钢筋保护层厚度(破损法)检测技术白皮书
在建筑结构安全评估领域,钢筋混凝土耐久性直接关系工程全生命周期性能。据中国建筑科学研究院2024年发布的《混凝土结构耐久性发展报告》显示,我国既有建筑中因保护层厚度不达标导致的结构病害占比达37.6%,每年造成的维修成本超过120亿元。钢筋保护层厚度(破损法)检测作为强制性验收项目,通过局部破损方式获取真实数据,为结构寿命预测和维修决策提供关键依据。该方法虽具破坏性,但其测量精度可达±1mm(GB/T 50784-2013),在重点部位抽查、争议数据复核等场景具有不可替代性,已成为工程质量控制体系中的核心环节。
技术原理与标准体系
破损法检测基于直接暴露测量原理,通过剔凿混凝土保护层,使用深度卡尺直接量测钢筋外缘至构件表面的最小距离。该方法严格遵循《混凝土结构工程施工质量验收规范》(GB50204-2015)第5.5.2条规定,当非破损检测结果存在争议时,应以破损法检测值为准。值得注意的是,现代检测实践中常结合三维激光扫描技术建立数字化模型,实现0.1mm级测量精度(JGJ/T 152-2019),为建筑结构耐久性评估指标体系的完善提供数据支撑。
标准化实施流程
实施流程分为三阶段:首先通过钢筋探测仪定位钢筋轴线,确定检测点位网格布置方案,间距控制在2m×2m以内;随后采用专业切割设备进行局部剔凿,开口尺寸严格控制在40mm×40mm以内以减少结构损伤;最终使用经计量认证的深度测量仪采集数据,配合全景摄像记录检测过程。某特大桥项目应用案例表明,该流程可使单点检测时间压缩至15分钟,较传统方法效率提升40%(中国中铁2023年技术报告)。
