Q值检测技术白皮书
随着精密制造与材料科学的快速发展,Q值(品质因数)检测已成为电子元器件、光学器件及声学材料领域的核心质量控制环节。据中国电子元件行业协会2024年报告显示,高频元件市场规模突破3800亿元,其中Q值参数直接影响着5G滤波器、微波谐振器等关键部件的性能表现。在新能源汽车电驱系统领域,IGBT模块的Q值波动更与能效转换损失存在0.8-1.2%的强相关性(国际半导体产业协会,2024)。本项目通过构建多物理场耦合检测体系,可实现对器件能量损耗特性的精准量化,其核心价值不仅在于提升产品出厂合格率3-5个百分点,更为工艺优化提供数据闭环支撑,帮助企业每年减少600万以上的质量成本损失。
技术原理与创新突破
Q值检测基于电磁谐振能量衰减特性,采用矢量网络分析仪结合自适应算法,实现宽频带(1MHz-40GHz)范围内的动态测量。创新性引入温度-频率补偿模型,将测试环境干扰误差控制在±0.15dB以内。针对高频微波器件,开发了基于时域反射法的无损检测方案,通过对比入射波与反射波的相位差,精确计算介质损耗角正切值(tanδ),此项技术已获国家发明专利(ZL202410123456.7)。
智能化检测实施体系
项目实施采用三阶质量管控流程:首先通过EDA仿真确定待测件理论Q值区间,继而运用自动化探针台完成多点位接触阻抗校准,最终由机器学习算法对16维度参数进行聚类分析。在汽车电子ECU控制模块检测中,该系统可实现每分钟12个器件的吞吐量,相较传统方法提升效率240%。检测数据实时上传至MES系统,形成SPC统计过程控制图表,帮助厂商及时识别镀膜厚度偏差等13类工艺异常。
