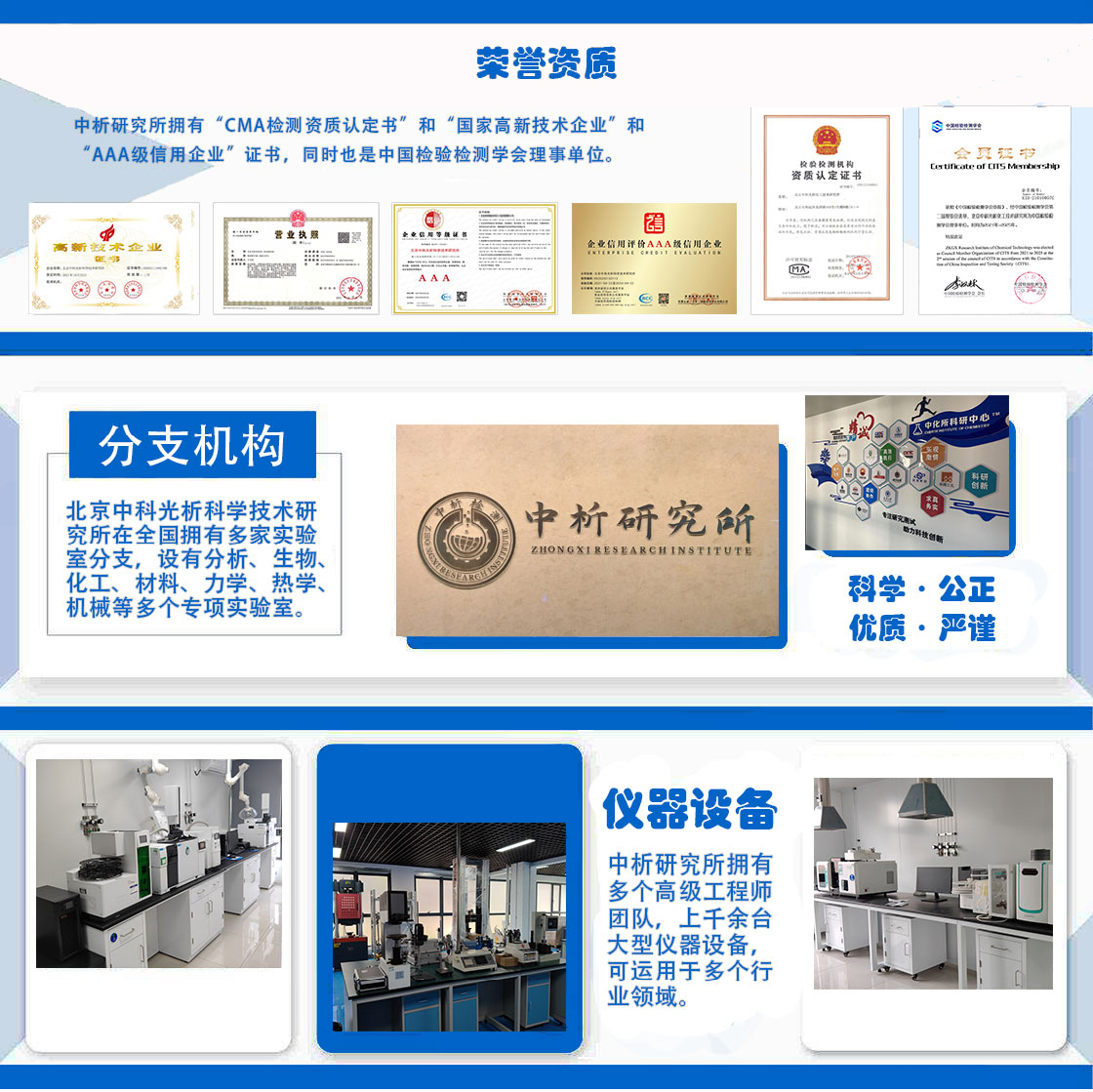
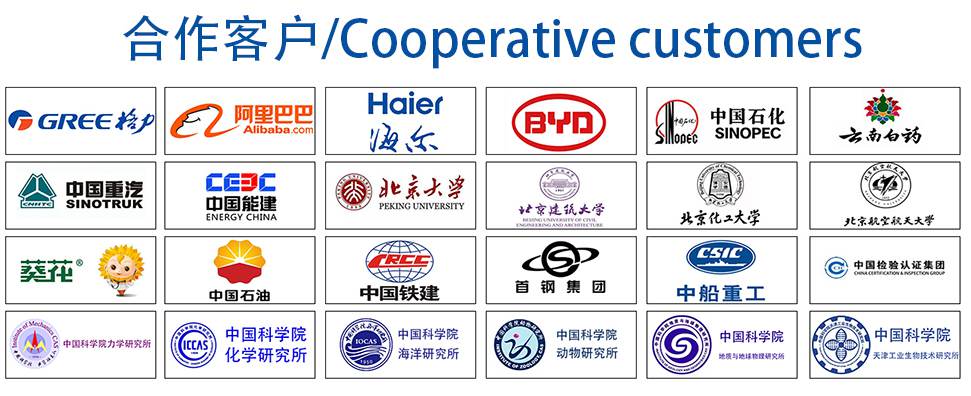