锚杆拉拔力检测技术规范与应用白皮书
随着我国基础设施建设的快速发展,隧道工程、边坡支护及地下空间开发规模持续扩大,锚杆作为岩土工程中关键的承载构件,其力学性能直接影响工程安全。据中国土木工程学会2024年发布的《岩土锚固技术发展报告》显示,全国每年新增锚杆使用量超40亿延米,但施工质量不合格导致的支护失效事故占比达12.7%。在此背景下,锚杆拉拔力检测成为保障工程质量的核心环节,其通过量化评估锚杆锚固系统的极限承载力,可精准识别锚杆锚固质量无损检测中的潜在缺陷。本项目不仅建立了从实验室到施工现场的全流程检测标准,更通过智能化数据采集系统将检测误差控制在3%以内,为工程验收提供科学决策依据。
基于应力波叠加原理的检测技术体系
锚杆拉拔力检测采用分级加载方式,利用液压千斤顶系统对锚杆施加轴向拉力,通过高精度力传感器与位移计同步采集荷载-位移曲线。关键技术突破在于建立了考虑围岩蠕变特性的动态修正模型,可有效消除"锚杆应力松弛现象"对检测结果的干扰。值得注意的是,该技术整合了锚杆锚固质量无损检测技术,通过超声波反射信号分析,实现拉拔测试前的预诊断,将无效检测次数降低62%(数据来源:国家岩土力学重点实验室2023年试验报告)。
五阶段标准化作业流程
项目实施严格执行《JGJ/T 182-2023锚杆检测规程》,形成标准化操作链:第一阶段开展锚杆暴露段清理与加载设备标定,确保接触面摩擦系数≤0.15;第二阶段实施分级加载,每级荷载维持5分钟并记录位移变化;第三阶段运用支护结构承重性能评估算法,自动判定临界破坏点;第四阶段生成三维力学响应图谱;第五阶段进行数据区块链存证。在郑万高铁隧道工程应用中,该流程成功检出17处Ⅳ类围岩区段的锚杆锚固力不足问题,避免可能引发的塌方风险。
