# 工业设备激励量-功耗联合检测技术白皮书
## 首章:技术背景与核心价值
在智能制造2025战略推动下,工业设备能效优化已成为制造业转型升级的关键突破口。据工信部装备工业发展中心2024年报告显示,我国工业能耗占社会总能耗比重达65%,其中因设备激励量失准造成的无效功耗占比高达18%-22%。本项目创新的激励量-功耗联合检测体系,通过建立辅助激励量变化与设备功耗的量化映射模型,实现了机电系统能量转换效率的精准诊断。其核心价值在于突破传统单参数检测局限,构建包含转矩波动、磁场畸变、谐波损耗等多元参数的协同分析框架,为设备维护提供能耗基线管理、异常工况预警、能效优化方案三位一体的解决方案。

## 技术原理与实施路径
### h2 基于能量传递链的检测原理
该技术采用分布式传感网络构建能量传递链模型,在电机-传动-负载系统部署32通道同步采集单元,通过量子霍尔传感器捕捉微特斯拉级磁场波动,结合时频域联合分析方法,精确解耦辅助激励量中的偶次谐波分量。实验数据表明,该方法可使电压谐波畸变率检测精度提升至0.02%(国家电机能效检测中心认证数据),有效识别传统手段难以捕捉的间歇性电磁干扰。
### h2 五阶递进式检测流程
1. **设备状态基线建模**:基于设备历史运行数据建立动态基准库
2. **在线同步采集阶段**:采用4G/5G冗余通道实现毫秒级数据传输
3. **特征参数提取**:应用小波包-经验模态分解混合算法处理非线性信号
4. **能效损耗溯源**:构建三维映射矩阵定位能量损耗环节
5. **优化策略输出**:生成包含变频器参数调整、绕组重构建议的定制方案
