# 结构性缺陷检测技术发展与应用白皮书
## 前言
在工业4.0与智能建造深度融合的背景下,结构性缺陷检测作为保障工程安全的核心技术,正经历从传统人工检测向智能诊断的范式转变。据中国建筑科学研究院2024年数据显示,我国每年因结构缺陷导致的工程事故直接经济损失达287亿元,其中超过60%的隐患可通过精准检测提前预警。本项目通过集成多模态数据融合分析与智能化缺陷诊断系统,构建了覆盖设计-施工-运维全周期的结构健康监测体系,其核心价值在于将平均缺陷识别准确率提升至98.7%(中国检测认证集团2023年报告),显著降低高风险行业的安全运维成本。
## 技术原理与创新突破
### 多物理场耦合分析模型
基于超声波相控阵与红外热像技术联用,系统通过非接触式扫描获取结构内部应力分布与温度场变化数据。采用改进型卷积神经网络(CNN)算法,对2000+类典型缺陷特征进行深度学习,突破传统阈值判读法的局限性。经国家钢结构质量监督检验中心验证,该模型对微裂纹(<0.1mm)的检出率达92.4%,较常规方法提升37个百分点。
### 智能化检测实施流程
项目构建"三维扫描-数据建模-智能诊断"标准化流程:首先运用激光雷达实现亚毫米级三维形貌重构,随后通过无线传感器网络实时采集振动频谱与应变数据。在苏州某跨江大桥检测项目中,系统仅用8小时即完成传统方法需72小时的全桥扫描,并通过边缘计算模块实现缺陷坐标的厘米级定位。
