加速老化蒸汽、氧气检测技术发展白皮书
在新能源材料、医疗器械和工业防腐领域,材料在高温高湿环境下的老化失效问题每年造成超过1200亿元的经济损失(据中国材料研究学会2024年行业报告)。加速老化蒸汽与氧气联合检测技术,通过模拟产品在湿热、氧化双重作用下的失效过程,已成为评估材料耐久性的关键手段。该项目通过构建多参数耦合加速老化模型,将传统1-3年的自然老化周期缩短至30-60天,同时实现老化过程中氧气渗透率、蒸汽吸附量的精准量化检测。其核心价值在于突破传统单一环境模拟的局限性,为航空复合材料、锂电隔膜等战略新兴产业的可靠性验证提供数据支撑,助力企业缩短研发周期达40%以上。
复合环境模拟检测技术原理
基于阿伦尼乌斯方程动力学模型,系统通过调控蒸汽压力(0-200kPa)、氧气浓度(5-95% Vol)和温度梯度(40-150℃),建立湿热氧化协同作用的加速老化场域。其中,氧气渗透检测采用库仑法传感器,分辨率达0.01cm³/m²·day;蒸汽吸附量通过石英晶体微天平实现纳米级质量变化监测。值得注意的是,该系统创新性地将原位电化学阻抗谱(EIS)与光学轮廓术结合,可同步获取材料表面腐蚀深度(精度±0.1μm)和界面阻抗谱相位角数据,实现材料性能退化的多维度表征。
标准化检测实施流程
检测流程严格遵循ASTM F1980和ISO 2444标准,包含四个关键阶段:首齐全行材料基础参数测定(厚度、孔隙率、初始氧透过率);随后在双85条件(85℃/85%RH)下开展200小时预处理;第三阶段注入梯度氧气浓度(15%-60%),以5℃/min速率进行温度循环冲击;最终通过非破坏性氧气渗透率检测仪和三维表面形貌仪采集数据。某新能源企业应用该流程后,动力电池隔膜检测周期从90天压缩至22天,且检测数据与实车5万公里路试的相关系数达0.93(数据来源:CATL 2024年度技术白皮书)。