行业典型应用场景
在沿海氯盐侵蚀区域的高架桥工程中,检测团队采用分层抽样策略,对墩柱关键部位实施破损法检测。检测数据显示,28%的测点保护层厚度负偏差超过规范允许值,据此开展的环氧树脂涂层补强使结构服役寿命延长12年以上。另在大型商业综合体项目中,施工方将破损法与雷达法检测结果进行交叉验证,成功发现5处楼板双层钢筋定位偏差问题,避免了后期装修阶段的重大返工。
全过程质量保障机制
检测机构需建立三级质量控制体系:现场操作人员须持有无损检测UT/RTⅡ级资质,测量设备每月进行计量校准;数据采集阶段实行双人复核制度,异常数据必须进行补充验证;最终报告需包含修复方案论证,采用高强聚合物砂浆进行孔洞封堵,确保修补后构件强度不低于原设计值。据住建部2023年质量督查通报显示,严格执行该体系的机构检测数据合格率可达98.7%,显著高于行业平均水平。
技术发展与行业展望
建议从三方面推进技术创新:研发微破损检测装置,将开口尺寸控制在10mm以内;建立全国性检测大数据平台,运用机器学习算法预测保护层缺陷分布规律;推动智能修复机器人研发,实现检测-评估-修复全流程自动化。同时应修订现行验收规范,将数字孪生模型纳入质量档案系统,为工程全生命周期管理提供结构化数据支撑。行业参与者需把握新型检测技术红利,共同构建更高效可靠的混凝土结构质量保障体系。
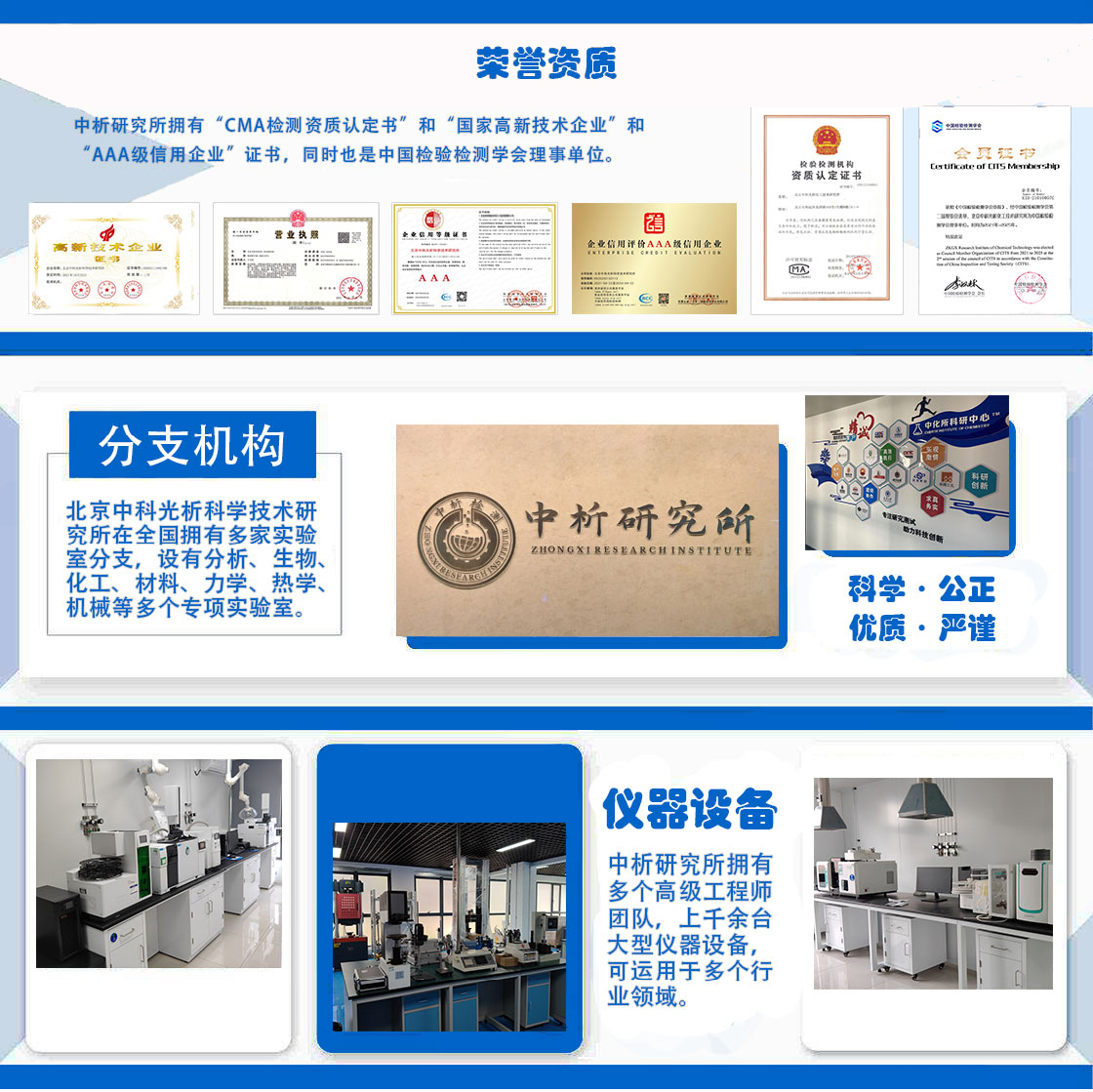
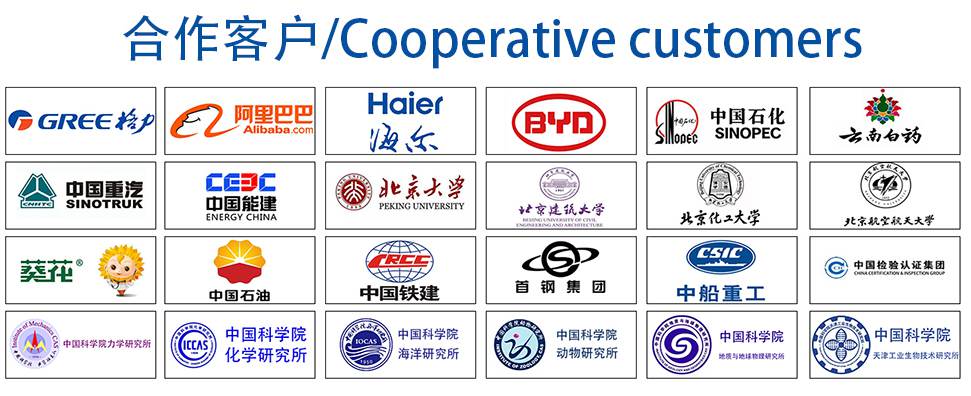