大气环境要求:—低温;—高温;—温度变化;—湿热检测
发布时间:2025-07-12 20:19:28- 点击数: - 关键词:
实验室拥有众多大型仪器及各类分析检测设备,研究所长期与各大企业、高校和科研院所保持合作伙伴关系,始终以科学研究为首任,以客户为中心,不断提高自身综合检测能力和水平,致力于成为全国科学材料研发领域服务平台。
立即咨询大气环境适应性检测项目详解
一、低温检测
- GB/T 2423.1-2008:电工电子产品环境试验 第2部分:低温试验
- IEC 60068-2-1:国际电工委员会低温测试标准
- 设备:高低温试验箱(控温精度±1°C)
- 步骤:
- 预处理:样品在常温下稳定24小时。
- 降温:以≤1°C/min速率降至目标温度(如-40°C)。
- 保持:持续48小时或至热平衡状态。
- 性能检测:实时监测电气性能、机械强度等参数。
- 恢复:常温下静置2小时后复测。
- 电子设备:手机、无人机电池低温放电测试。
- 汽车工业:润滑油在-30°C下的流动性验证。
- 航空航天:卫星组件在太空极寒环境中的可靠性。
二、高温检测
- GB/T 2423.2-2008:高温试验方法
- MIL-STD-810G:军用装备高温测试标准
- 设备:高温老化试验箱(支持循环热风系统)。
- 步骤:
- 升温阶段:以3°C/min速率升至目标温度(如85°C)。
- 恒温保持:持续72小时,模拟长期高温暴露。
- 功能测试:评估散热性能、绝缘电阻等。
- 加速老化:部分产品需进行1000小时以上持续测试。
- 汽车行业:发动机舱线束耐125°C高温测试。
- 光伏组件:太阳能板在85°C湿热双85试验(温度85°C/湿度85%)。
- LED照明:灯具在高温下的光衰及色温稳定性。
三、温度变化检测
