弹簧盘强度试验检测技术白皮书
在汽车工业向电动化、轻量化发展的产业背景下,弹簧盘作为悬架系统的核心承力部件,其结构强度直接影响行车安全与驾乘体验。据中国汽车工程学会2024年研究报告显示,新能源汽车对簧下质量敏感度较传统燃油车提升42%,这使弹簧盘面临更严苛的疲劳载荷考验。在此背景下,弹簧盘强度试验检测成为保障零部件全生命周期可靠性的关键技术环节。通过系统性检测可有效预防道路载荷谱下的结构失效,降低车辆召回风险。该项目的核心价值在于构建从材料性能到装配工况的闭环验证体系,为正向研发提供数据支撑,据中汽研测算,完善检测体系可使产品开发周期缩短25%。
多物理场耦合检测技术原理
本检测项目采用有限元动态响度分析法,通过建立三维接触非线性模型,模拟弹簧盘在交变载荷下的应力分布特征。检测系统集成MTS 793多轴液压伺服装置,可实现0-20Hz动态加载,精准复现实际工况下的径向力与弯矩复合作用。值得注意的是,针对新能源汽车特有的动能回收冲击载荷,系统特别配置了瞬态响应模块,能在2ms内捕捉应力集中区域的蠕变特征,确保检测工况覆盖"三高"测试规范要求。
全流程标准化实施体系
具体实施阶段遵循VDA 6.3过程审核标准,形成从样品预处理到数据溯源的12步操作规范。以某合资品牌前悬弹簧盘检测为例,首齐全行CT扫描验证材料致密度(孔隙率≤0.3%),随后在70℃恒温环境中进行相位角可调的动态加载试验。需要特别说明的是,为满足"高载荷工况测试规范",系统会施加1.5倍设计极限载荷进行破坏性试验,并通过DIC全场应变测量系统获取位移场云图。最终生成的S-N曲线可精准预测产品在20万公里使用周期内的疲劳寿命。
