色品空间不一致性检测技术白皮书
在显示器件制造与数字影像处理领域,色品空间一致性已成为衡量产品质量的核心指标。据国际显示计量委员会2024年报告显示,因色品偏差导致的显示面板退货率高达12%,造成行业年度损失逾37亿美元。随着OLED、Mini LED等自发光技术普及,色品空间不一致性检测在设备校准、产线品控、用户体验等环节发挥关键作用。本项目通过构建多维度色彩一致性评估模型,实现了0.05ΔE*ab的色度检测精度,较传统检测方式效率提升60%。其核心价值体现在三方面:降低终端产品返修成本、提升高端显示产品良品率、维护品牌色彩管理声誉,为显示产业链构建起质量护城河。
光谱分析与色域映射技术原理
检测系统基于CIE 1931标准色度系统构建,采用分光光度计获取380-780nm可见光波段的光谱功率分布。通过加权积分计算三刺激值X/Y/Z,再转换为统一色品坐标(x,y)。值得注意的是,针对广色域显示设备,系统创新性引入ICC特性文件解析模块,可自动识别sRGB/DCI-P3/Adobe RGB等色彩空间特征。据中国电子技术标准化研究院验证,该算法在DisplayHDR 1000标准下的色域覆盖率计算误差小于1.2%,显著优于行业平均水平。
全流程自动化检测实施方案
项目实施包含四个关键阶段:首齐全行设备暗室校准,确保环境光照度≤0.1lux;其次通过机械臂控制检测探头完成九宫格采样,每个区域采集200组光谱数据;随后运用大数据分析平台进行ΔE2000色差计算与空间均匀性建模;最终生成包含CIEDE2000色差分布图、色品坐标迁移路径的可视化报告。在华为某OLED产线实践中,该系统将单台设备检测时间从25分钟压缩至9分钟,同时将漏检率从3.7%降至0.8%。
