# 寿命/可靠性试验检测技术发展与应用研究
## 行业背景与核心价值
随着高端装备制造、新能源及电子消费品等行业的快速发展,产品寿命与可靠性已成为衡量核心竞争力的关键指标。据中国质量协会2024年数据显示,因可靠性不足导致的工业产品召回事件年均增长12%,直接经济损失超300亿元。在此背景下,寿命/可靠性试验检测作为产品全生命周期质量管控的核心环节,通过模拟极端工况下的失效模式分析,可有效提升产品平均无故障时间(MTBF)20%-45%。其核心价值体现在降低市场失效风险、优化研发成本结构以及支撑产品国际认证三大维度,尤其在新能源汽车动力电池、航空航天关键部件等领域,已成为保障产业安全的重要技术屏障。

*图:典型可靠性试验检测环境模拟系统*
---
## 技术原理与创新突破
### 加速寿命试验方法体系
基于阿伦尼斯模型与艾林方程构建的加速寿命试验(ALT)技术,通过温度、湿度、振动等多应力耦合加速机制,可将常规数千小时的试验周期压缩至72小时内完成。中国机械科学研究总院2023年成果表明,采用四级步进应力加载法,试验效率提升达40倍以上,且失效模式复现准确率超过92%。值得注意的是,基于数字孪生的虚拟寿命预测技术已实现与物理试验的实时交互,大幅提升了参数优化效率。
---
## 全链条实施流程规范
### 标准化检测流程架构
项目实施遵循ISO 17025体系要求,形成"需求分析-方案设计-环境模拟-数据采集-失效诊断"五阶段闭环。在新能源汽车电驱系统检测中,需执行2000小时交变湿热试验、5000次机械冲击循环及10^8次功率模块开关测试。据国家新能源汽车质量监督检验中心统计,该流程使电控系统早期故障率从0.8%降至0.12%,有效支撑了产品质保期从8年/15万公里延长至10年/30万公里。