- GB/T 2423.22-2012:温度变化试验导则
- JESD22-A104:半导体器件温度循环标准
- 设备:两箱式冷热冲击试验箱(转换时间<1分钟)。
- 步骤:
- 极端温度设定:高温箱(+125°C)与低温箱(-55°C)交替循环。
- 循环条件:每个温区停留30分钟,循环次数≥50次。
- 中间检测:每10次循环后检查外观及功能。
- 失效分析:通过显微观察或X-ray检测内部结构损伤。
- 消费电子:手机主板在-20°C至+60°C循环下的可靠性。
- 军工设备:导弹制导系统在极地到沙漠环境切换的适应性。
四、湿热检测
- GB/T 2423.3-2016:恒定湿热试验
- IEC 60068-2-78:交变湿热测试标准
- 设备:恒温恒湿试验箱(湿度控制范围20%~98%RH)。
- 步骤:
- 温湿度设定:典型条件为40°C/93%RH(双85测试)。
- 循环模式:交变湿热需在25°C至55°C间周期性变化。
- 长期测试:持续21天以上,监测霉菌生长或电解腐蚀。
- 盐雾叠加:部分汽车部件需结合盐雾试验(如GB/T 10125)。
- 海洋设备:船用雷达在95%RH盐雾环境中的耐腐蚀性。
- 医疗器材:呼吸机在湿热条件下的电气安全认证。
上一篇:表面安装开关的底层弯曲检测下一篇:供电电压缓降和缓升检测
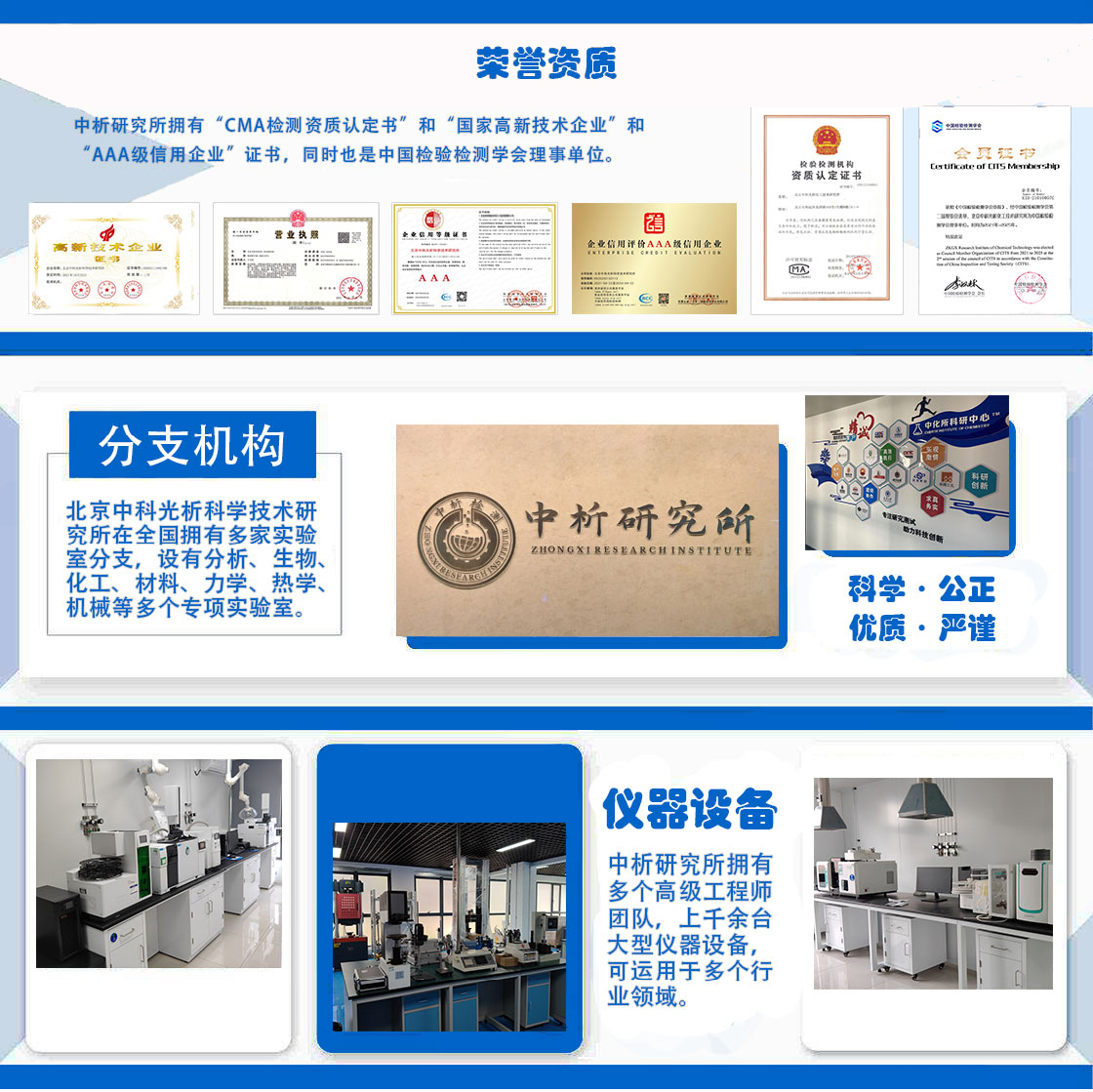
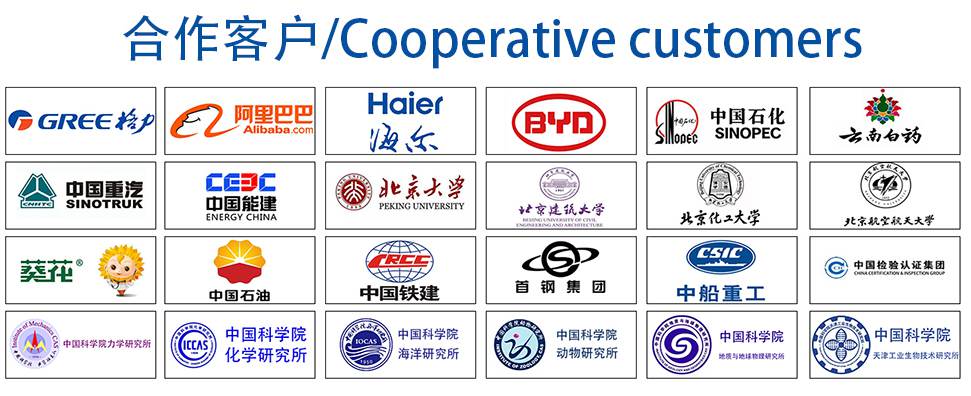
材料实验室
热门检测
297
250
225
236
231
232
246
239
245
253
234
237
237
238
230
228
242
227
242
236
推荐检测
联系电话
400-635-0567