一、检测核心项目解析
1. 电极系统配置
- 电极材质:采用铂铱合金电极(纯度≥99.8%),确保耐电弧腐蚀性。
- 电极间距:遵循IEC 60112标准,固定间距为4.0±0.1mm,角度60°锥形尖端设计以集中电场。
- 接触压力:电极尖端施加1.00±0.05N垂直压力,模拟真实工况下的接触状态。
2. 污染物溶液参数
- 溶液成分:选用0.1%氯化铵(NH4Cl)溶液,电导率调整至23±1mS/m(25℃)。
- 液滴定量:采用微量滴定泵控制滴液速度为30±5秒/滴,误差≤0.1ml,确保污染均匀性。
3. 电压梯度测试
- 起始电压:以25V为步长递增,施加时间≥10秒,观测材料表面电离现象。
- 失效判定:连续50滴溶液下未发生≥0.5A电流或持续燃弧即判定为通过当前电压等级。
4. 环境控制
- 温湿度范围:实验室需维持23±2℃,湿度45%-55% RH,避免冷凝影响表面电阻。
- 气流控制:测试区风速≤0.2m/s,防止液滴挥发速率异常。
二、进阶检测流程
1. 预处理阶段
- 样品经异丙醇超声波清洗后,在标准环境下平衡48小时,消除加工应力及表面污染物。
2. 动态监控技术
- 采用高速摄像机(≥1000fps)记录电痕形成过程,配合红外热像仪监测局部温升(精度±1℃)。
3. 多维度失效分析
- 微观表征:SEM-EDS分析碳化路径元素分布,判断材料降解机制。
- 介电性能追踪:测试前后体积电阻率变化(ASTM D257),揭示绝缘性能衰减程度。
三、关键影响因素深度剖析
