介电强度/耐电压/耐压检测:核心检测项目详解
一、核心检测项目分类
1. 介电强度测试(击穿电压测试)
- 目的:测定材料在电场作用下发生绝缘击穿时的临界电压(kV/mm),反映材料的极限绝缘能力。
- 测试方法:
- 标准电极法:使用圆柱形电极或球状电极对材料施加逐渐升高的电压,直至击穿(如ASTM D149、IEC 60243)。
- 阶梯升压法:按固定时间间隔逐步增加电压,记录击穿瞬间的电压值。
- 关键参数:
- 击穿电压(kV)
- 介电强度(击穿电压/材料厚度,单位kV/mm)
- 适用对象:塑料、橡胶、陶瓷、绝缘油等原材料。
2. 耐电压测试(工频耐压/直流耐压)
- 目的:验证设备或组件在规定时间内承受特定电压的能力,确保绝缘系统无击穿或异常漏电流。
- 测试方法:
- 工频耐压(AC):施加50/60Hz交流电压,持续1分钟(如IEC 60601-1对医疗设备要求)。
- 直流耐压(DC):用于电容类设备(如电缆),避免交流容性电流干扰(标准如IEC 60502)。
- 关键参数:
- 测试电压(通常为额定电压的2-3倍)
- 持续时间(1秒至数分钟)
- 漏电流阈值(如医疗设备漏电流≤0.1mA)
- 适用对象:变压器、电机、开关柜、家用电器等成品设备。
3. 局部放电测试(Partial Discharge, PD)
- 目的:检测绝缘体内部微小放电现象,评估长期运行下的绝缘劣化风险。
- 测试方法:
- 脉冲电流法:通过高频电流传感器捕捉局部放电信号(标准IEC 60270)。
- 超声波/紫外成像法:辅助定位放电位置。
- 关键参数:
- 放电量(pC)
- 放电重复率(次/周期)
- 适用对象:高压电缆、GIS(气体绝缘开关设备)、发电机绕组。
4. 绝缘电阻测试
- 目的:测量绝缘材料或设备的直流电阻,评估其阻止漏电流的能力。
- 测试方法:
- 施加500V或1000V直流电压,读取稳定后的电阻值(标准如IEC 60167)。
- 区分体积电阻率(材料本体)与表面电阻率(污染影响)。
- 关键参数:
- 绝缘电阻值(Ω,通常要求≥1MΩ)
- 适用对象:印制电路板(PCB)、线缆绝缘层、电子元件。
