表面安装开关的底层弯曲检测
发布时间:2025-07-13 03:30:32- 点击数: - 关键词:
实验室拥有众多大型仪器及各类分析检测设备,研究所长期与各大企业、高校和科研院所保持合作伙伴关系,始终以科学研究为首任,以客户为中心,不断提高自身综合检测能力和水平,致力于成为全国科学材料研发领域服务平台。
立即咨询一、底层弯曲的主要原因
- 回流焊温度不均匀:过高温度或快速冷却导致基板热应力变形。
- PCB设计缺陷:焊盘布局不对称或基材(FR-4)厚度不足。
- 材料热膨胀系数(CTE)不匹配:开关基材与PCB的CTE差异引发弯曲。
- 机械应力:分板、组装或测试过程中的外力导致形变。
二、核心检测项目
1. 焊点形貌检测
- 检测目标:焊点填充完整性、润湿角度、裂纹或空洞。
- 方法:
- 目检(放大镜/显微镜):观察焊点边缘是否均匀,是否存在虚焊或翘起。
- 自动化光学检测(AOI):通过3D轮廓扫描量化焊点高度差异(精度±10μm)。
- 标准:依据IPC-A-610G Class 2/3,焊点润湿角应<90°,无可见裂纹。
2. 共面性检测(Coplanarity)
- 检测目标:开关引脚与PCB焊盘的贴合度,确保所有引脚同时接触焊锡。
- 方法:
- 激光共面性测试仪:测量引脚高度偏差,阈值通常为±0.1mm。
- 治具接触式检测:使用标准平面治具模拟焊接状态,判定是否通过。
- 标准:JEDEC JESD22-B108规定,共面性误差需<引脚长度的5%。
3. 底层引脚形变分析
- 检测目标:引脚弯曲、扭曲或内缩问题。
- 方法:
- X射线检查(AXI):透视扫描引脚内部结构,识别隐蔽形变。
- 剖面切片(Cross-section):抽样切开焊点,观察引脚与焊锡的结合状态。
- 关键参数:引脚直线度偏差需<0.05mm,焊接后偏移量<焊盘宽度的15%。
4. 基板翘曲度测量
- 检测目标:开关基材或PCB在焊接后的整体平整度。