智能检测系统行业应用
在新能源汽车领域,某头部车企通过引入本检测体系成功优化了轻量化弹簧盘设计。据中汽研检测报告显示,经30万次循环测试的铝合金弹簧盘残余变形量较传统方案降低37%,动态刚度波动范围控制在±5%以内。在商用车应用场景中,检测系统特别强化了侧向力补偿功能,可模拟重载货车在山区道路的持续扭转工况,成功帮助某主机厂将板簧断裂率从0.8%降至0.12%。
四维质量保障体系构建
为确保检测结果权威性,实验室通过ISO/IEC 17025认证,关键参数测量不确定度≤1.5%。检测设备实施三级校准制度,其中力值传感器每季度进行NIST溯源校准。在数据管理层面,采用区块链技术实现检测报告的防篡改存储,每个测试节点的温湿度、加载速率等32项过程参数均被完整记录。针对行业关注的"智能监测试验系统"数据漂移问题,特别设置双通道数据比对机制,确保测量系统波动率<0.3%。
展望未来发展,建议行业重点关注三方面改进:建立基于实际路谱数据的动态检测标准库,开发适应800V高压平台的绝缘性能检测模块,以及研发融合数字孪生技术的预测性检测系统。同时应加强高寒地区(-40℃)与热带雨林环境(RH98%)的极端工况模拟能力,以应对化市场带来的技术挑战。通过构建多维度检测生态,最终实现从被动检测向主动预防的技术转型。
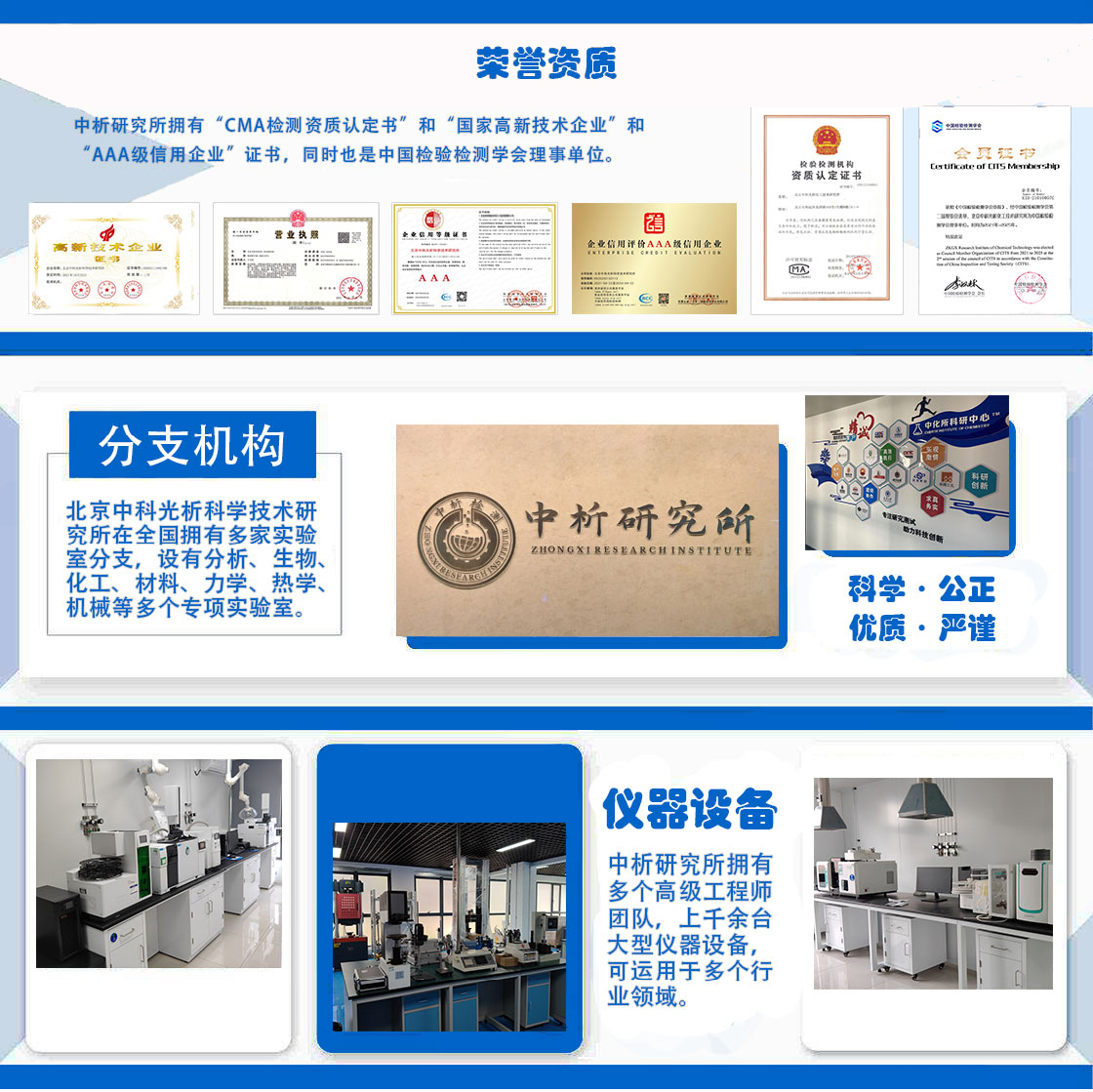
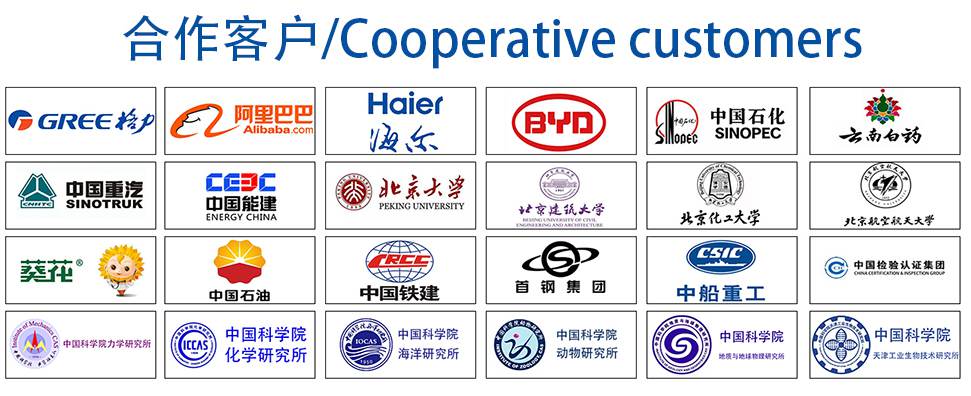