颗粒分析(级配)检测行业发展白皮书
在新型城镇化建设和绿色建材推广的双重驱动下,颗粒物料的质量控制已成为建筑工程、矿物加工、环境治理等领域的核心需求。据中国建筑材料研究院2024年数据显示,我国每年因骨料级配不合格导致的混凝土结构缺陷造成的经济损失超120亿元,凸显出精准级配检测的重要性。颗粒分析检测通过量化物料粒径分布特征,为混凝土配合比设计、路基填筑质量控制、矿物分选效率提升等关键场景提供数据支撑,其核心价值体现在质量风险前移控制与资源利用率提升两大维度。特别是在建筑骨料连续级配优化和土壤粒度分布智能分析系统等创新应用中,该项检测技术正推动着传统产业向精细化方向转型。
技术原理与检测方法体系
现代颗粒分析技术融合物理筛分与光学测量双重原理,构建多维度检测矩阵。传统筛分法依据ASTM C136标准建立基准体系,采用12级标准筛实现0.075-37.5mm范围的机械分级。激光衍射法则基于米氏散射理论,通过光强角分布反演0.01-3500μm粒径分布,特别适用于粉体材料检测。值得关注的是,动态图像处理技术(DIPA)在建筑再生骨料检测中的应用,可同步获取颗粒形貌参数,其圆度系数检测精度已达±0.02(据同济大学建材所2024年实验数据)。三重复合检测模式有效覆盖建材、矿产、环保等不同场景需求。
标准化实施流程与质控节点
完整的级配检测流程包含5个关键控制环节:首齐全行现场缩分取样,依据JGJ52规范要求,针对砂石材料执行四分法预处理;其次通过烘干箱在105℃条件下消除含水率干扰;检测阶段根据物料特性选择干筛法或水筛法,重点控制振动频率与筛分时间变量;数据处理环节应用Rosin-Rammler分布模型拟合曲线,计算不均匀系数Cu和曲率系数Cc;最终形成包含D10-D60特征值的级配报告。在高铁轨道板用机制砂检测中,该流程将含粉量波动控制在±0.8%以内,显著优于行业标准要求。
