螺纹部件及连接检测:关键检测项目详解
引言
一、几何参数检测
- 检测项:大径、中径、小径、螺距、导程、牙型角(如60°公制螺纹或55°管螺纹)。
- 工具:螺纹千分尺、三针法测量仪、光学投影仪(精度±0.001mm)。
- 标准:ISO 68(公制螺纹)、ASME B1.20.1(管螺纹)。
- 通止规检测:通规(T)应完全旋入,止规(Z)旋入不超过2圈,判定螺纹中径合格性。
- 等级判定:4H/6g(内螺纹/外螺纹)对应不同松紧度等级。
- 激光测距仪:检测有效螺纹长度是否满足国标最小旋合长度(如8倍螺距)。
- 倒角角度:确保30°~45°导入角,避免装配损伤。
二、机械性能检测
- 试验方法:拉伸试验机加载至断裂,记录最大载荷(如8.8级螺栓需≥800MPa)。
- 关键指标:断裂位置(杆部或螺纹根部)反映材料均匀性。
- 扭矩测试仪:模拟实际装配,验证扭矩系数(K=T/(F·d)),控制离散度≤0.03。
- 案例:风电螺栓需施加30%超拧测试,检测抗松弛能力。
- 维氏硬度计:表面硬度(HRC 22-32)与芯部硬度梯度检测,避免氢脆风险。
- 冲击试验:-40℃低温冲击功≥27J(汽车底盘件要求)。
三、表面质量与缺陷检测
- 磁粉探伤:检测裂纹、折叠等表面缺陷(裂纹深度>0.1mm为不合格)。
- 涡流检测:高速分选表面微小缺陷,适用于批量生产。
- 盐雾试验:中性盐雾48小时无红锈(镀锌层≥8μm)。
- 涂层附着力:划格法测试,等级≥4B(ASTM D3359)。
