ESD(静电放电)检测
发布时间:2025-07-13 08:00:24- 点击数: - 关键词:
实验室拥有众多大型仪器及各类分析检测设备,研究所长期与各大企业、高校和科研院所保持合作伙伴关系,始终以科学研究为首任,以客户为中心,不断提高自身综合检测能力和水平,致力于成为全国科学材料研发领域服务平台。
立即咨询ESD(静电放电)检测:核心检测项目详解
引言
一、核心检测项目及方法
-
- 目的:模拟人体直接接触设备时的静电放电。
- 方法:使用ESD模拟器(如放电枪)直接对被测设备的金属部件施加放电脉冲。
- 标准:IEC 61000-4-2(测试电压通常为2kV至8kV)。
- 参数:放电次数≥10次,间隔1秒,正负极性均需测试。
-
- 目的:模拟带电体靠近设备时产生的非接触式放电。
- 方法:放电枪接近但不接触设备,通过空气间隙放电(电压可达15kV)。
- 应用:评估绝缘外壳或非导电部件的抗干扰能力。
-
- 目的:确保静电通过接地系统有效释放。
- 工具:接地电阻测试仪。
- 标准:ANSI/ESD S20.20要求接地电阻≤1Ω。
- 对象:工作台、地板、人员佩戴的防静电手环等。
-
- 目的:评估工作区域内的静电场强度是否超标。
- 设备:静电场计或静电电压表。
- 安全阈值:一般要求静电场强<100V/cm。
-
- 方法:将被测物置于法拉第笼内,施加高压后检测内部电场变化。
- 判定标准:屏蔽效能≥30dB(衰减99.9%的电场)。
-
- 目的:评估材料消散静电电荷的速度。
- 标准:ANSI/ESD STM11.11规定消散时间<2秒(从5kV降至50V)。
- 适用对象:防静电地板、包装材料等。
-
