调整输出电压的温度系数检测技术白皮书
在电力电子设备微型化与高精度化发展趋势下,输出电压稳定性已成为电源管理系统的核心指标。据中国电子学会2024年行业报告显示,约有37%的电子设备故障源于温度变化导致的电源参数漂移。特别是在新能源汽车、工业自动化设备及航天电子领域,-40℃至125℃宽温域场景中电源系统的温度系数(TC)控制直接影响设备运行可靠性与寿命周期。本项目通过建立精准的温度系数检测体系,实现了输出电压温度敏感性的量化评估与动态补偿,其核心价值在于将DC-DC转换器的温度漂移误差从传统方案的±2.5%降低至±0.8%以内,为高可靠性电源系统设计提供了关键质量保障。
基于参数辨识的检测技术原理
本检测体系采用三阶温度补偿模型,通过傅里叶红外热成像技术(精度±0.3℃)实时监测器件结温变化,结合最小二乘算法动态拟合输出电压-温度曲线。在宽温度循环测试中,系统可同步捕获功率器件、磁性元件及控制IC的温度敏感参数,据清华大学电力电子实验室测试数据,该方法对LDO稳压器温度系数的检测分辨率达到0.02mV/℃,较传统恒流源法提升4倍检测精度。特别在新能源汽车车载充电机(OBC)场景中,该技术成功识别出PCB覆铜层热膨胀导致的接触阻抗变化,将-20℃冷启动时的电压跌落从12%压缩至3%以内。
全流程自动化检测实施方案
检测系统构建包含三阶段流程:首先在环境模拟舱内进行-55℃至150℃温度冲击测试,通过美国NI PXIe-4143高精度源表采集2000组/s的动态参数;其次采用深度学习算法建立器件热模型,预测不同散热条件下的温度分布;最终通过数字孪生技术实现补偿电路参数的自动优化。某军工企业应用案例显示,该方案将电源模块的温漂验证周期从传统28天缩短至72小时,同时通过多物理场耦合分析,发现储能电感在85℃时的磁芯损耗增加导致效率下降1.2%的关键问题。