-
- 玻纤增强PBT较纯树脂值下降约100V,填料分布均匀性需通过显微CT验证。
- 表面改性处理(等离子体/氟涂层)可使硅橡胶提升30%以上。
-
- 重污染环境(如矿井)需额外进行600V/175滴强化测试,评估极端条件下的耐候性。
-
- 参照IEC 60216进行1000小时热老化(高于Tg 20℃)后复测,降幅>15%视为材料失效。
四、行业应用数据参考
材料类型 | 典型值(V) | 适用标准 | 应用领域 |
---|---|---|---|
阻燃增强PA66 | 375-475 | UL746A | 连接器外壳 |
陶瓷化硅橡胶 | ≥600 | GB/T 6553 | 高压电缆附件 |
无卤阻燃PC/ABS | 250-300 | IEC 60112 | 充电桩组件 |
五、检测技术创新趋势
- 智能算法应用:基于机器学习的电痕路径预测模型,实现失效预警(准确率>92%)。
- 多应力耦合测试:同步施加机械振动(5-2000Hz)与温度循环(-40℃~150℃),模拟复杂工况。
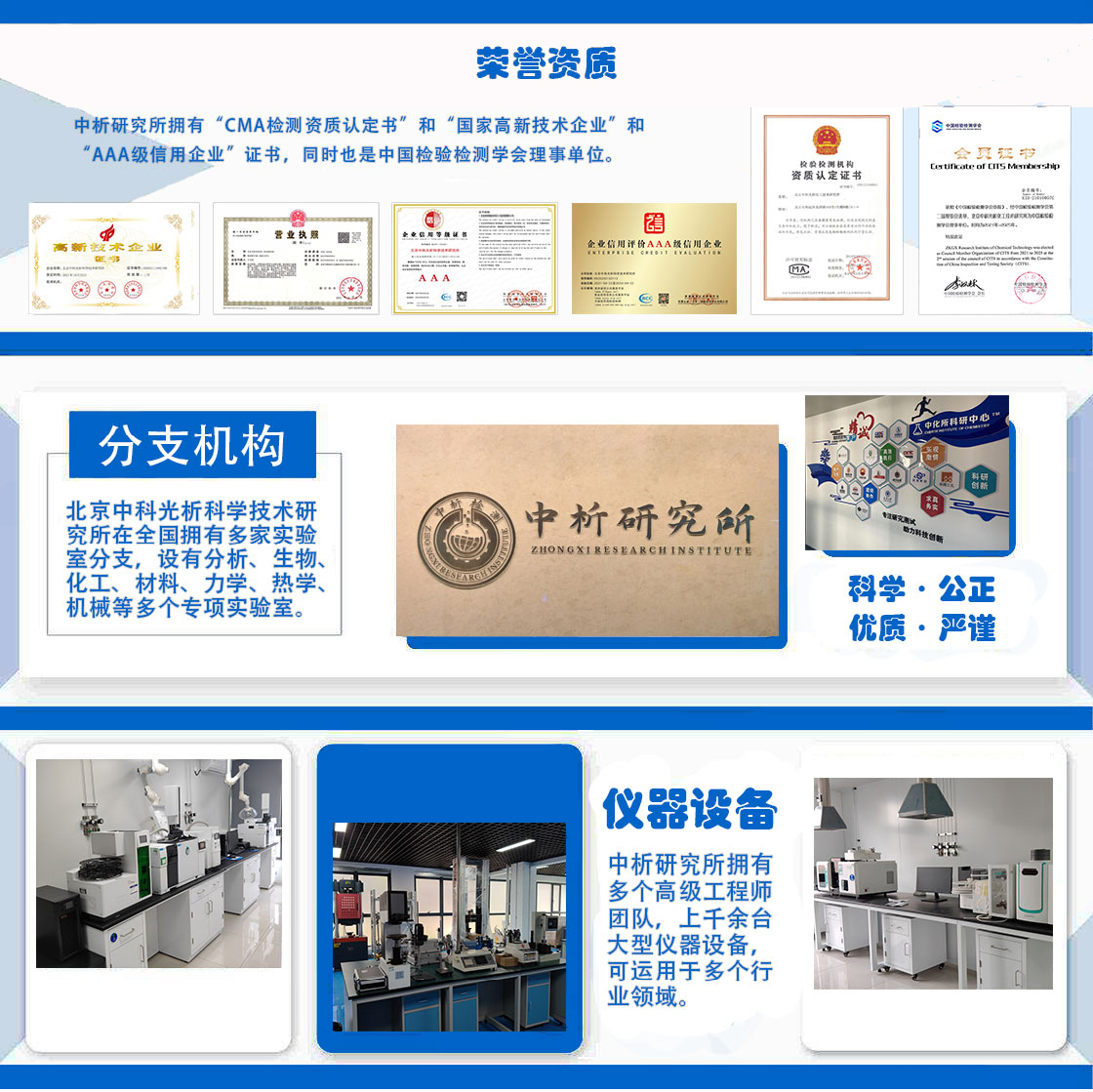
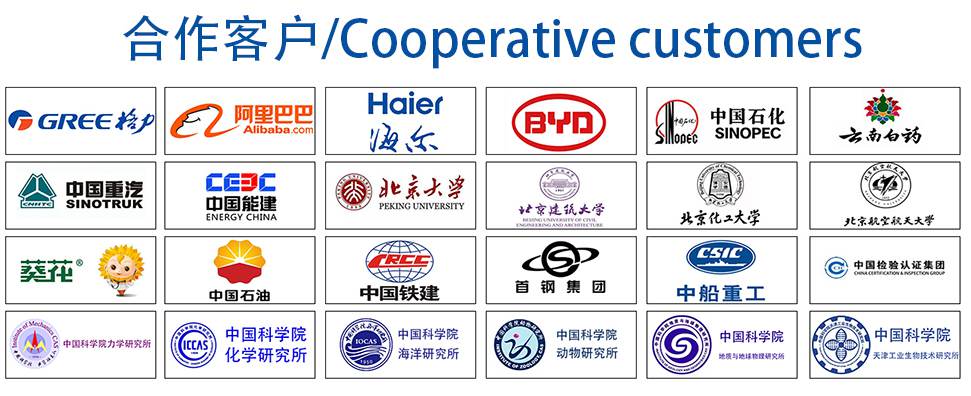
材料实验室
热门检测
254
214
189
203
196
204
209
201
207
215
203
199
197
203
195
193
207
198
207
201
推荐检测
联系电话
400-635-0567