5. 脉冲耐压测试(Impulse Voltage Test)
- 目的:模拟雷击或操作过电压,验证设备耐受瞬态高电压冲击的能力。
- 测试方法:
- 施加标准雷电波(1.2/50μs)或操作波(250/2500μs)(标准IEC 60060-1)。
- 关键参数:
- 波形参数(波前时间/波尾时间)
- 峰值电压(如10kV~200kV)
- 适用对象:避雷器、输电线路绝缘子、电力变压器。
二、测试设备与条件控制
- 设备选型:
- 高压发生器(交流/直流/脉冲)
- 漏电流检测仪
- 局部放电分析仪
- 绝缘电阻测试仪(兆欧表)
- 环境控制:
- 温度:23±2℃(标准实验室条件)
- 湿度:≤65% RH(防止表面凝露影响)
- 样品预处理:清洁干燥,排除表面污染干扰。
三、行业应用差异
行业 | 典型测试项目 | 标准参考 |
---|---|---|
电力设备 | 工频耐压、局部放电、脉冲耐压 | IEC 62271(高压开关柜) |
电子元件 | 绝缘电阻、耐电压 | IPC-4101(PCB基材) |
医疗器械 | 耐电压、漏电流测试 | IEC 60601-1 |
汽车电子 | 直流耐压、温度循环耐压 | ISO 16750-2 |
四、安全规范与失效分析
- 安全要求:
- 测试区域设置隔离屏障,防止电弧伤害。
- 接地保护:确保设备与人员接地可靠。
- 失效判断:
- 击穿:电流骤升或可视放电通道。
- 漏电流超标:超过设定阈值(如医疗设备0.1mA)。
- 失效原因:
- 材料缺陷(气泡、杂质)
- 工艺问题(绝缘层厚度不均)
- 环境老化(潮湿、化学腐蚀)
五、总结
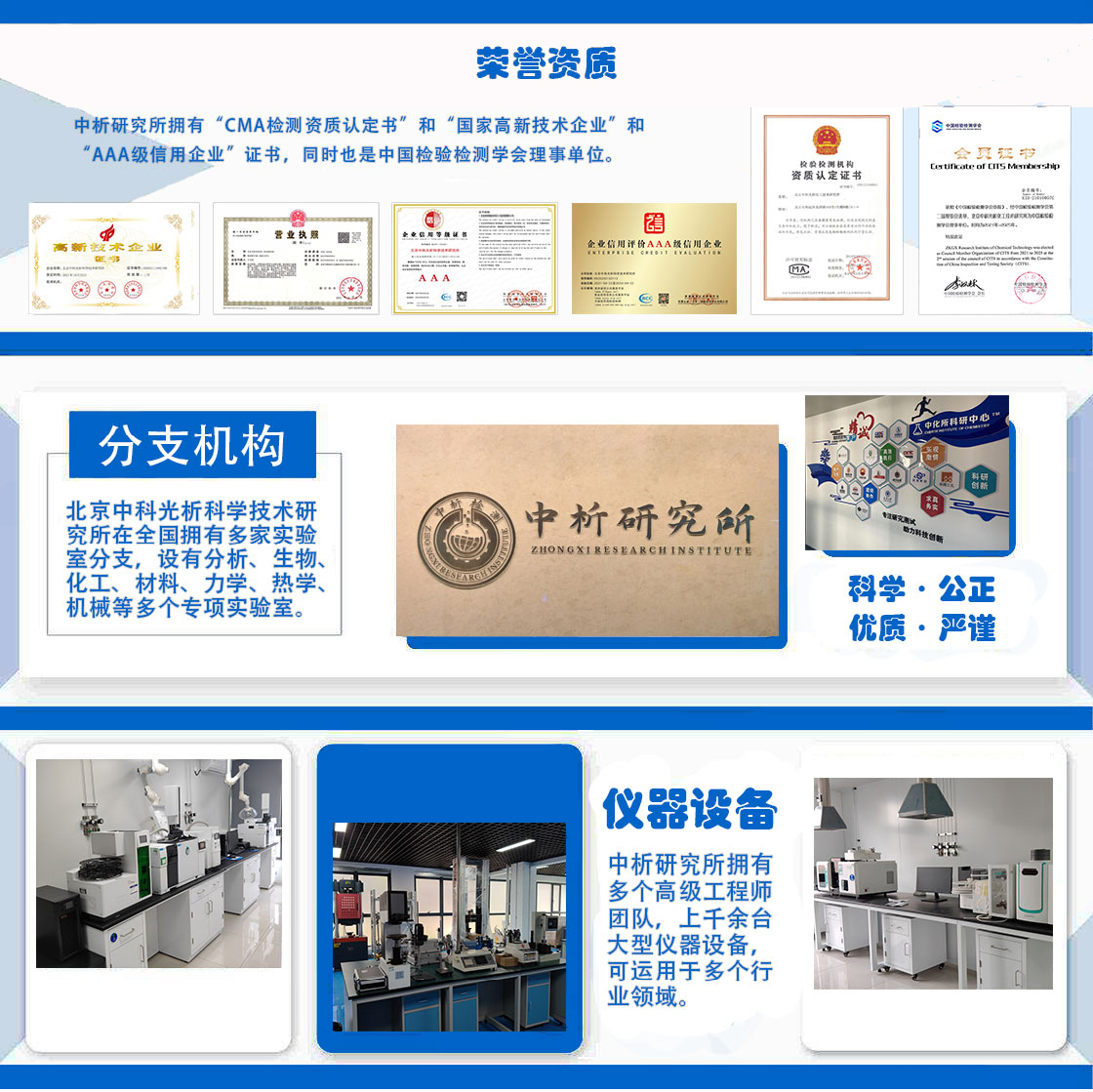
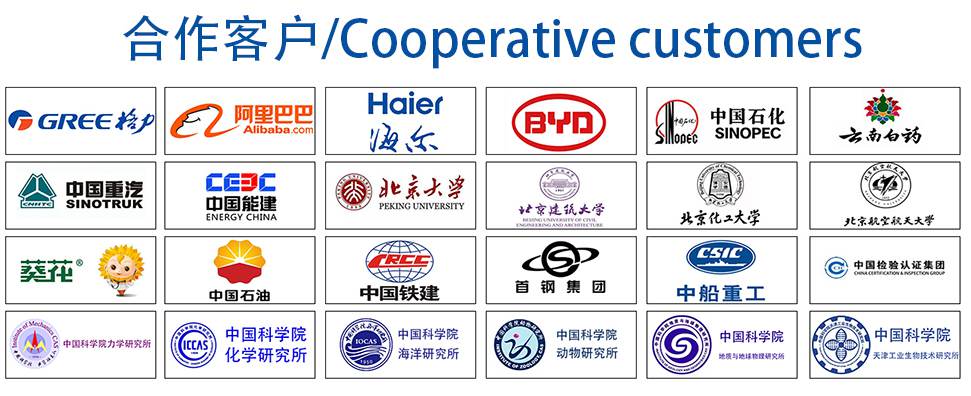
材料实验室
热门检测
251
211
187
201
194
201
206
199
205
212
200
196
192
198
193
189
204
195
204
199
推荐检测
联系电话
400-635-0567