- 金相显微镜:分析螺纹根部晶间腐蚀(如不锈钢在氯化物环境中的点蚀)。
- 轮廓仪:测量服役后螺纹牙型的磨损量(允许磨损≤5%原始高度)。
四、功能特性检测
- 横向振动台:模拟高频振动(频率50Hz,振幅±1.5mm),记录预紧力衰减曲线。
- 评定标准:Junker测试中残余预紧力≥初始值的80%为合格。
- 气压/水压试验:施加1.5倍工作压力,保压5分钟无泄漏。
- 密封剂兼容性:测试生料带/厌氧胶对密封效果的影响。
- 交变载荷试验:加载应力幅(Δσ=±200MPa),记录失效循环次数(如≥10^6次)。
五、材料理化分析
- 光谱分析:检测C、Mn、Cr等元素含量(如SCM435铬钼钢需Cr:0.90-1.20%)。
- 显微镜分析:回火索氏体占比≥90%(10.9级高强螺栓),避免未回火马氏体。
- 延迟断裂试验:施加75%抗拉应力,保持48小时无断裂(ASTM F1940)。
常见问题与对策
上一篇:相比电痕化指数检测下一篇:爬电距离,电气间隙和通过密封胶的距离检测
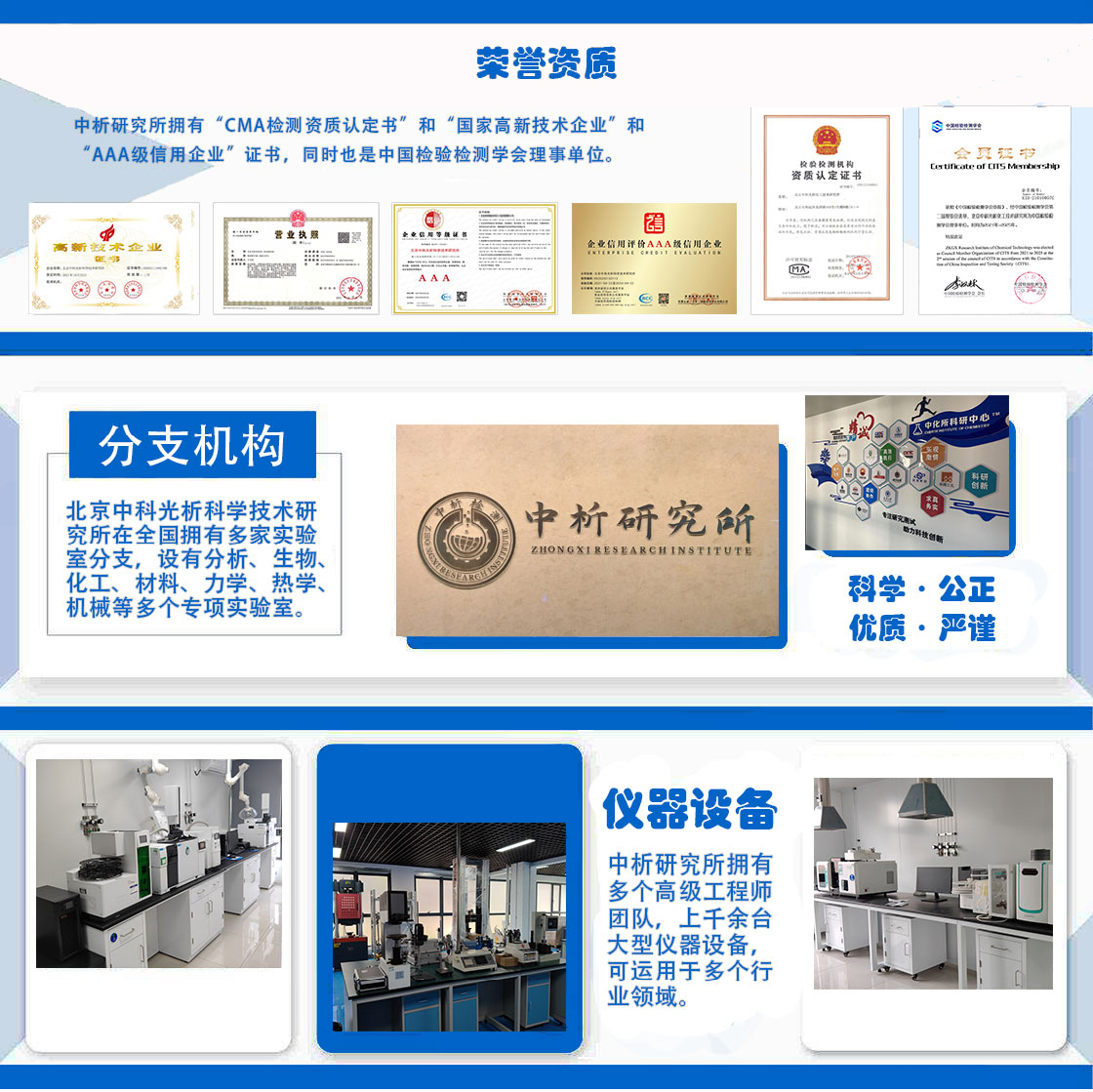
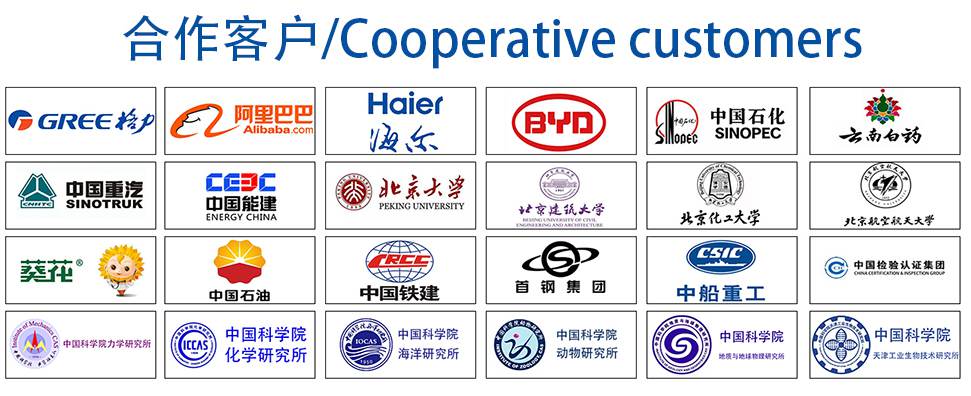
材料实验室
热门检测
251
211
186
201
193
197
205
197
203
210
199
195
192
198
193
189
203
195
204
198
推荐检测
联系电话
400-635-0567