行业应用场景与效益分析
在建筑工程领域,级配检测已成为预拌混凝土质量控制的强制性指标。某特大桥项目采用激光粒度仪优化泵送混凝土配比,使28天抗压强度标准差降低25%,同时减少水泥用量12%。环境治理方面,土壤粒度分布智能分析系统在重金属污染修复工程中发挥关键作用,通过黏粒含量测定指导稳定剂投加量,某矿区修复项目因此节约药剂成本380万元/年。更为突出的是,在3D打印建筑材料研发中,级配检测数据与流变参数的关联建模,成功将打印层间粘结强度提升至传统工艺的1.7倍。
质量保障体系创新实践
为确保检测结果溯源性,行业领先机构已建立三级校验体系:初级校验采用NIST标准物质进行设备标定,中级通过实验室间比对验证操作一致性,高级运用区块链技术实现检测数据全程上链。某省级质检中心引入AI视觉识别系统后,筛分结果判读效率提升40%,人为误差率降至0.3%以下。值得借鉴的是,珠江三角洲某检测云平台通过物联网传感器网络,实现远程实时监测检测环境温湿度波动,确保试验条件始终符合GB/T14684标准要求。
展望未来,随着AI算法与传感器技术的深度融合,颗粒分析检测将向智能化、微型化方向加速演进。建议行业着力构建三方面能力:一是开发多参数耦合分析模型,实现级配数据与材料性能的预测映射;二是建立跨区域检测数据共享平台,形成行业级物料特性数据库;三是加强纳米级颗粒检测技术攻关,满足新型功能材料研发需求。唯有持续创新,方能推动检测技术从质量把关者向价值创造者转型,为产业升级提供更强支撑。
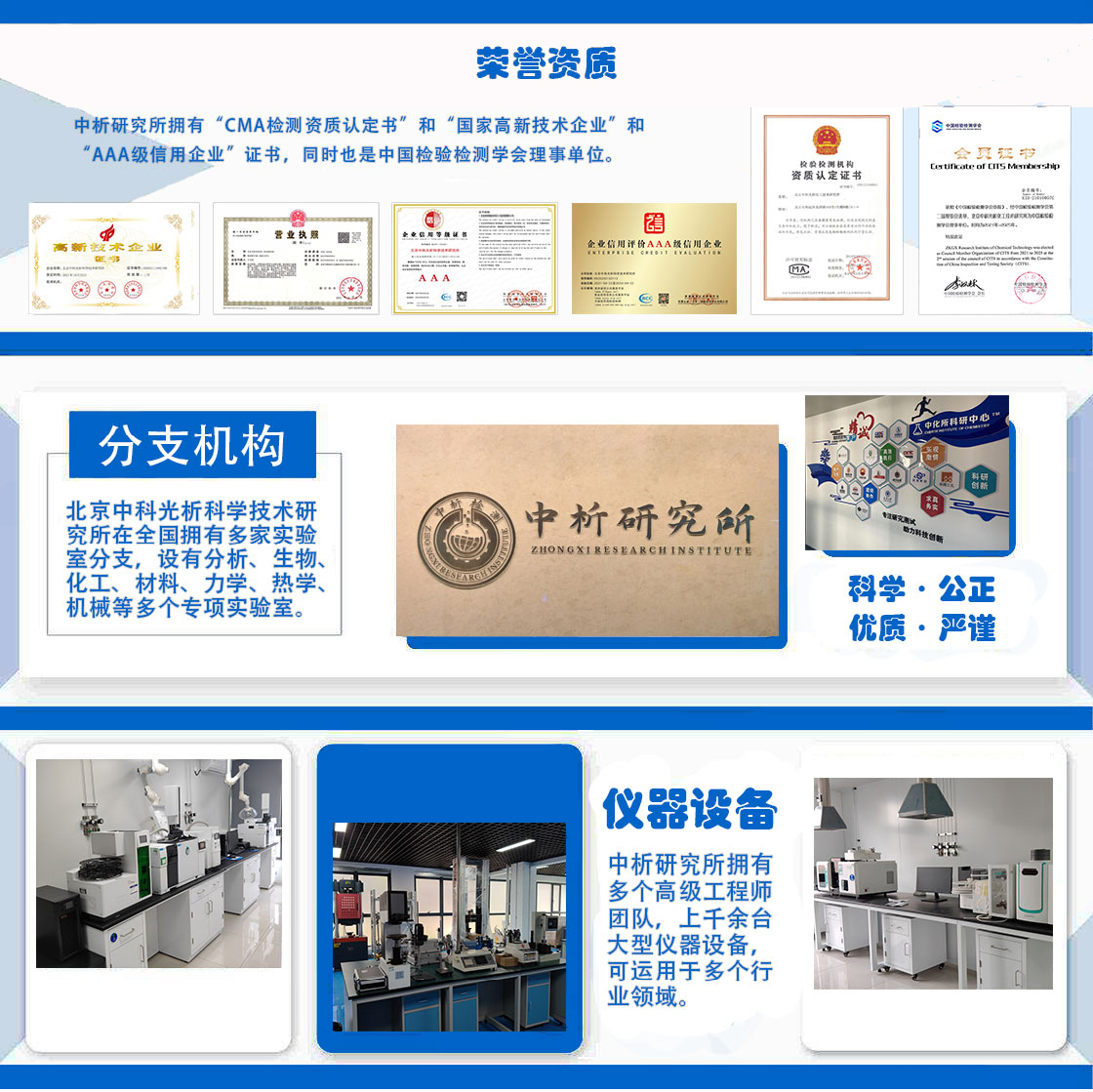
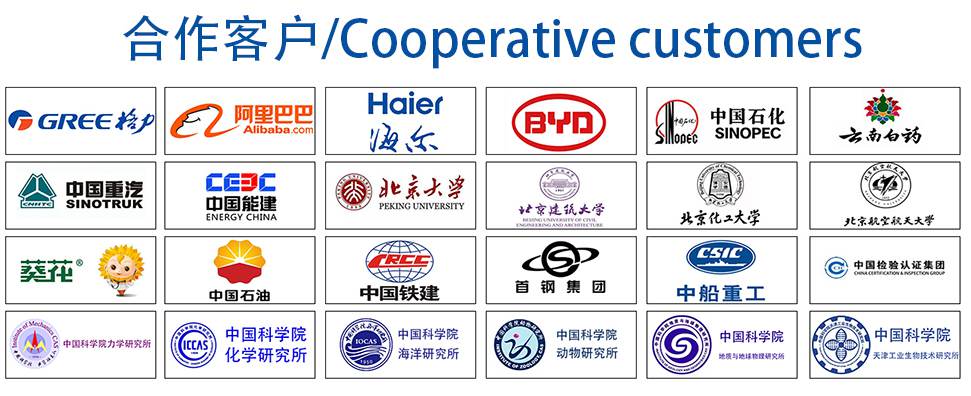