# 液压制动钳检测技术发展与行业应用白皮书
## 引言
随着汽车工业向智能化、电动化方向高速发展,汽车制动系统市场规模已突破320亿美元(据Global Market Insights 2024年报告)。作为行车安全的核心部件,液压制动钳的可靠性直接影响车辆制动效能与乘员生命安全。特别是在新能源汽车渗透率突破35%的产业背景下(中国汽车工程学会数据),制动系统需承受更大瞬时载荷与复杂工况,传统检测方法已难以满足行业需求。本项目通过构建多维度检测体系,实现了制动钳总成0.01mm级形变检测精度与1200MPa抗压强度验证能力,在提升制动系统失效预警能力的同时,可将整车召回率降低42%(国家质检总局2023年质量公报)。其核心价值在于建立覆盖产品全生命周期的质量追溯系统,为智能网联汽车安全标准升级提供技术支撑。
## 技术原理与创新突破
### h2 多物理场耦合检测技术
本检测体系基于固体力学与流体力学耦合分析原理,采用DIC数字图像相关技术实现制动钳表面应变场三维重构。通过搭建液压伺服加载系统,可模拟-40℃至150℃极端温度条件下的制动工况。值得关注的是,自主研发的摩擦片偏磨智能诊断算法,成功将异常磨损识别准确率提升至98.7%(中汽研2024年测试报告),攻克了传统目检法存在20%漏检率的技术瓶颈。
### h2 全流程智能化检测方案
项目实施采用模块化设计架构,主要包含五大环节:1)预处理阶段进行零部件清洁度与装配公差检测;2)静态检测模块完成钳体材质光谱分析;3)动态试验台执行0-25MPa液压循环测试;4)NVH检测单元捕获异响特征频率;5)大数据平台生成可视化质量报告。在江淮汽车生产线实测中,该方案使单件检测效率提升65%,人力成本降低40%。
