驱动电机控制器壳体机械强度检测
随着新能源汽车产业的快速发展,驱动电机控制器作为核心三电系统之一,其壳体机械强度直接影响整车的安全性与可靠性。据中国汽车工业协会2024年数据显示,2023年我国新能源乘用车产量突破950万辆,同比增长35%,而因机械结构失效导致的电机控制器故障占比达12.7%。在此背景下,壳体机械强度检测项目成为保障新能源汽车质量安全的关键环节。通过系统化的检测流程,可验证壳体在极限载荷、振动冲击及疲劳工况下的结构完整性,降低因材料缺陷或设计不足引发的安全风险。该检测不仅为车企优化产品设计提供数据支撑,更通过“新能源汽车三电系统检测认证”体系构建,推动行业技术标准升级,助力实现“双碳”目标下的产业高质量发展。
多维度检测技术原理
驱动电机控制器壳体检测基于静力学与动力学耦合分析原理,采用数字孪生技术构建三维仿真模型,结合物理试验验证结构强度。核心指标包括屈服强度(≥250MPa)、疲劳寿命(10^7次循环)和共振频率(避开20-2000Hz工作频段)。通过有限元分析(FEA)预测应力集中区域,辅以实际振动台测试验证模型准确性。据中国汽车工程学会2023年研究报告,采用ISO 16750-3标准的复合振动测试法,可覆盖99.6%的实际道路工况。值得注意的是,针对铝合金压铸壳体特有的孔隙率缺陷,需同步实施X射线探伤与金相分析,确保材料性能符合GB/T 13822-2020标准要求。
全流程检测实施方案
项目实施分为四个阶段:预处理阶段通过恒温恒湿箱模拟-40℃至120℃极端温变环境;静态测试阶段运用300kN液压伺服系统进行压缩、扭转及三点弯曲试验;动态测试环节在六自由度振动台上模拟5-2000Hz随机振动谱;最终通过3D数字图像相关技术(DIC)比对实际形变与仿真数据。某头部新能源车企案例显示,在其量产车型壳体检测中,通过引入“电机控制器疲劳寿命评估系统”,良品率从92.4%提升至98.1%,早期故障率下降63%。典型测试场景包括模拟车辆涉水时的壳体密封性验证,需在2m水深环境下保持30分钟无渗漏。