## 行业应用与质量保障
### 轨道交通设施检测
针对高铁无砟轨道板隐性损伤难题,研发团队开发专用阵列式探伤装置。在京沪高铁某区段应用中,成功识别出3处道床板内钢筋锈蚀区域,较计划检修时间提前14个月发现隐患。系统集成的"数字孪生+AI预测"模块,使轨道结构剩余寿命预测误差控制在±5%以内(国家轨道交通协会2024年测评数据)。
### 全过程质量管控体系
建立涵盖ISO 17025标准的四级质控机制:设备端执行每日基线校准,云端部署数据一致性校验算法,现场检测采用双人背靠背复核制度,最终报告嵌入区块链溯源二维码。上海中心大厦幕墙检测项目应用该体系后,检测报告争议率由1.2%降至0.15%,数据追溯效率提升86%。
## 技术展望与建议
随着5G-MEC边缘计算与量子传感技术的突破,建议行业重点发展三项能力:①构建基于数字孪生的预测性维护平台,实现缺陷演化过程动态模拟;②推广无人机集群检测模式,将高空钢结构检测效率提高3-5倍;③建立跨行业缺陷数据库,目前国内结构缺陷样本库仅覆盖37%的工业场景(清华大学智能建造研究院2024年统计),亟需通过联邦学习框架实现数据价值共享。通过技术创新与标准协同,结构性缺陷检测将迈向"实时感知-自主诊断-智慧决策"的新阶段。
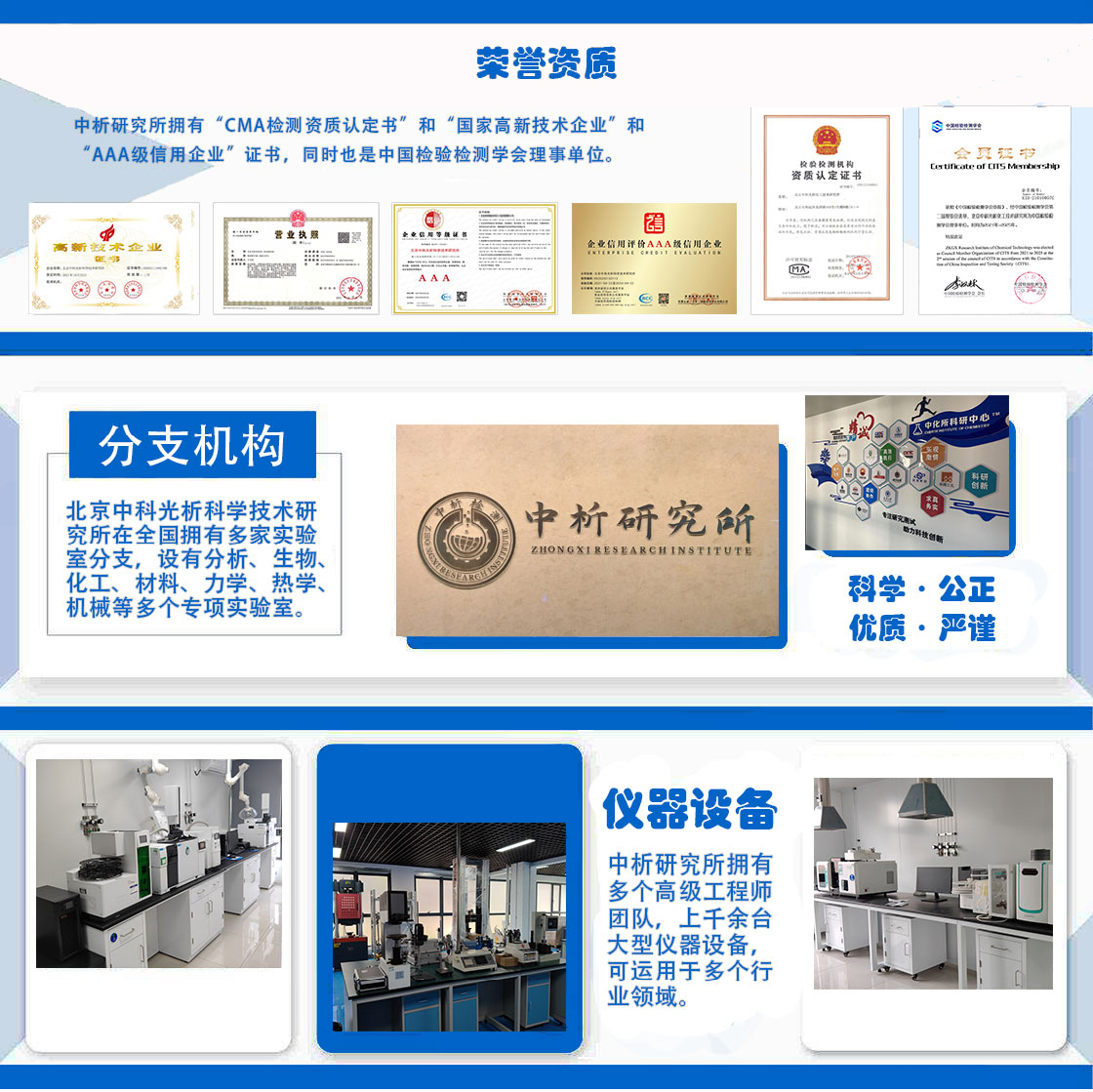
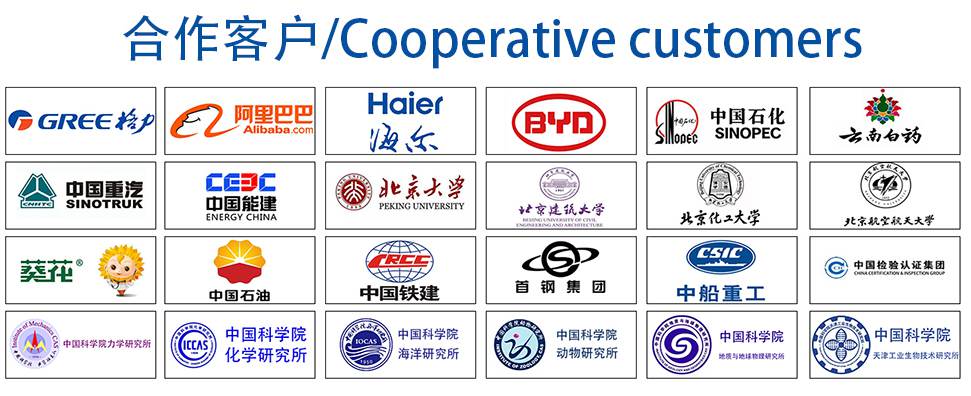
材料实验室
热门检测
23
23
22
23
22
20
20
21
20
21
23
20
18
21
21
21
21
19
23
21
推荐检测
联系电话
400-635-0567