高温外部短路检测:核心检测项目解析
一、检测目标与意义
- 电气系统的稳定性:是否能在短路瞬间触发保护机制(如熔断器、断路器等)。
- 热失控风险:短路产生的热量是否会导致材料分解、气体释放或热蔓延。
- 结构完整性:短路冲击是否导致机械形变、密封失效或部件熔融。
二、核心检测项目
1. 外观与结构检查
- 检测内容:
- 检查设备外壳、连接端子、导线绝缘层在高温下的老化、变形或破损情况。
- 确认短路路径是否因材料软化或结构松动导致意外导通。
- 标准参考: IEC 62619(工业储能电池)、GB/T 31485(电动汽车电池安全要求)。
2. 短路电流与温升测试
- 检测方法:
- 在高温环境(如60°C~85°C)下,人为制造外部短路(正负极直接连接),测量短路电流峰值、持续时间及温升速率。
- 使用红外热成像仪监测热点分布。
- 关键参数:
- 最大短路电流(I_max)、温升速率(ΔT/Δt)、最高表面温度(T_max)。
- 判定标准:温度是否符合UL 9540A(储能系统热失控评估)中的限值。
3. 绝缘性能评估
- 步骤:
- 短路测试后,立即测量设备内部绝缘电阻(如电池模组极间绝缘电阻)。
- 验证高温是否导致绝缘材料碳化或击穿。
- 设备要求: 使用高压绝缘测试仪(如500V DC或1000V DC档位)。
4. 保护装置响应验证
- 测试重点:
- 熔断器、断路器或BMS(电池管理系统)的响应时间是否在设定阈值内(如<5ms)。
- 保护动作后,是否有效切断电流回路,防止复通。
- 失效模式分析: 若保护装置未及时触发,需排查过流检测精度或高温下的器件性能漂移。
5. 气体排放与化学稳定性分析
- 适用场景: 针对锂离子电池等化学储能系统,检测短路时电解液分解产生的气体(如CO、H₂、CH₄)。
