外形结构及尺寸检测
发布时间:2025-07-13 04:19:10- 点击数: - 关键词:
实验室拥有众多大型仪器及各类分析检测设备,研究所长期与各大企业、高校和科研院所保持合作伙伴关系,始终以科学研究为首任,以客户为中心,不断提高自身综合检测能力和水平,致力于成为全国科学材料研发领域服务平台。
立即咨询外形结构及尺寸检测:核心检测项目与技术详解
一、检测目标与意义
- 几何精度:确保形状、尺寸、位置和轮廓的准确性。
- 功能性验证:保证零部件在装配和使用中的兼容性。
- 质量控制:降低废品率,提高产品一致性和可靠性。
二、核心检测项目分类
1. 外形检测
- 表面轮廓:测量曲面的弧度、平整度及复杂三维形状(如汽车钣金件、航空叶片)。
- 边缘特征:检测倒角、棱边锐度、毛刺等(适用于精密机械零件)。
- 对称性:验证轴对称或中心对称部件的对称精度(如齿轮、法兰盘)。
2. 结构检测
- 孔位与槽位:孔径、孔距、槽宽、槽深及位置度(如PCB板钻孔、发动机缸体)。
- 装配配合面:检查接触面的平面度、垂直度和平行度(如机床导轨、轴承座)。
- 焊缝与连接结构:评估焊接接头的几何完整性(如压力容器、管道)。
3. 尺寸检测
- 基础尺寸:长度、宽度、高度、直径、厚度等线性尺寸。
- 形位公差:
- 形状公差:直线度、圆度、圆柱度、平面度。
- 位置公差:位置度、同心度、同轴度、跳动度。
- 角度与倾斜度:斜面角度、锥度、倾斜角(如模具型腔、刀具刃口)。
三、常用检测方法与工具
1. 传统接触式测量
- 工具:游标卡尺、千分尺、高度规、塞规、环规。
- 应用:适用于简单几何特征的手动测量。
2. 光学与影像测量
- 工具:光学投影仪、影像测量仪、激光扫描仪。