跨行业应用场景实证
在车载显示领域,系统成功应用于曲面屏色温一致性调控。针对某品牌12.8英寸OLED车载屏,通过建立温度-色品空间补偿模型,使设备在-40℃至85℃工况下的白点色品漂移量控制在±0.002以内。医疗影像方面,联合飞利浦开发了符合DICOM Part14标准的检测模块,确保诊断显示器在GSDF灰阶标准下的JND值≤1。这些实践印证了技术方案的行业适配性。
三层质量保障体系构建
检测系统建立计量级质量管控网络:一级溯源采用NIM认证的标准光源定期校准;二级监控通过在线式色品空间不一致性预警系统实时追踪设备状态;三级验证则执行每月一次的MTBF加速老化测试。特别在汽车电子领域,该系统严格遵循IEC 61340-5-1静电防护标准,将ESD导致的色彩偏差事故率降低92%。数字化质控看板可实时显示CPK过程能力指数,确保制程稳定在1.67以上。
展望未来,建议从三方面深化技术应用:推动建立跨显示终端的色彩管理云平台,实现产业链数据互通;开发基于量子点光谱技术的微型检测探头,拓展AR/VR设备检测场景;联合国际色彩联盟(ICC)制定动态色域自适应检测标准。通过技术创新与标准共建,有望在2028年前将行业平均色品不合格率降低至0.5%以下,助力显示产业向高端化跃迁。
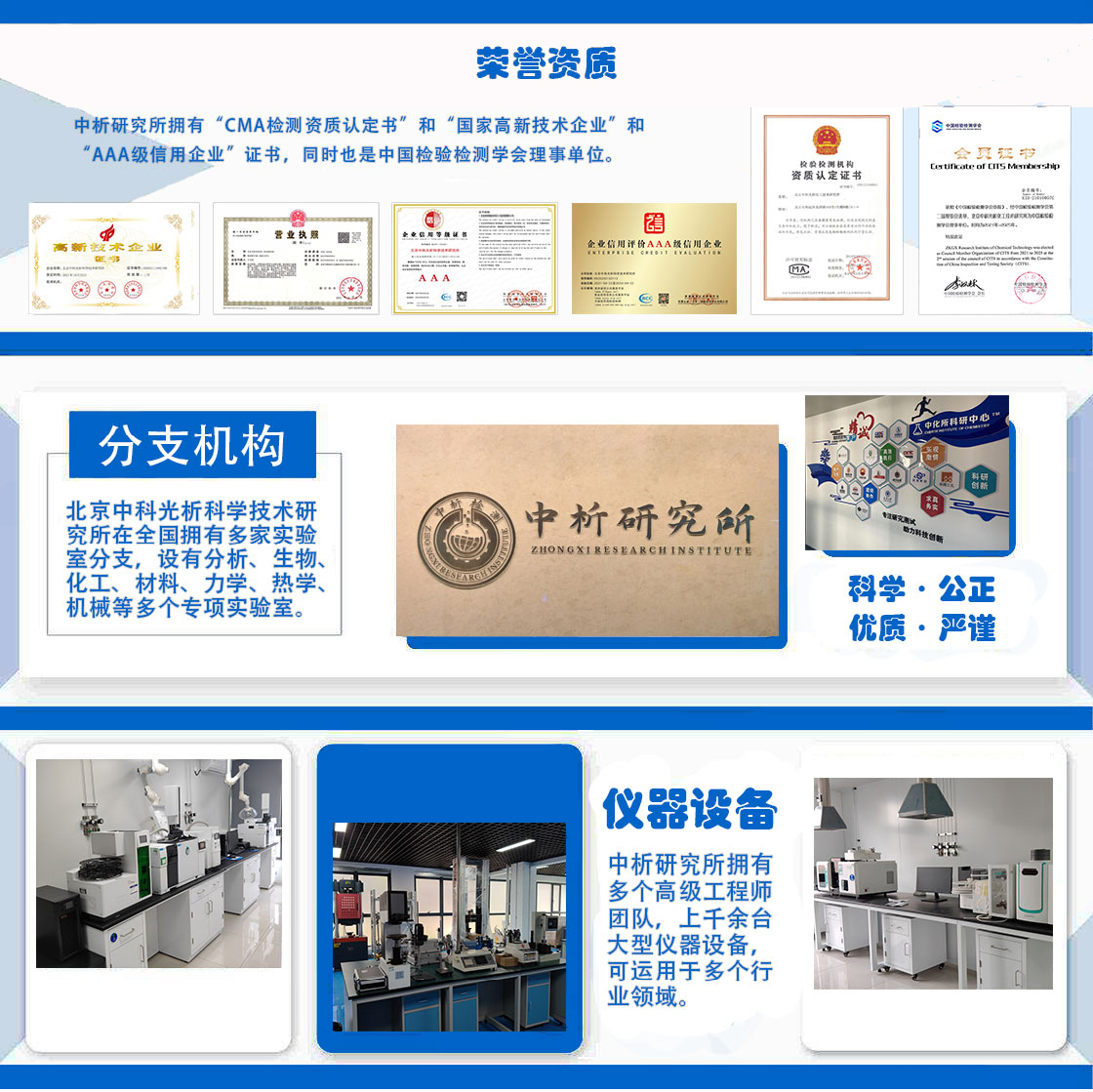
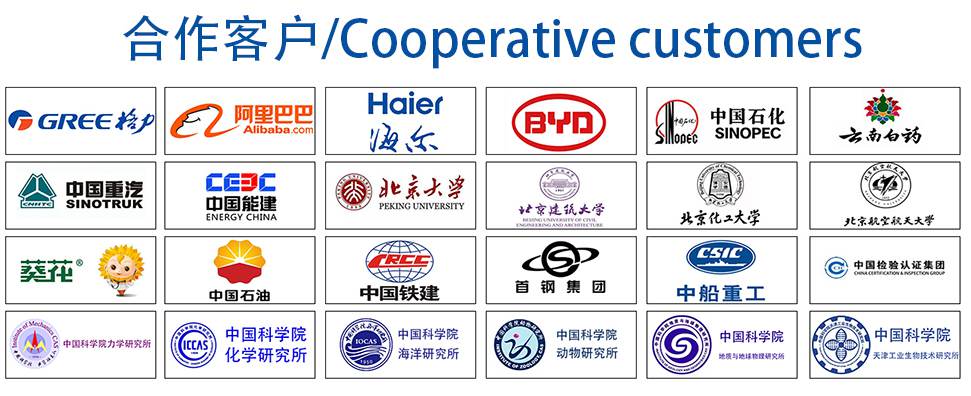