温度循环(空气-空气)检测:核心检测项目与技术解析
引言
检测原理
核心检测项目清单
1. 温度范围设定
- 测试目标:验证产品在极限高温(如+85°C)和极限低温(如-40°C)下的耐受性。
- 标准参考:MIL-STD-810G(方法501.5)、IEC 60068-2-14。
- 参数选择:需根据产品实际使用环境(如汽车级要求-40°C至+125°C)确定上下限温度。
2. 循环次数与驻留时间
- 测试目标:评估产品在长期温度交替下的稳定性。
- 典型参数:
- 单次循环:高温驻留30分钟 → 降温至低温 → 低温驻留30分钟 → 升温完成一次循环。
- 总循环次数:500~1000次(视产品寿命要求而定)。
- 失效判定:出现性能参数偏移(如电子器件电阻值变化超过±10%)或物理损伤(如开裂)即判定失效。
3. 温度变化速率
- 测试目标:模拟实际环境中温度骤变的冲击效应。
- 控制要求:
- 传统空气-空气法:5~15°C/min(如IPC-9701标准建议10°C/min)。
- 液态氮辅助快速温变:可达30°C/min以上(需特殊设备)。
4. 温度均匀性监测
- 测试目标:确保测试箱内温度分布符合标准(避免局部过热/过冷)。
- 检测方法:在样品区布置热电偶矩阵,验证箱内各点温差不超过±2°C(依据IEC 60068-3-5)。
5. 功能与性能验证
- 在线监测项目:
- 电气性能:通电状态下实时监测电压、电流、信号完整性(如高速PCB的信号失真率)。
- 机械性能:结构件形变、连接器插拔力变化、密封性测试(如IP等级验证)。