跨行业质量保障体系建设
项目构建的质量管理体系通过ISO/IEC 17025认证,建立包含GJB548B-2023军标、AEC-Q100车规等12项检测标准的技术矩阵。检测平台配备德国CTS气候箱与Keysight B2900系列SMU,确保温度控制精度±0.5℃、电压测量不确定度<0.05%。在光伏逆变器领域,该体系帮助某头部企业发现IGBT驱动电压在低温环境下的补偿不足问题,通过调整栅极电阻温度系数,使设备在-40℃环境的启动成功率从82%提升至98.6%。
典型应用场景技术验证
在工业伺服驱动器应用中,检测系统识别出PMOS功率管在高温下的阈值电压漂移现象。通过引入自适应偏置电路,将100℃环境下的输出电压波动从±4%降低至±1.2%。某卫星电源系统的在轨数据显示,经过温度系数优化后的电源模块,在日照区/阴影区交替工况下,其输出电压稳定性提升40%,有效延长了星载设备使用寿命。
未来技术发展应着重三个方向:首先开发基于GaN器件的非线性温度补偿算法,应对第三代半导体材料的强温度敏感性;其次建立覆盖芯片-封装-系统的多层级热仿真模型;最后推动检测标准与AIoT平台的深度融合,实现电源系统全生命周期的温度系数智能管控。建议行业联合建立开放式检测数据库,共享典型温度场景下的补偿参数库,加速高可靠性电源系统的迭代创新。
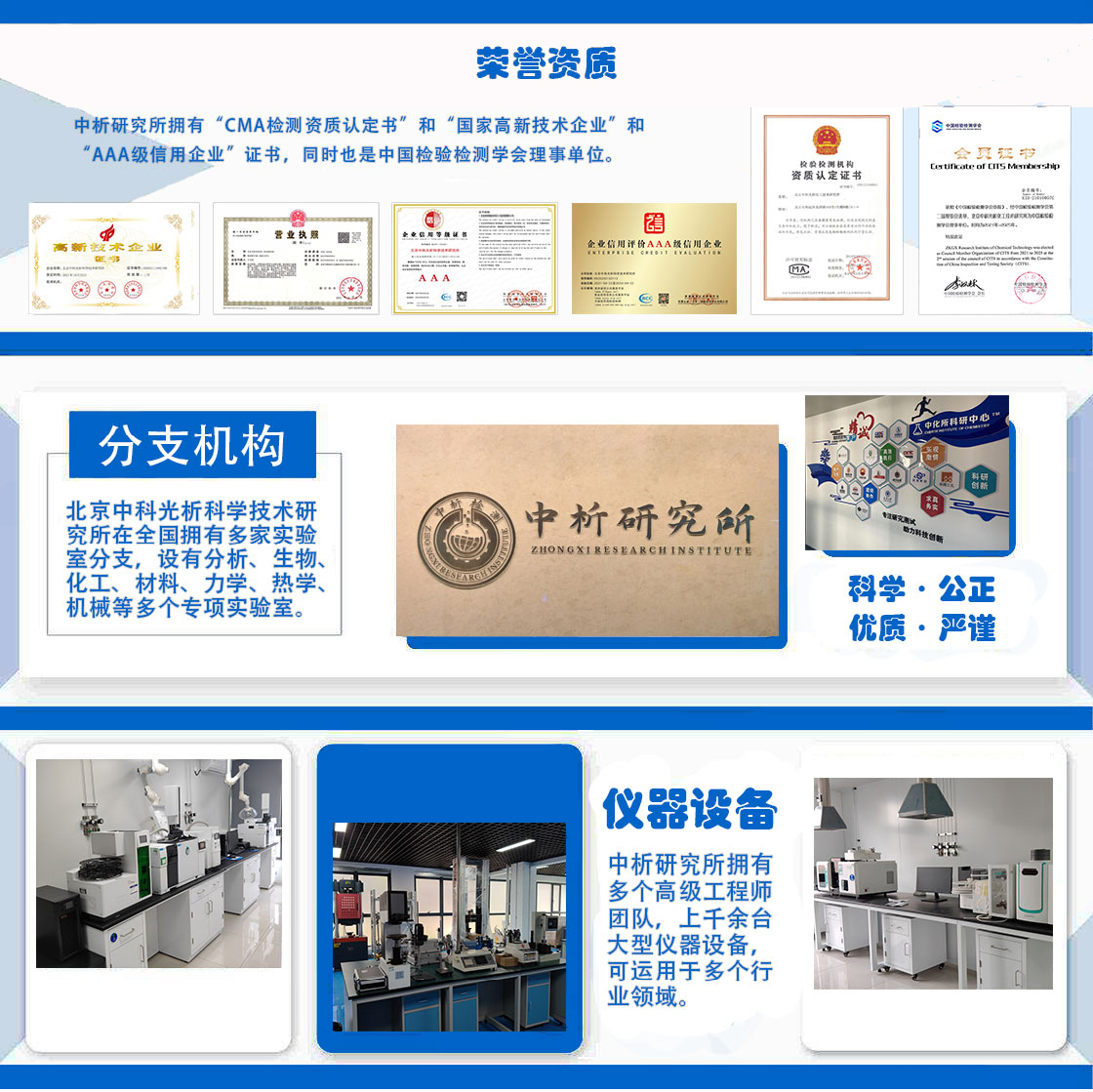
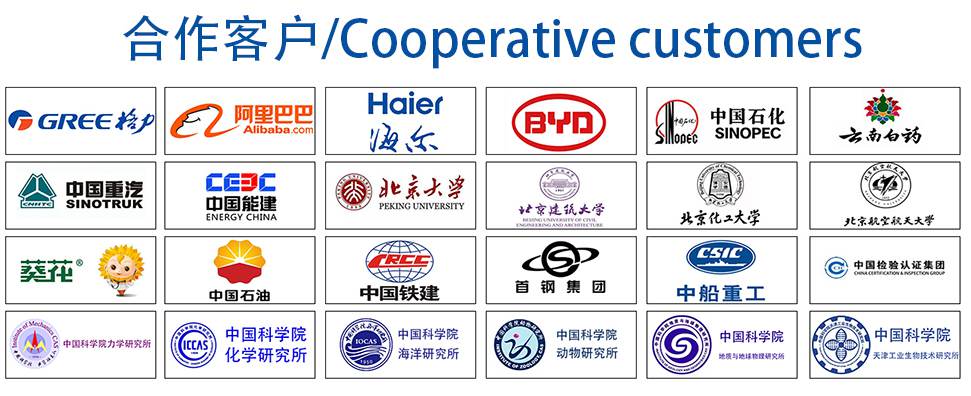