- 检测手段: 使用气相色谱仪(GC)分析气体成分,评估热失控风险等级。
6. 机械结构耐受性测试
- 内容:
- 短路冲击后检查壳体是否开裂、密封圈是否失效。
- 评估内部连接件(如汇流排、焊接点)的机械强度是否下降。
- 量化指标: 通过CT扫描或X射线检测内部结构损伤。
7. 多次循环短路测试
- 目的: 验证设备在多次轻微短路累积效应下的耐久性(如电网设备在雷击浪涌后的潜在损伤)。
- 方法: 在高温环境中重复施加短时(<1s)短路脉冲,记录性能衰减趋势。
三、测试设备与环境要求
- 高温试验箱:控温精度±2°C,支持快速升降温。
- 数据采集系统:同步记录电流、电压、温度信号(采样率≥1kHz)。
- 安全防护设施:防爆箱、废气排放系统、紧急断电装置。
四、风险控制与结果判定
- 合格标准:
- 无起火、爆炸、泄漏等不可逆故障。
- 保护装置及时动作,温升控制在安全阈值内。
- 风险等级划分: 根据测试结果划分风险等级(如低风险、需改进、高风险),指导设计优化。
五、应用案例
- 锂离子电池模组测试: 某型号储能电池在85°C下进行外部短路测试,BMS在2ms内触发断路,模组表面温度由60°C升至110°C后趋于稳定,判定为合格。
- 工业连接器失效分析: 高温导致绝缘层软化,短路电流引发连接器熔融,改进陶瓷绝缘材料后通过验证。
六、总结
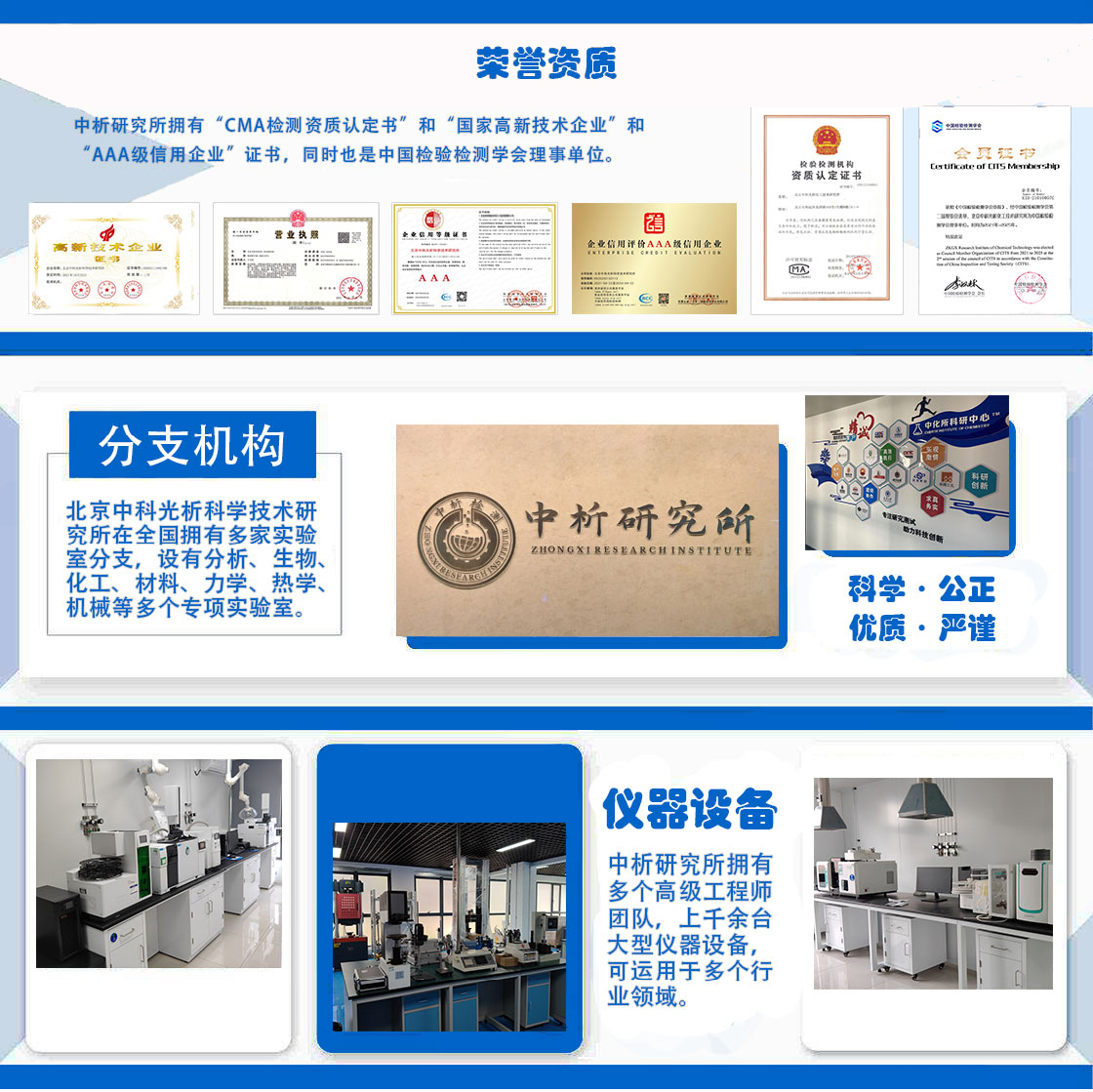
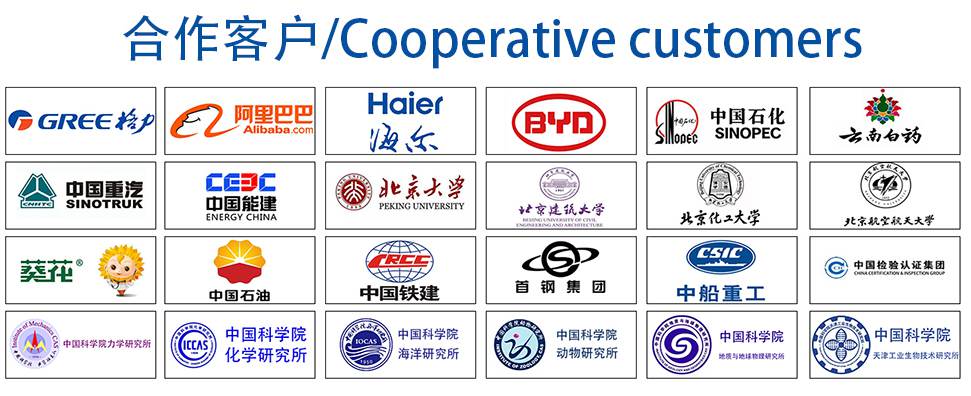
材料实验室
热门检测
254
214
189
203
196
204
209
201
207
215
203
199
197
202
195
193
207
198
207
201
推荐检测
联系电话
400-635-0567