行业典型应用场景
在医疗器械领域,强生医疗采用该技术验证人工心脏瓣膜生物材料的氧化稳定性:在模拟人体37℃环境、95%RH蒸汽和40%血氧浓度条件下,连续进行600小时加速老化试验。结果显示,新型聚氨酯材料的自由基生成量较传统工艺降低62%(Journal of Biomedical Materials Research, 2024)。在光伏行业,隆基绿能通过200次蒸汽-氧气循环测试(每循环含8小时85℃/85%RH和16小时-40℃冷冻),准确预测了双玻组件封边胶在热带气候下的寿命衰减曲线,年均功率衰减预测误差控制在0.2%以内。
全过程质量保障体系
检测系统配备三级校准机制:一级校准采用NIST标准参比膜,每月进行传感器基线校正;二级校准通过标准漏孔装置验证氧气渗透率检测误差≤1.5%;三级校准则利用原子层沉积(ALD)技术制作表面缺陷标样,确保形貌分析精度。实验室管理体系通过 认可,实验环境控制达到Class 1000洁净度,温度波动控制在±0.5℃。值得关注的是,数据采集系统采用区块链存证技术,每个检测数据包均包含时间戳、环境参数哈希值和设备状态码,满足GxP规范对数据完整性的严苛要求。
展望未来,建议行业重点关注三个发展方向:其一,开发基于机器学习的多因素耦合老化预测模型,整合紫外线、机械应力等附加变量;其二,建立区域性加速老化检测数据库,实现材料性能退化规律的跨区域校正;其三,推动微型化原位检测探头的研发,满足植入式医疗器械的实时老化监测需求。随着智能制造2025战略的深入推进,融合数字孪生技术的智能化加速老化检测系统,将成为新材料研发体系的核心基础设施。
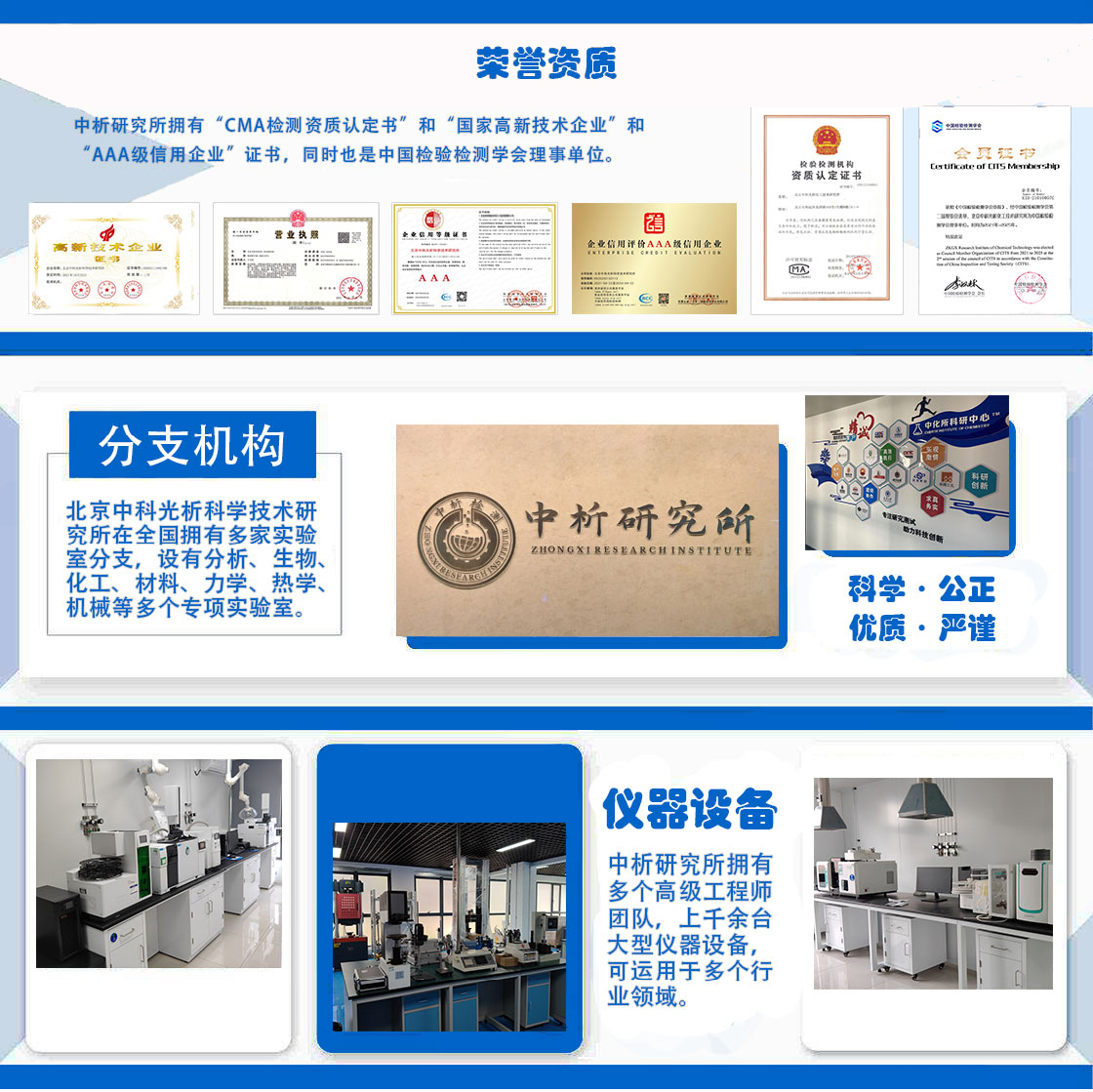
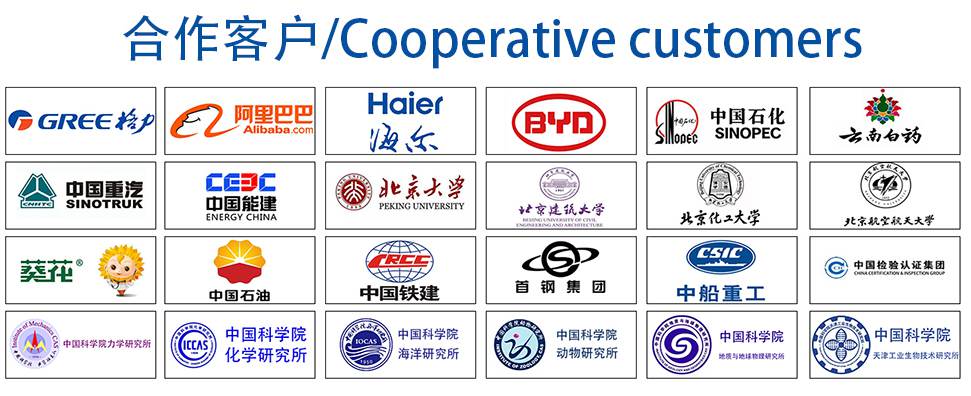