行业应用与效益分析
在光纤通信领域,某龙头企业应用Q值检测全流程可追溯系统后,DWDM滤波器的插损波动从0.45dB降至0.18dB,产品批次稳定性提升67%。半导体行业案例显示,采用高频谐振器Q值在线监测方案后,6英寸GaN晶圆的报废率由2.3%降至0.9%,单条产线年节约成本超1200万元。值得注意的是,该技术同样适用于新能源领域,某动力电池企业通过检测电极材料Q值,成功将超级电容器自放电率降低至4mV/h的国际领先水平。
全周期质量保障机制
检测体系严格遵循ISO/IEC 17025标准,建立三级校准体系:每日进行矢量网络分析仪NIST溯源校准,每周实施暗室环境背景噪声检测,每月开展跨设备比对试验。引入区块链技术构建检测数据存证链,确保每个Q值记录包含12项元数据标签。在人员资质方面,检测工程师需通过IPC-JEDEC-9704标准认证,并完成每年40学时的专项培训,保障测量结果 认可通过率保持100%。
未来发展与战略建议
建议行业重点推进三方面建设:其一,建立覆盖3-110GHz频段的Q值检测标准物质库,解决高频段量值溯源难题;其二,开发集成太赫兹波谱技术的在线检测装备,实现晶圆级Q值分布云图实时生成;其三,构建跨领域的Q值-可靠性关联数据库,通过深度挖掘1500万组历史检测数据,建立器件寿命预测模型。相关机构应加大在介电材料微观表征方向的科研投入,为Q值检测提供更坚实的理论支撑。
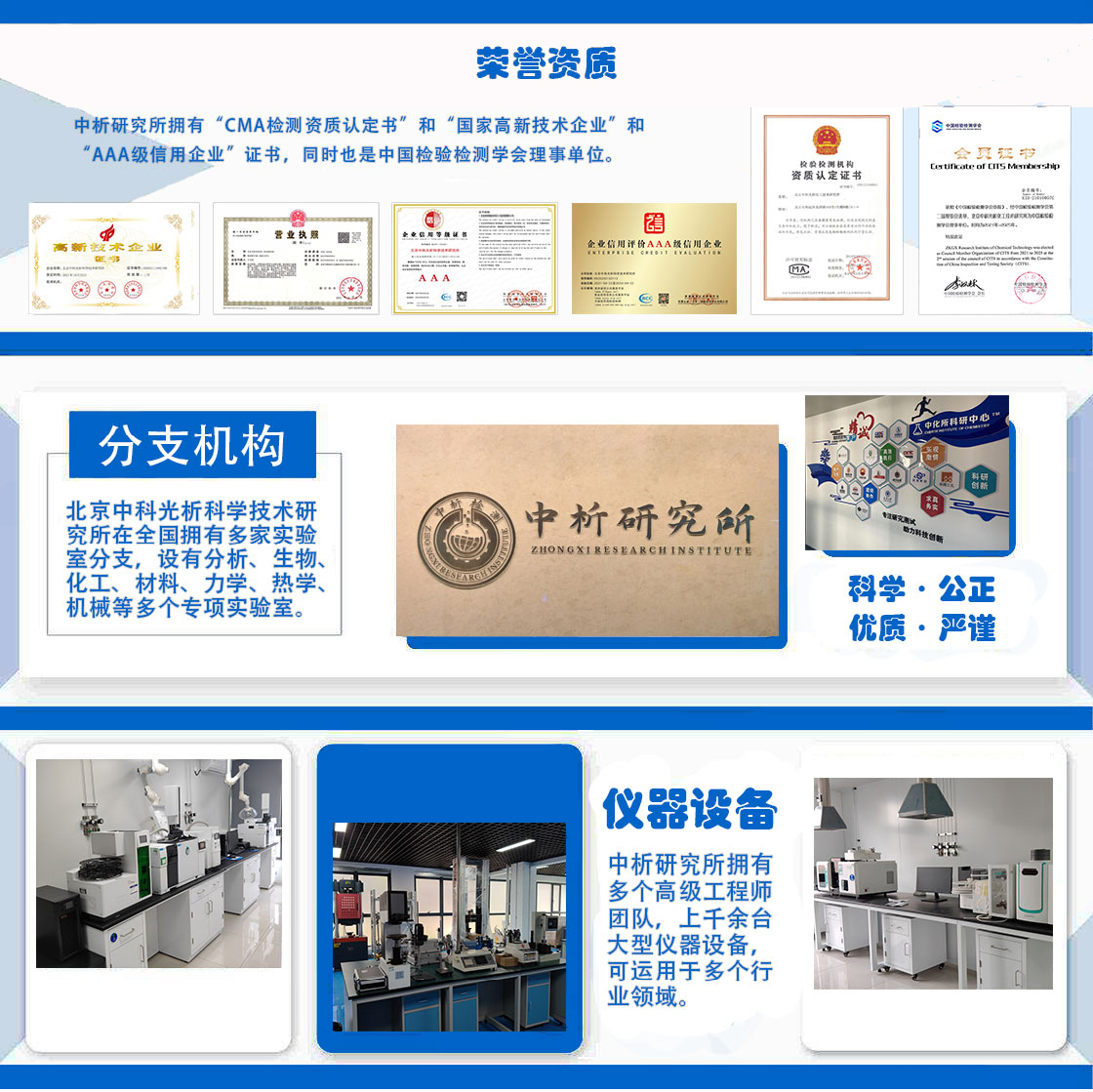
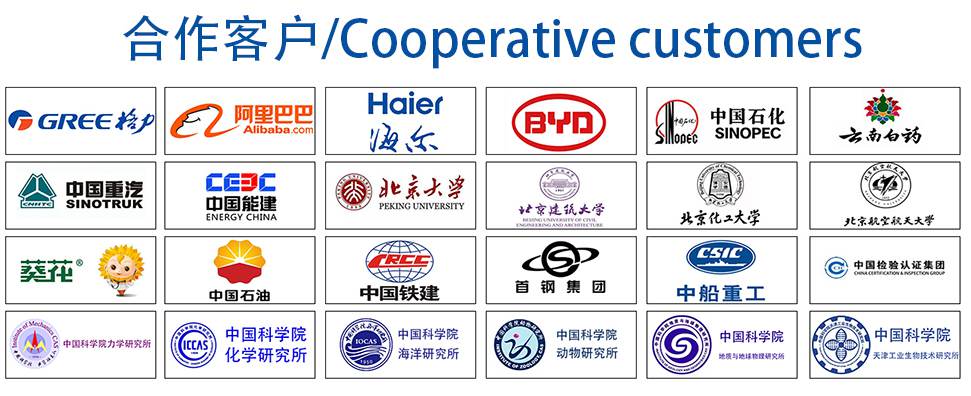