- 标准方法:JEDEC JESD22-A104E(针对半导体器件)。
6. 失效模式分析(Post-Test FA)
- 检测项目:
- 显微观察:通过SEM/EDS分析焊点裂纹、金属迁移现象。
- 断面分析:检测PCB分层、涂层剥落等缺陷。
- 热成像:定位异常发热点(如虚焊导致的局部高温)。
7. 湿度叠加测试(可选)
- 复合测试:在温度循环中引入湿度控制(如85°C/85%RH),加速评估材料吸湿膨胀效应(参考JESD22-A101)。
测试流程示例
- 预处理:样品在标准温湿度下稳定24小时。
- 初始检测:记录外观、电气参数基线数据。
- 循环执行:按设定参数运行指定次数,每50次暂停并检测中间数据。
- 最终检测:对比性能退化程度,进行失效分析。
应用领域与案例
- 汽车电子:发动机ECU需通过-40°C至+125°C、1000次循环测试(ISO 16750-4)。
- 航空航天:卫星组件需验证-65°C至+150°C下的真空兼容性(ECSS-Q-ST-70-04C)。
- 消费电子:手机主板需通过500次-20°C至+70°C循环,确保BGA焊接可靠性。
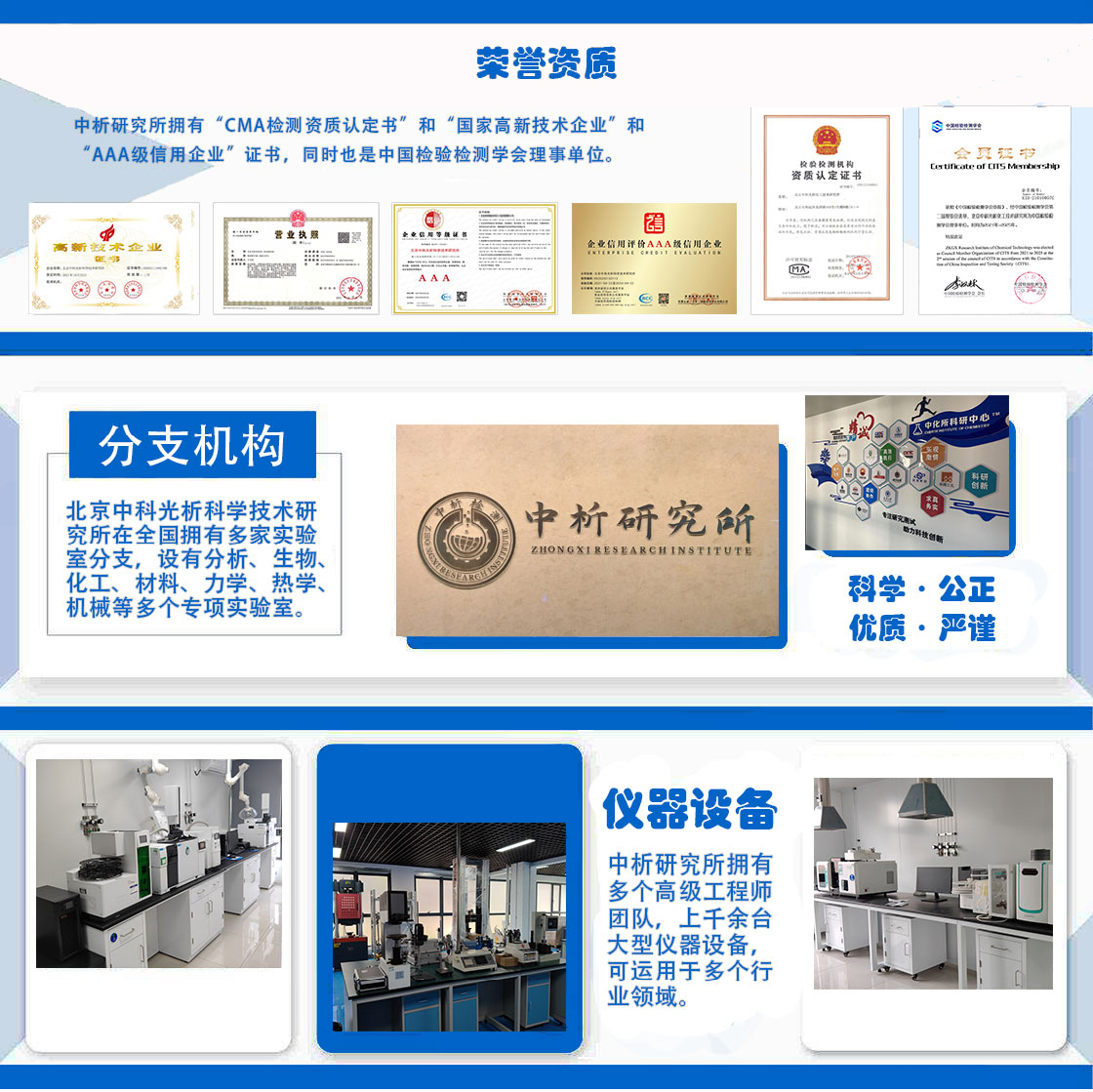
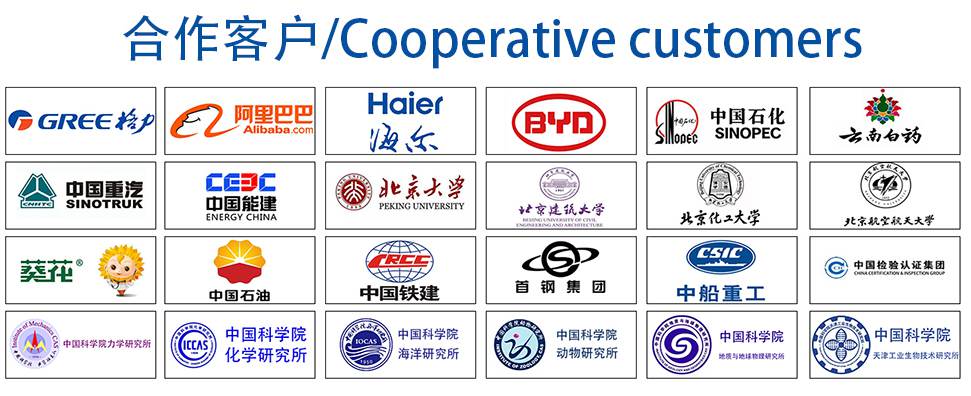
材料实验室
热门检测
264
221
199
207
201
206
216
208
216
221
208
207
211
208
201
199
213
204
211
206
推荐检测
联系电话
400-635-0567