高速性能试验检测项目全解析
一、 动力总成效能试验
- 加速响应测试:80-120km/h全油门再加速时间测量,检验变速箱降档逻辑及涡轮增压系统响应速度
- 连续高速巡航试验:在85%最高车速工况下持续运行2小时,监测发动机水温、机油温度、涡轮增压器温度变化曲线
- 动力热衰减测试:通过10次连续0-100%油门开度循环,记录马力机输出功率衰减幅度,要求不超过标称值5%
二、 高速制动效能验证
- ABS效能测试:在μ-split路面上进行120km/h紧急制动,记录方向盘扭矩波动范围控制在±5Nm以内
- 制动盘热衰退试验:连续10次100-0km/h全制动后,测量制动距离增量不得超过首次的15%
- 电子驻车动态测试:80km/h行驶中触发EPB,验证系统是否拒绝误操作并保持行车稳定性
三、 空气动力学验证体系
- 风洞气动测试:在1:1整车风洞中获取Cd值,同时监测升力系数不超过0.15
- 高速横风响应:侧风发生器模拟90km/h横风,车辆以120km/h通过时方向盘修正角度应≤5°
- 气动声学风噪测试:120km/h工况下A柱区域风噪不超过68dB(A)
四、 底盘动态稳定性试验
- 蛇形穿桩测试:110km/h通过间距50m的18个桩桶,ESP介入频率不超过3次/秒
- 变道稳定性试验:80-120km/h瞬态变道,横摆角速度延迟应<0.1秒