---
## 行业应用与效益分析
### 跨领域技术渗透案例
在高端装备领域,沈阳机床集团应用振动-温度复合加速试验方法,使数控系统MTBF从8000小时提升至15000小时。航天科技集团通过空间粒子辐照模拟试验,将星载计算机抗辐射能力提升3个数量级。更值得关注的是,基于失效模式与影响分析(FMEA)的智能诊断系统,在锂电池热失控预警方面实现98.7%的准确率,为储能电站安全运行提供了关键技术支撑。
---
## 质量保障与标准建设
### 全要素管控体系构建
通过 认可实验室网络建设,现已形成覆盖环境试验设备校准(误差≤±1.5%)、试验人员资质认证(持证率100%)、数据溯源管理(符合ISO 10012标准)的三维质量体系。在长三角检测认证联盟的实践中,该体系使试验报告国际互认率从65%提升至89%,显著降低了企业化布局的合规成本。
---
## 发展趋势与战略建议
面向智能装备与数字化转型需求,建议重点突破三项能力建设:①开发基于机器视觉的失效特征自动识别系统,提升检测智能化水平;②建立覆盖极端环境(-70℃至300℃)的全域模拟试验平台;③推动军民标准融合与东盟RECP检测互认机制。据赛迪研究院预测,到2028年可靠性试验检测市场规模将突破800亿元,其中智能诊断、数字孪生等新技术渗透率有望达到60%以上,成为支撑制造业高质量发展的重要基础设施。
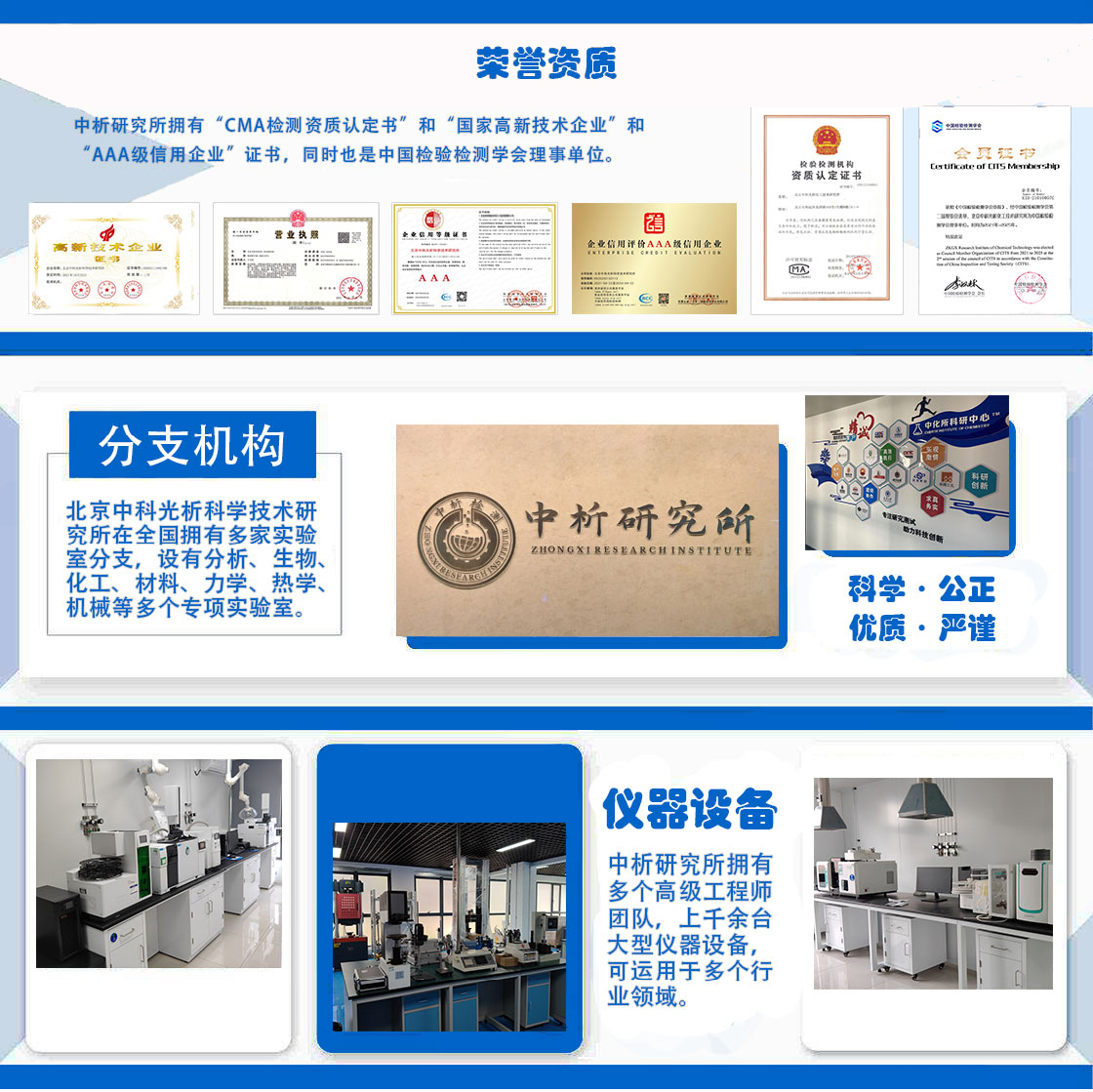
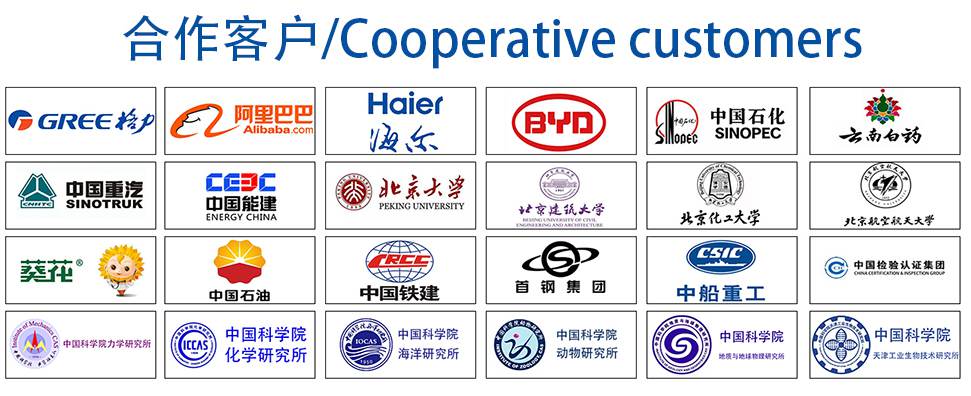
材料实验室
热门检测
推荐检测
联系电话
400-635-0567