- 原理:模拟人体带电(典型电容100pF,电阻1.5kΩ)对器件的放电。
- 标准:JEDEC JS-001(测试等级:Class 0至3A)。
- 应用:半导体器件的ESD耐受能力评估。
-
- MM测试:模拟金属工具放电(电容200pF,电阻0Ω),标准为JESD22-A115。
- CDM测试:评估器件自身带电后的放电耐受性,标准为JESD22-C101。
-
- 表面电阻测试:区分导电(<1×10⁴Ω)、静电耗散(1×10⁴–1×10¹¹Ω)和绝缘材料(>1×10¹¹Ω)。
- 静电衰减测试:依据ANSI/ESD STM11.31,确保电荷快速消散。
二、检测设备与环境要求
- 关键设备:ESD模拟器、静电电压表、表面电阻测试仪、法拉第笼、HBM/CDM测试机台。
- 环境控制:温度23±3°C,湿度40-60% RH(参考ANSI/ESD S20.20)。
三、应用领域
- 电子制造业:PCB、集成电路生产的静电防护验证。
- 汽车电子:车载ECU、传感器的ESD抗扰度测试(ISO 10605标准)。
- 医疗设备:确保生命支持设备在静电环境下的可靠性。
- 航空航天:极端环境下ESD防护(如MIL-STD-1686标准)。
四、
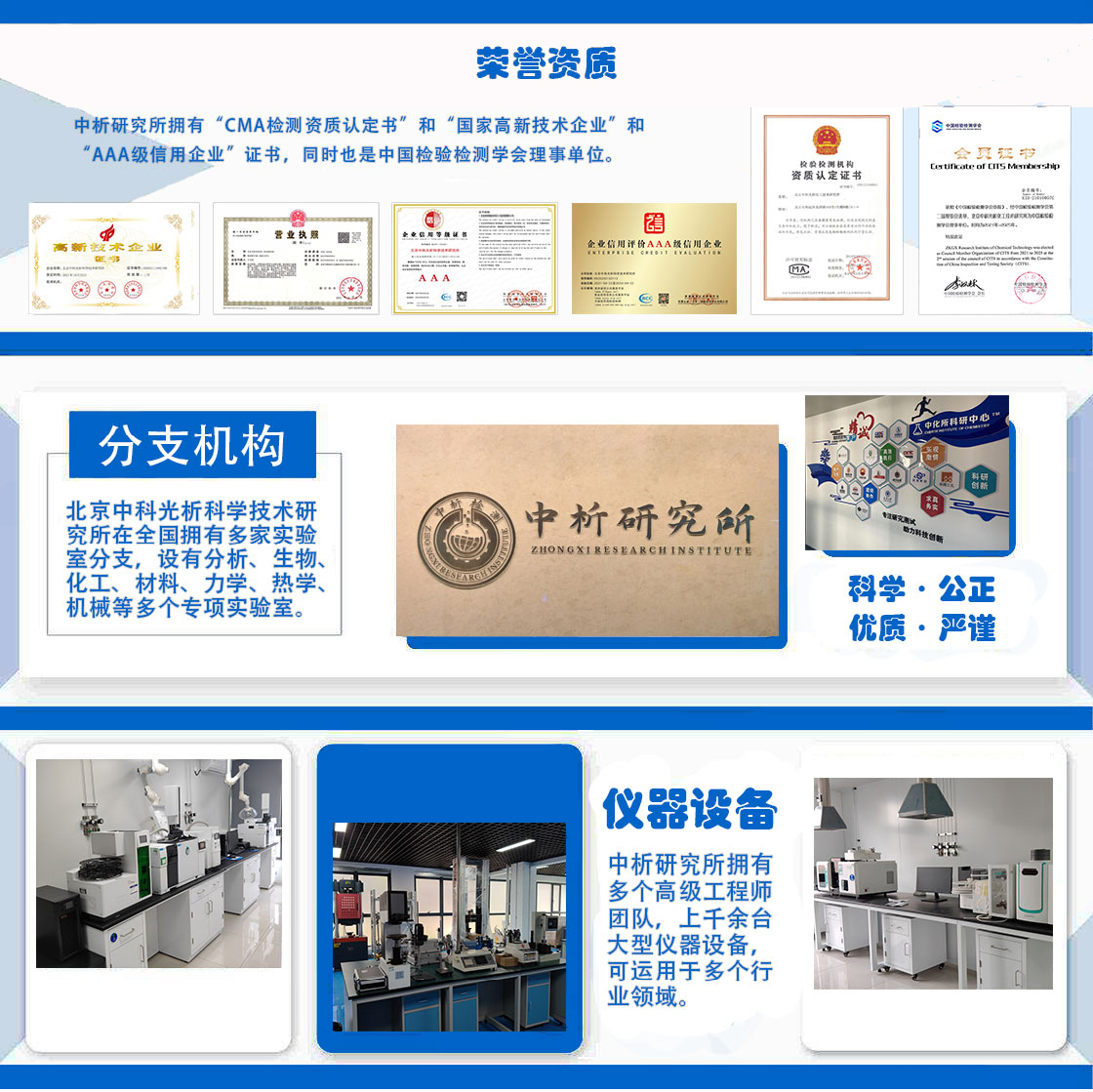
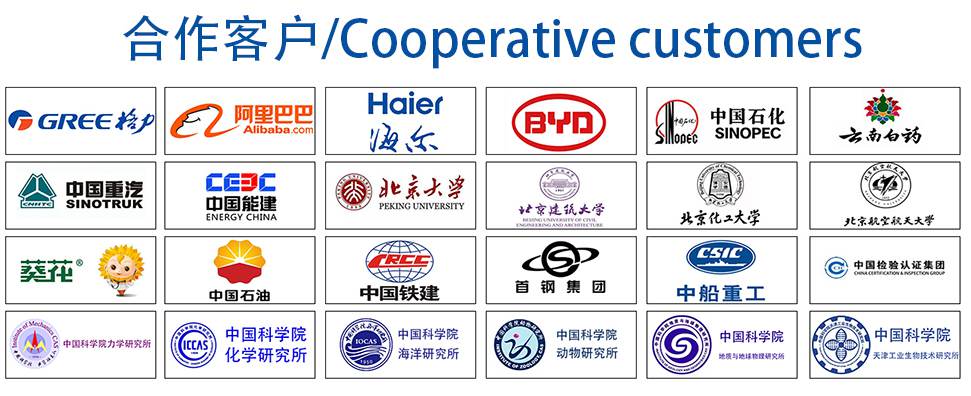
材料实验室
热门检测
297
252
227
237
232
233
246
242
247
256
235
240
238
239
231
229
242
227
242
237
推荐检测
联系电话
400-635-0567