- 方法:
- 激光翘曲度检测仪:非接触式扫描,输出3D形变热图。
- 热循环测试:在-40℃~125℃环境下循环10次,测量形变量变化。
- 标准:IPC-6012规定,基板翘曲度需<0.75%(板厚≤1.6mm)。
5. 材料性能验证
- 检测项目:
- 玻璃化转变温度(Tg):确保基材耐高温(FR-4 Tg≥140℃)。
- 弹性模量测试:评估基板抗弯曲能力(标准值≥18GPa)。
6. 焊接工艺参数验证
- 检测目标:回流焊温度曲线与底层弯曲的相关性。
- 方法:
- 热电偶实时监测:记录预热、回流、冷却阶段的温升速率。
- 焊后形变对比:对比不同峰值温度(如230℃ vs. 245℃)下的基板翘曲数据。
三、检测流程优化建议
- 制程前预防:
- 使用仿真软件(如Ansys)模拟热应力分布,优化焊盘设计。
- 选择CTE匹配的基材(如高Tg PCB或金属基板)。
- 在线检测整合:
- 在SMT产线中集成AOI+AXI双检系统,实现全自动缺陷分类。
- 数据追溯:
- 建立SPC(统计过程控制)模型,监控关键参数(如共面性CPK≥1.33)。
四、典型失效案例与对策
-
- 根因:PCB散热不均导致局部过热。
- 对策:调整热风回流焊风速分布,降低峰值温度5℃。
-
- 根因:分板应力传递至焊点。
- 对策:改用激光分板或增加应力缓冲槽。
五、总结
上一篇:堵转转矩检测下一篇:大气环境要求:—低温;—高温;—温度变化;—湿热检测
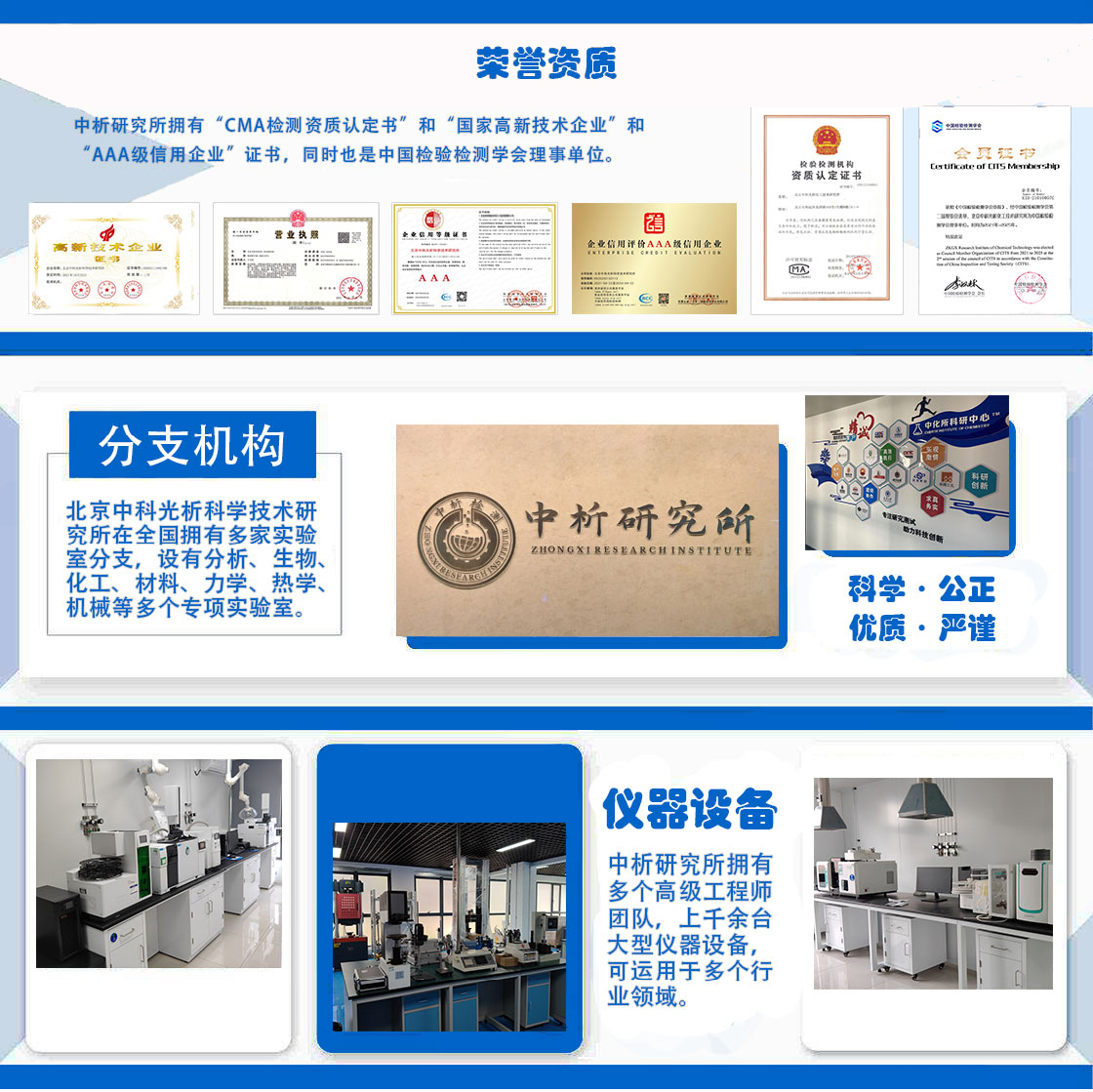
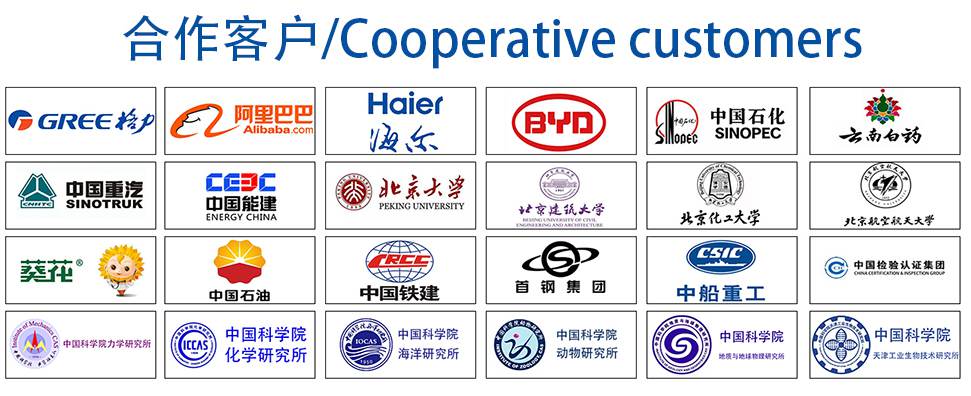
材料实验室
热门检测
297
251
226
237
231
232
246
241
247
256
235
240
237
239
231
229
242
227
242
237
推荐检测
联系电话
400-635-0567