- 转向回正测试:100km/h松手后,车辆应在3秒内自动回正且残存横摆角<2°
五、 热管理系统验证
- 持续爬坡试验:载重75%条件下以60km/h连续攀登10%坡度山路,冷却液温度应稳定在95-105℃区间
- 涡轮增压器冷却测试:连续高速行驶后停机,监测增压器冷却系统持续工作时间≥15分钟
- 电池热管理验证:电动车120km/h巡航时,电池温差控制在±2℃以内
六、 NVH性能专项检测
- 传动系共振测试:在80-140km/h范围内扫描变速箱阶次振动,要求座椅导轨振动量<0.6m/s²
- 轮胎空腔噪声:通过车内声学摄像头定位200-250Hz频段噪声源
- 高频风噪分析:采用声学阵列定位后视镜、天窗等部位的湍流噪声源
- LKA车道保持系统在120km/h时的纠偏响应时间
- ACC自适应巡航在高速跟车时的制动平顺性
- 自动变道辅助系统的车速适应范围验证
上一篇:微耕机检测下一篇:温度循环(空气-空气)检测
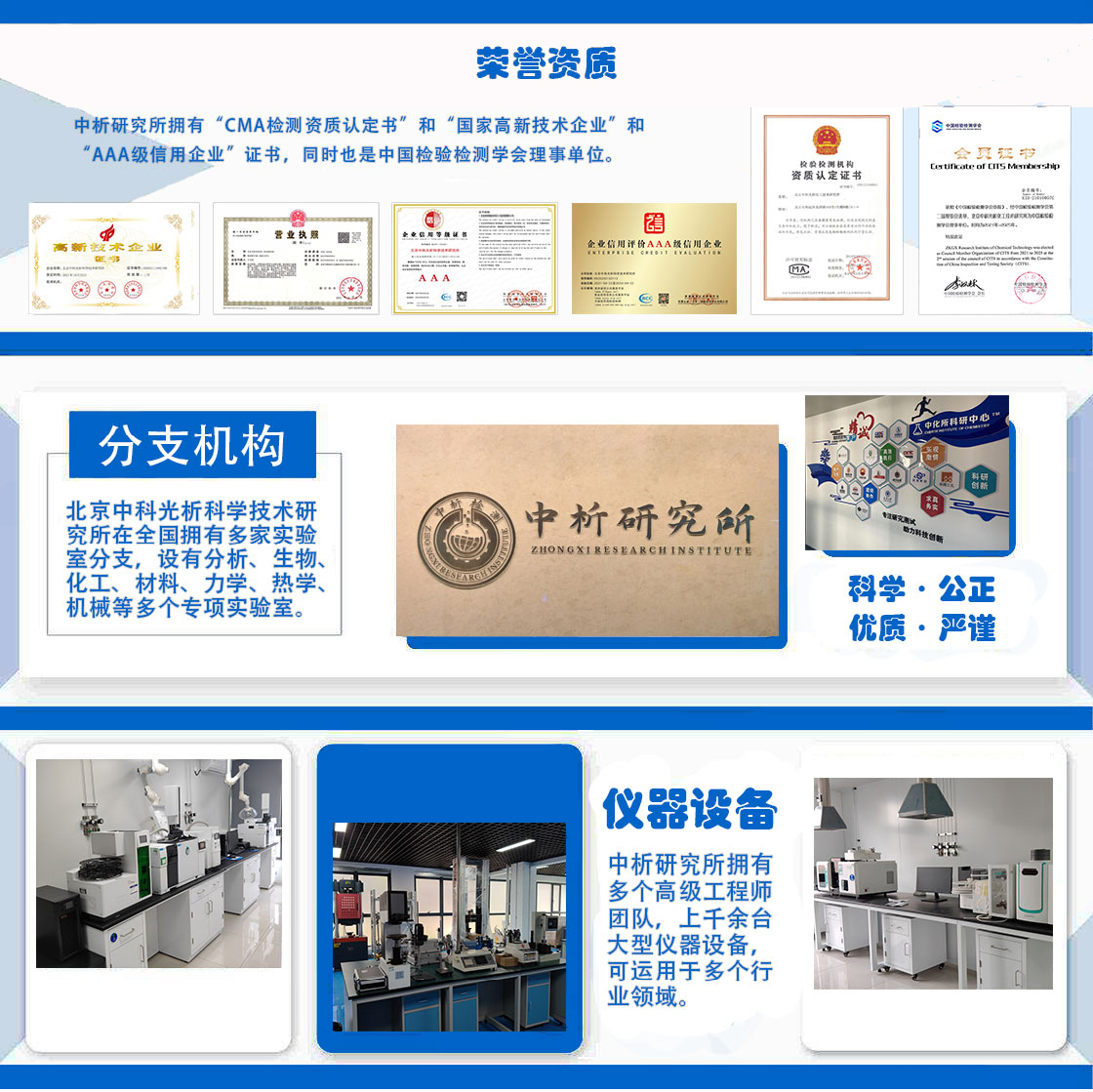
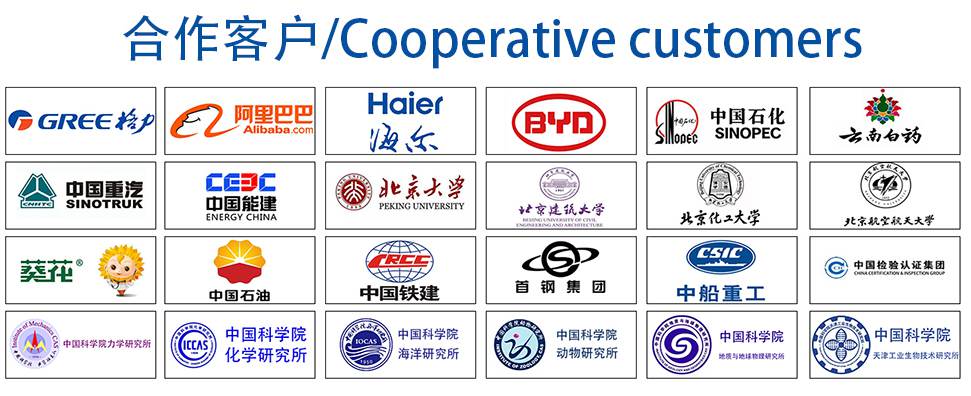
材料实验室
热门检测
262
220
198
207
200
205
215
208
215
220
207
204
207
208
200
198
213
202
211
206
推荐检测
联系电话
400-635-0567