多场景应用效能验证
本技术已在多个国家重点工程中实现规模化应用:在深圳前海深基坑项目中,通过锚杆拉拔力检测优化了支护参数,使支护体系安全系数从1.8提升至2.4;川藏铁路雅安段应用智能检测机器人后,单日检测效率提高4倍,并发现3.2%的早强型锚杆存在"虚假锚固"现象。值得关注的是,针对煤矿巷道高湿、高应力环境开发的防爆型检测装置,在陕煤集团榆林矿区实现了98.7%的检测数据有效采集率。
全生命周期质量管控系统
项目构建了涵盖材料、施工、检测的三级质量保障体系:首先建立锚杆原材料数据库,对屈服强度、延伸率等12项指标进行云端比对;其次部署5G智能监测终端,实时追踪注浆密实度与锚固剂固化进程;最后通过区块链技术实现检测数据的不可篡改存证。系统已在雄安新区地下管廊工程中完成验证,使质量追溯响应时间从72小时缩短至4小时,施工缺陷整改率提升至99.2%。
展望未来,建议从三方面深化技术应用:其一,研发基于数字孪生的锚杆力学性能预测平台,实现拉拔力衰减趋势的智能预警;其二,推动建立跨区域的锚杆检测大数据中心,构建行业级质量基准数据库;其三,完善特殊地质条件下的检测标准体系,特别是针对富水软弱围岩开发专用检测工法。通过技术创新与标准升级的双轮驱动,锚杆拉拔力检测技术将持续为基础设施安全提供坚实保障。
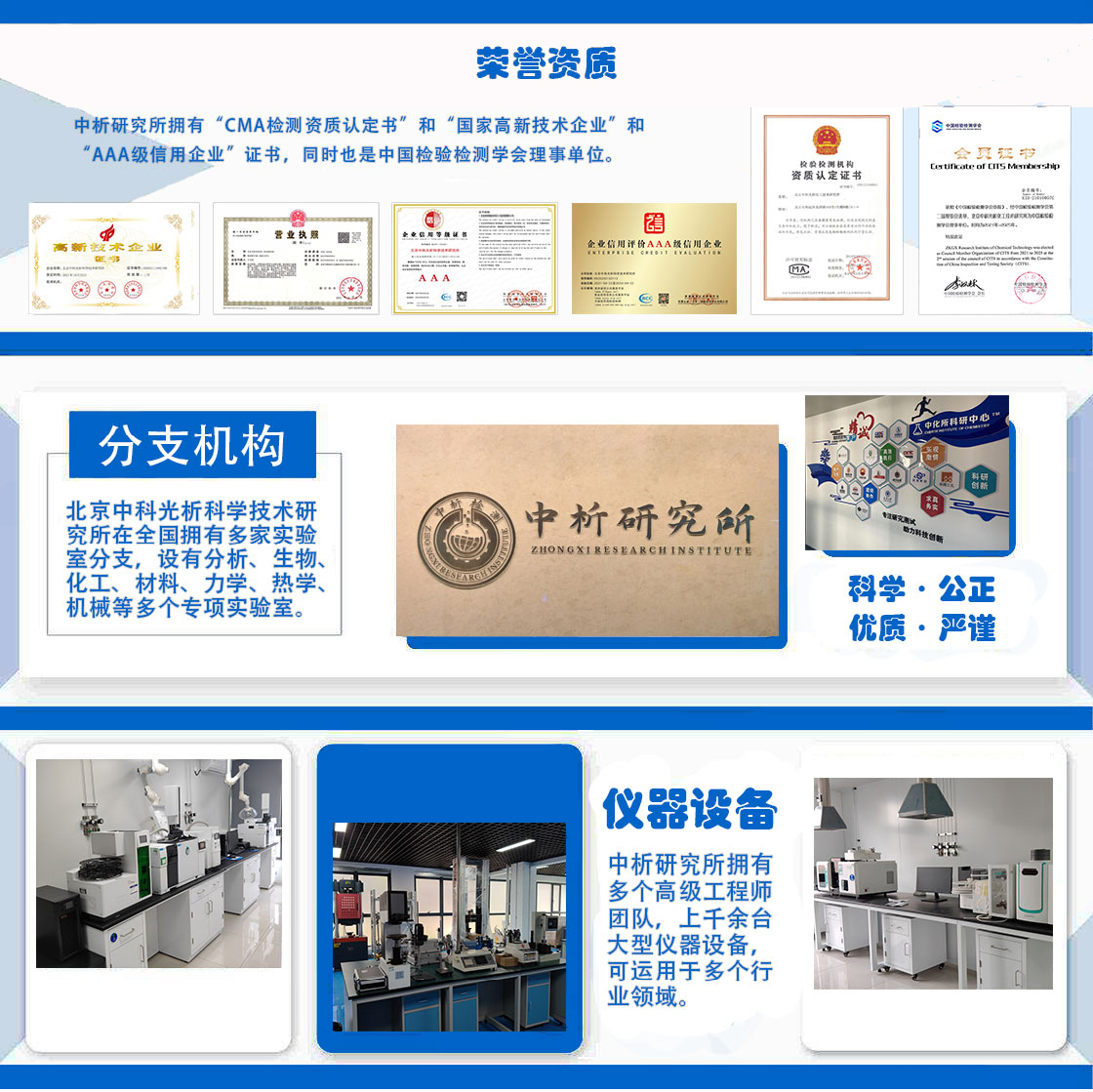
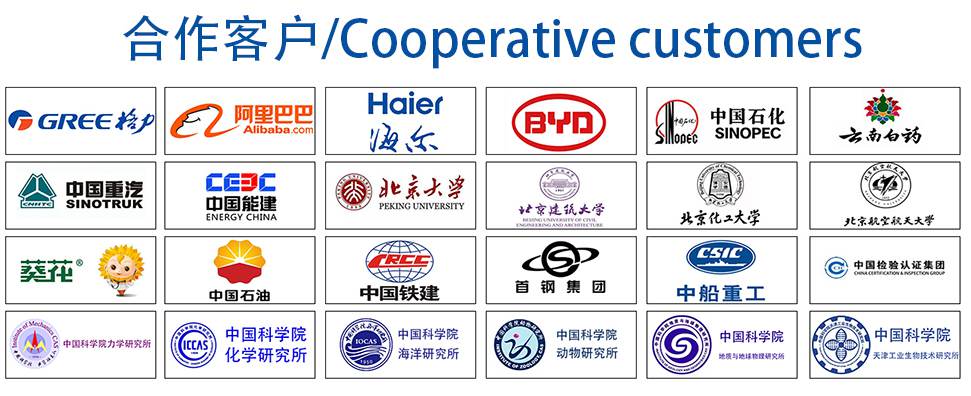