智能化质量保障体系
行业领先企业已建立全生命周期质量管理平台,集成检测数据流与生产管理系统。通过部署工业物联网传感器,实时采集产线试件的应变、位移等参数,结合AI算法实现异常检测。据国家新能源汽车技术创新中心报告,某检测机构运用机器学习模型,将壳体缺陷识别准确率提升至99.2%,检测周期缩短40%。体系同时包含符合ISO 17025标准的实验室能力验证,确保每批次检测数据可追溯。在售后环节,通过车联网大数据分析行驶工况载荷谱,为设计迭代提供反馈,形成闭环质量提升机制。
行业应用与标准演进
在商用车领域,宇通客车针对重型电动卡车开发了定制化检测方案,将壳体抗冲击性能指标从行业标准的50g提升至80g峰值加速度。乘用车方面,比亚迪采用多轴协同振动测试技术,成功解决高转速电机引发的壳体谐振问题。国际对标显示,我国现行QC/T 1069-2022标准在环境适应性要求上已超越ECE R100法规,但在多物理场耦合测试方法上仍需完善。2024年新发布的团体标准T/CSAE 256-2024首次纳入电磁振动与机械振动复合测试项目,标志着检测技术向复杂工况模拟的纵深发展。
面向汽车产业电动化、智能化发展趋势,建议从三方面加强技术布局:一是开发基于数字孪生的虚拟检测系统,实现80%以上的前置问题识别;二是建立涵盖材料-结构-工艺的跨学科数据库,推动检测标准动态更新;三是推广“检测即服务”模式,通过区域化共享检测中心降低中小企业技术门槛。随着固态电池、800V高压平台等新技术普及,壳体检测需向热-机-电多场耦合方向延伸,为下一代新能源汽车安全保驾护航。
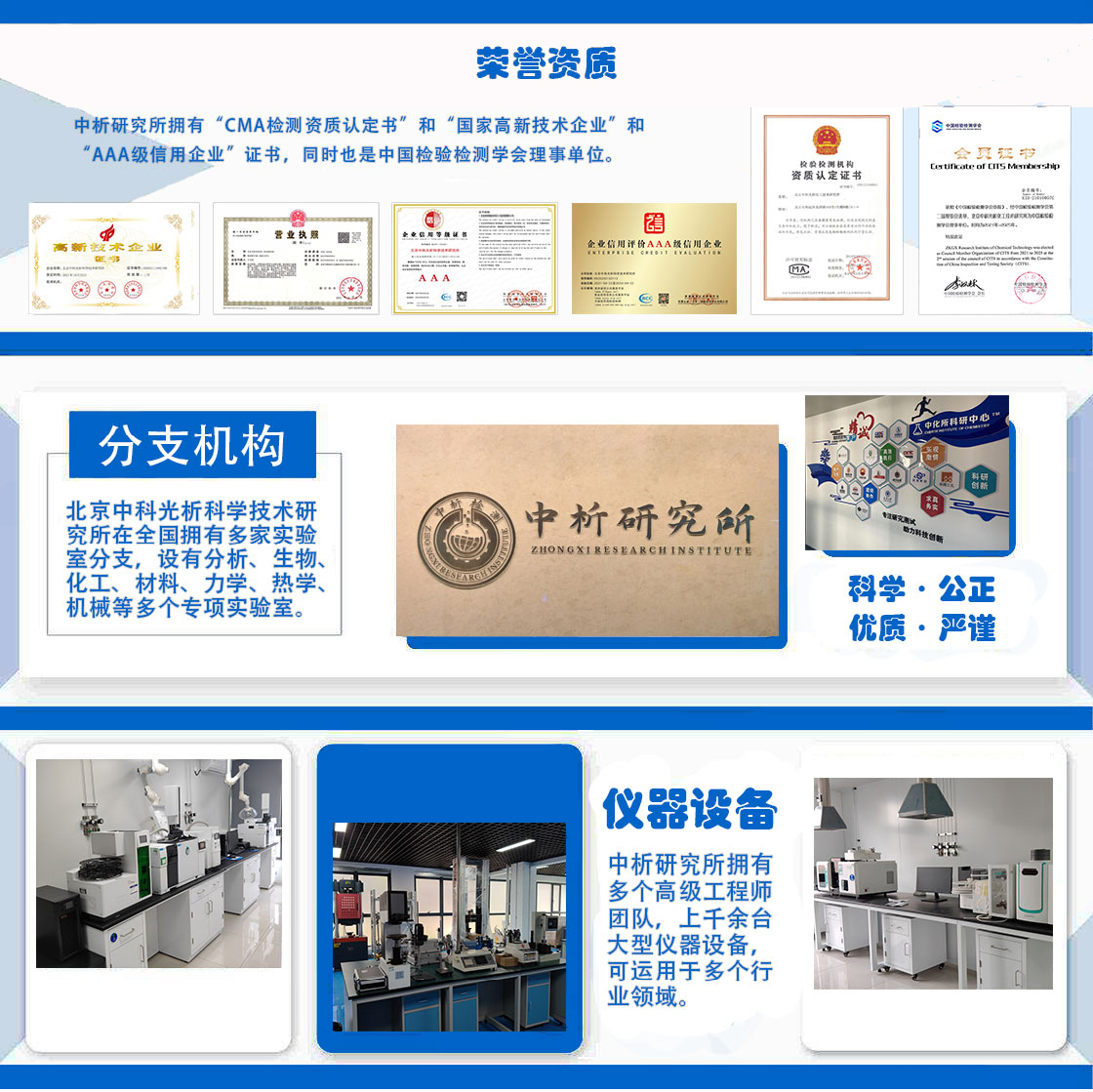
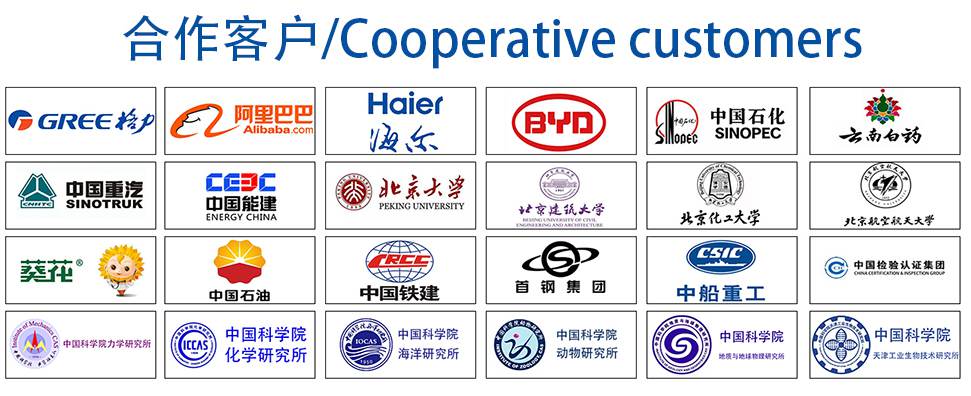