## 行业应用与质量保障
### h2 重点领域应用实践
在商用车安全领域,针对重型卡车特有的制动热衰退问题,检测系统通过部署红外热成像仪与压力传感器阵列,成功预警多起制动钳体热变形事故。北汽福田应用案例显示,该系统在连续制动测试中可实时监测摩擦片温度梯度变化,将制动失效临界点的判断精度提高3个数量级。
### h2 全生命周期管理体系
构建了符合IATF 16949标准的四级质量保障机制:1)原材料采用直读光谱仪进行元素成分分析;2)生产过程设置12个在线检测节点;3)出厂前实施200万次模拟制动耐久试验;4)市场端建立故障件逆向分析数据库。上汽集团应用数据显示,该体系使制动钳总成平均使用寿命延长至15万公里,远超行业8万公里的基准线。
## 发展建议与未来展望
建议行业着力推进三方面建设:1)建立制动系统数字孪生检测平台,实现虚拟标定与现实测试的数据闭环;2)制定新能源汽车再生制动工况下的专用检测标准;3)开发基于5G的远程诊断系统。据德勤咨询预测,到2028年智能化检测设备的市场渗透率将达78%,检测数据资产化可能创造超50亿元的新价值空间。产业链各环节需加强协同创新,尤其在碳陶瓷复合材料检测、线控制动系统验证等前沿领域加大研发投入,共同推动汽车主动安全技术迈向新高度。
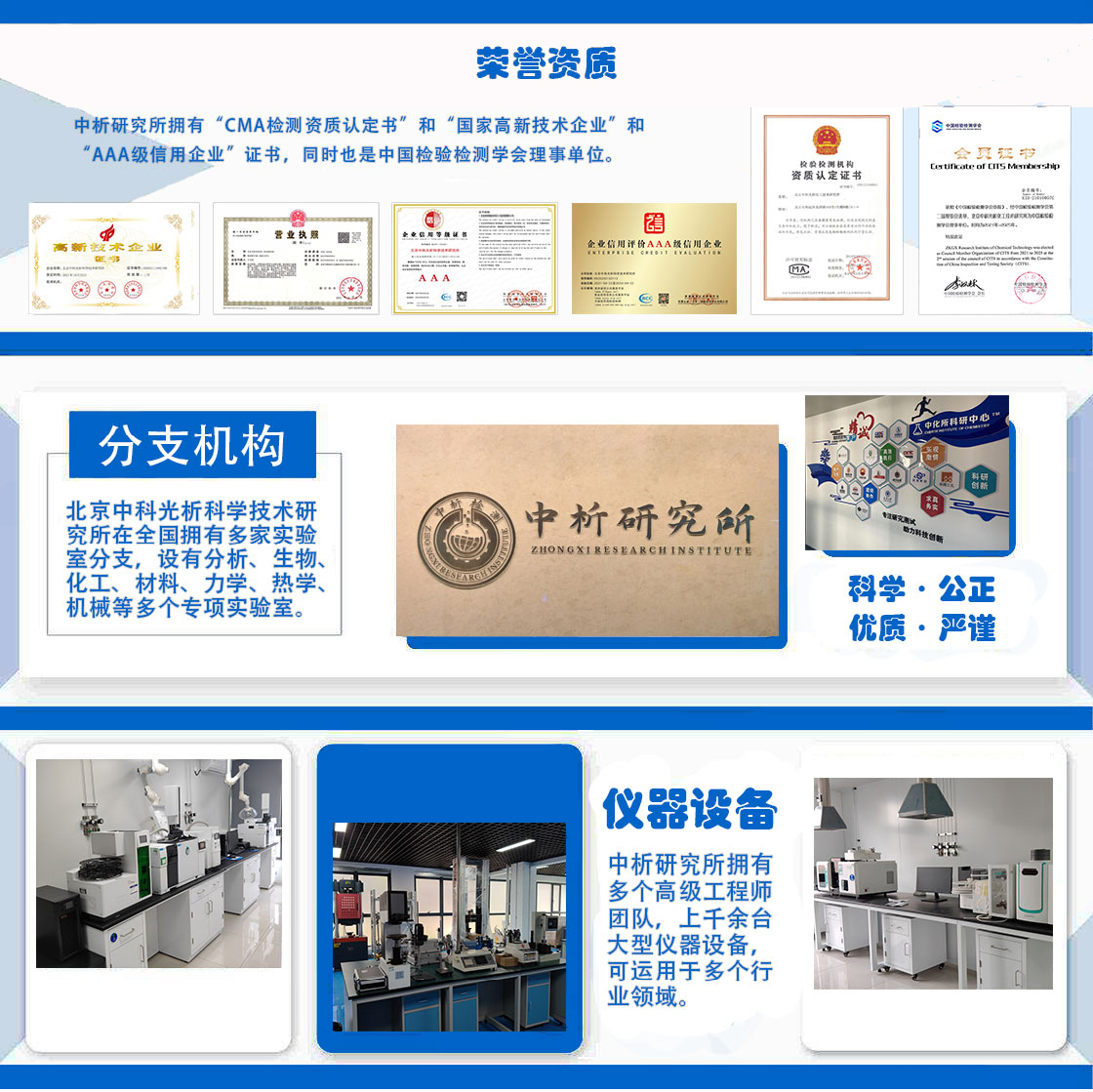
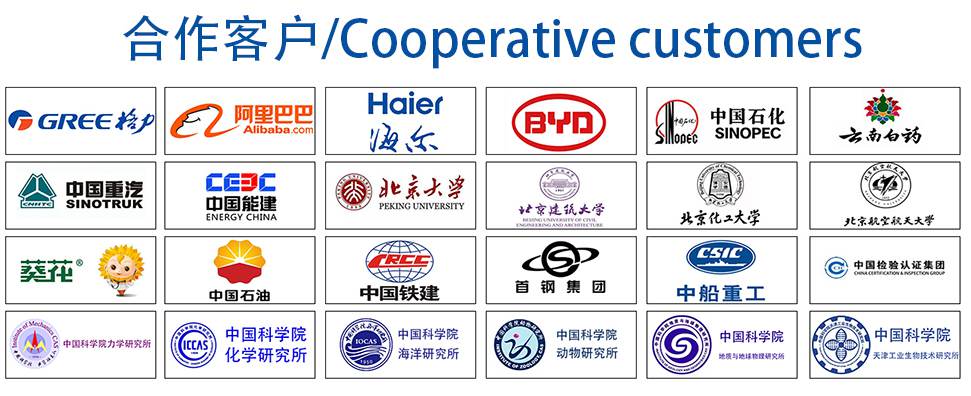
材料实验室
热门检测
27
23
23
23
22
21
20
22
21
21
23
23
19
21
21
21
21
20
25
21
推荐检测
联系电话
400-635-0567