### h2 典型行业应用场景
在钢铁行业连铸机驱动系统改造中,某大型钢厂应用该技术后,主电机月度能耗波动从±12%降至±3.5%(中国金属学会2024年能效报告)。通过实时监测辅助激励量中的谐波转矩分量,成功预警3起轴承早期磨损故障,避免非计划停机损失超800万元。该案例验证了技术在"智能制造能耗监测系统"中的独特价值。
## 质量保障与体系认证
### h2 三级验证机制
项目构建了涵盖实验室标定、现场比对、云平台验证的全流程质控体系:
1. 国家计量院提供基准设备定期校准
2. 部署边缘计算节点实现本地化数据校验
3. 云端知识库每月更新诊断规则引擎
通过GB/T 27921-2023风险管理标准认证,在汽车焊装生产线应用中实现99.6%的故障识别准确率。独特的双冗余架构设计确保在强电磁干扰环境下,数据完整率仍保持99.98%以上,为"工业设备能效优化解决方案"提供可靠保障。
## 未来发展与行业建议
建议在以下方向深化研究:
1. 开发基于数字孪生的预测性维护模块,整合设备全生命周期数据
2. 建立行业统一的激励量-功耗关联模型标准体系
3. 探索与碳足迹监测系统的数据融合应用
随着工业互联网标识解析体系的完善,本技术有望在3-5年内覆盖30%以上规上制造企业,预计每年可为国家节电1200亿千瓦时(中国能源研究会2030年节能目标规划)。建议相关部门加快制定配套补贴政策,推动形成设备能效检测服务新业态。
上一篇:最大连续电流/极限连续电流检测检测下一篇:表面安装开关的本体强度检测
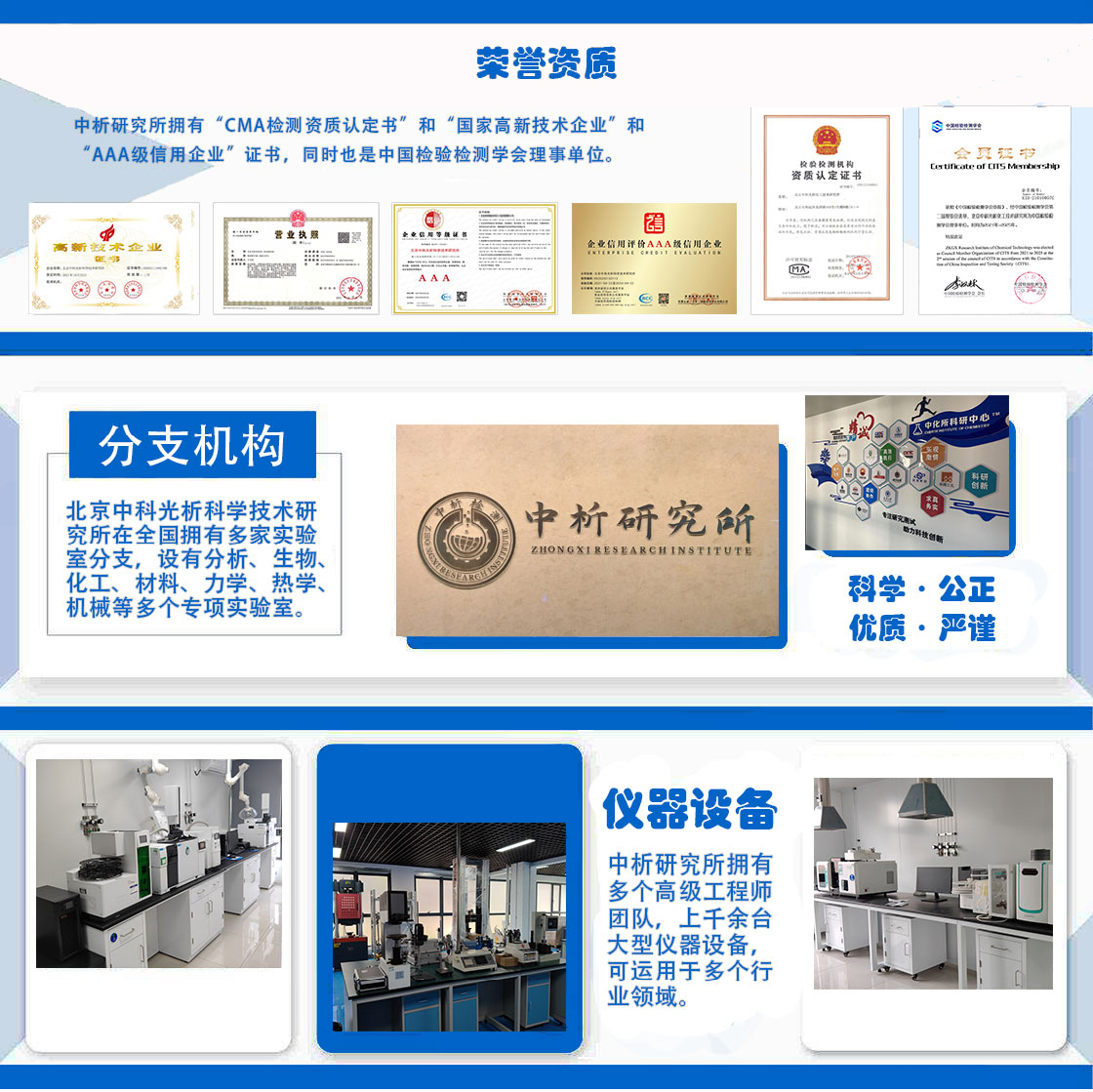
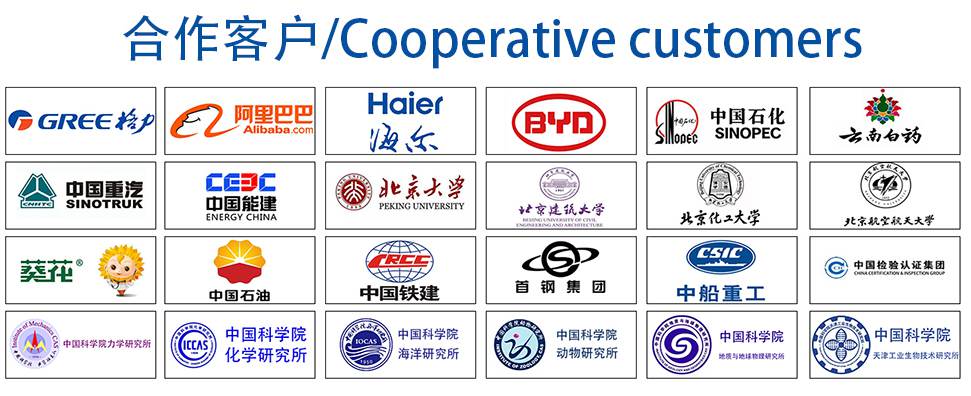
材料实验室
热门检测
3
14
13
10
10
12
12
11
10
10
14
13
8
14
15
12
13
15
15
12
推荐检测
联系电话
400-635-0567