- 优势:非接触式测量,适合复杂轮廓和微小零件(如电子元件、注塑件)。
3. 三维扫描与CMM(坐标测量机)
- 技术:通过探针或激光获取三维点云数据,生成数字化模型。
- 应用:高精度检测复杂曲面和自由形状(如航空航天部件、医疗器械)。
4. 自动化检测系统
- 技术:机器人+视觉系统、在线检测设备(如汽车生产线的实时尺寸监控)。
- 优势:提高效率,减少人为误差,适用于大批量生产。
四、质量控制的关键意义
- 降低返工成本:早期发现尺寸偏差,避免后续工序的连锁问题。
- 提升产品一致性:确保批量生产中的零部件互换性。
- 符合行业标准:满足ISO、ASTM、GB等国际或国家标准要求。
五、典型应用领域
- 汽车制造:车身钣金件、发动机缸体、齿轮箱。
- 电子行业:PCB板、半导体封装、连接器。
- 航空航天:涡轮叶片、机身结构件、起落架。
- 医疗器械:人工关节、手术器械、植入物。
六、未来发展趋势
- 智能化检测:AI算法辅助数据分析,实现缺陷自动识别。
- 在线实时监测:集成物联网(IoT)技术,实现生产全流程质量管控。
- 高精度便携设备:手持式三维扫描仪等工具的普及。
上一篇:ESD(静电放电)检测下一篇:满输出电压幅度的上限频率检测
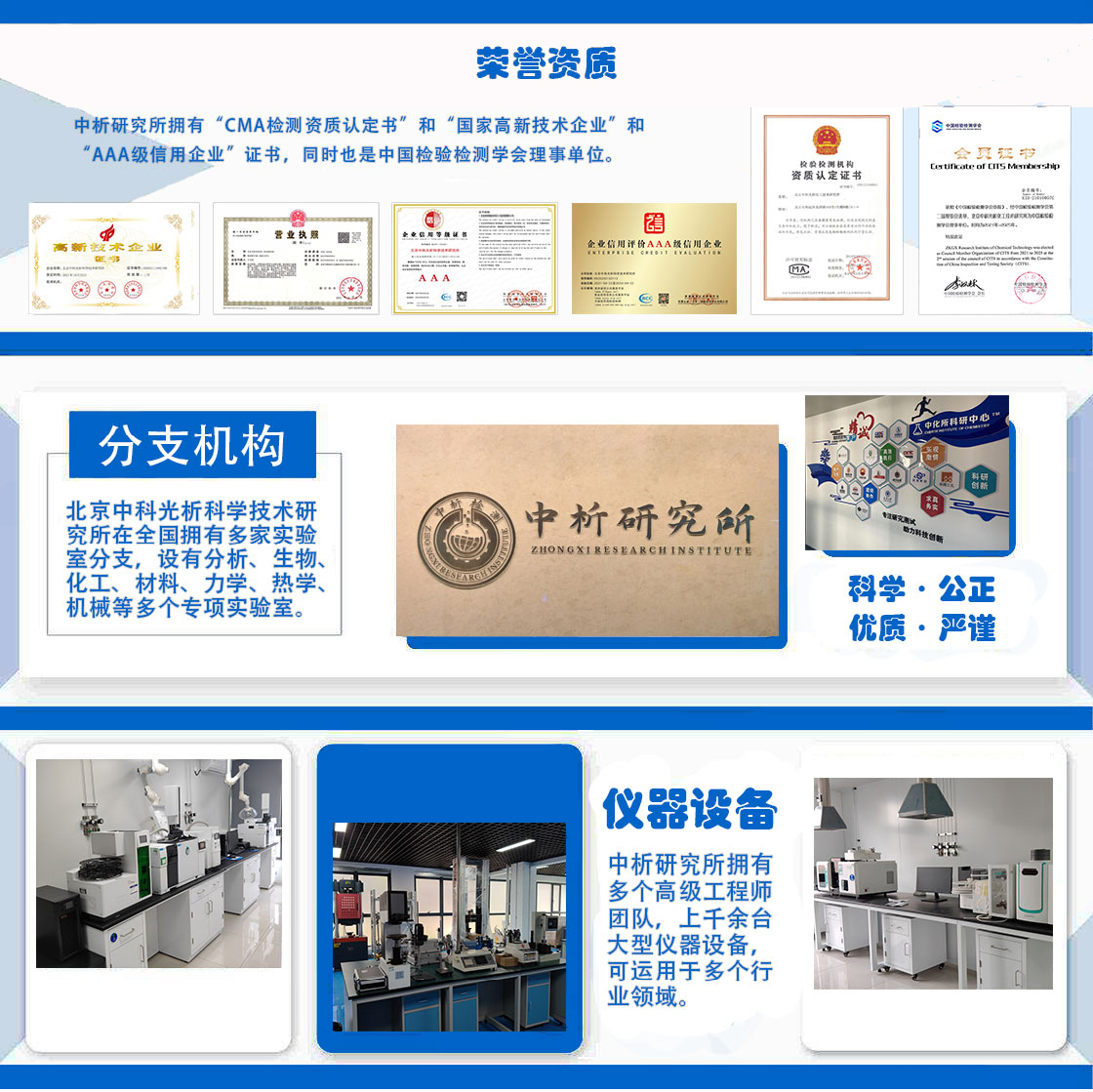
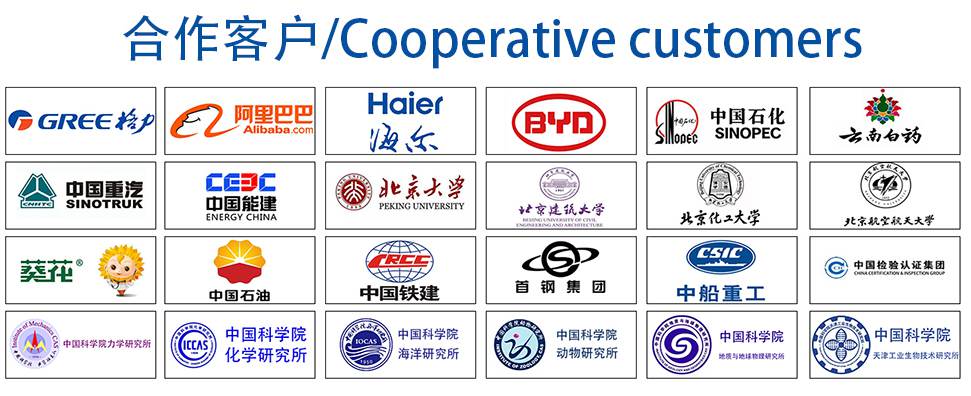
材料实验室
热门检测
297
252
227
237
231
232
246
241
247
256
235
240
237
239
231
229
242
227
242
237
推荐检测
联系电话
400-635-0567