基于相平衡理论和扩散动力学模型,现代溶解性检测采用动态光散射(DLS)与紫外分光光度法联用技术,实现溶液体系中溶解态与悬浮态的精准区分。以美国药典USP42-NF37标准为基准,不溶度指数(II)的计算公式为II=(C0-Cs)/C0×100%,其中C0为初始浓度,Cs为平衡溶解度。值得注意的是,新型微流控芯片技术可将检测灵敏度提升至0.1μg/mL水平,据中国科学院过程工程研究所2024年实验数据显示,该技术对多晶型药物的鉴别准确率提高至98.7%。
## 标准化实施流程构建完整检测流程涵盖三个关键阶段:预处理阶段需通过粒径控制(粒径≤50μm)和温度梯度法消除物理形态干扰;测量阶段采用自动化溶出度仪配合在线粒子计数器,实现溶解过程的动态监测;数据分析阶段引入机器学习算法,可自动识别异常溶解曲线。在乳制品加工领域的具体应用中,针对酪蛋白胶束的溶解度检测需严格保持pH6.5-6.7区间,温度波动需控制在±0.2℃范围内以保证数据可靠性。
## 行业应用场景解析在创新药物研发领域,某跨国药企通过建立辅料不溶度指数数据库,将制剂开发周期缩短40%。其案例显示,羟丙甲纤维素(HPMC)的不溶度指数从12.3%优化至5.1%后,片剂溶出度一致性由83%提升至97%。而在光伏材料行业,多晶硅浆料的溶解度检测数据直接关系电池转换效率,采用在线近红外监测技术后,某龙头企业将浆料固含量偏差从±1.5%降至±0.3%,组件功率输出提升1.2W。
## 质量保障体系创新构建四级质量管控体系:仪器端执行ASTM E2655标准进行日校;操作端实施视觉识别防错系统,避免人为操作偏差;数据端采用区块链技术确保检测记录不可篡改;验证端引入第三方能力验证(PT)方案。德国TÜV认证数据显示,该体系使实验室间比对数据离散系数从7.8%降至2.1%,显著优于ISO/IEC 17025:2017要求。
## 技术发展前瞻建议建议行业重点关注三个发展方向:其一,开发基于人工嗅觉的溶剂残留检测联用系统,突破现有检测维度局限;其二,建立涵盖5000种化合物的溶解度预测AI模型,实现检测前端的智能预判;其三,推动ISO/TC34制定纳米材料溶解度的国际标准。随着绿色化学理念的深化,未来检测体系需深度融合可持续性评估指标,形成涵盖性能、安全、环境的三维评价范式。
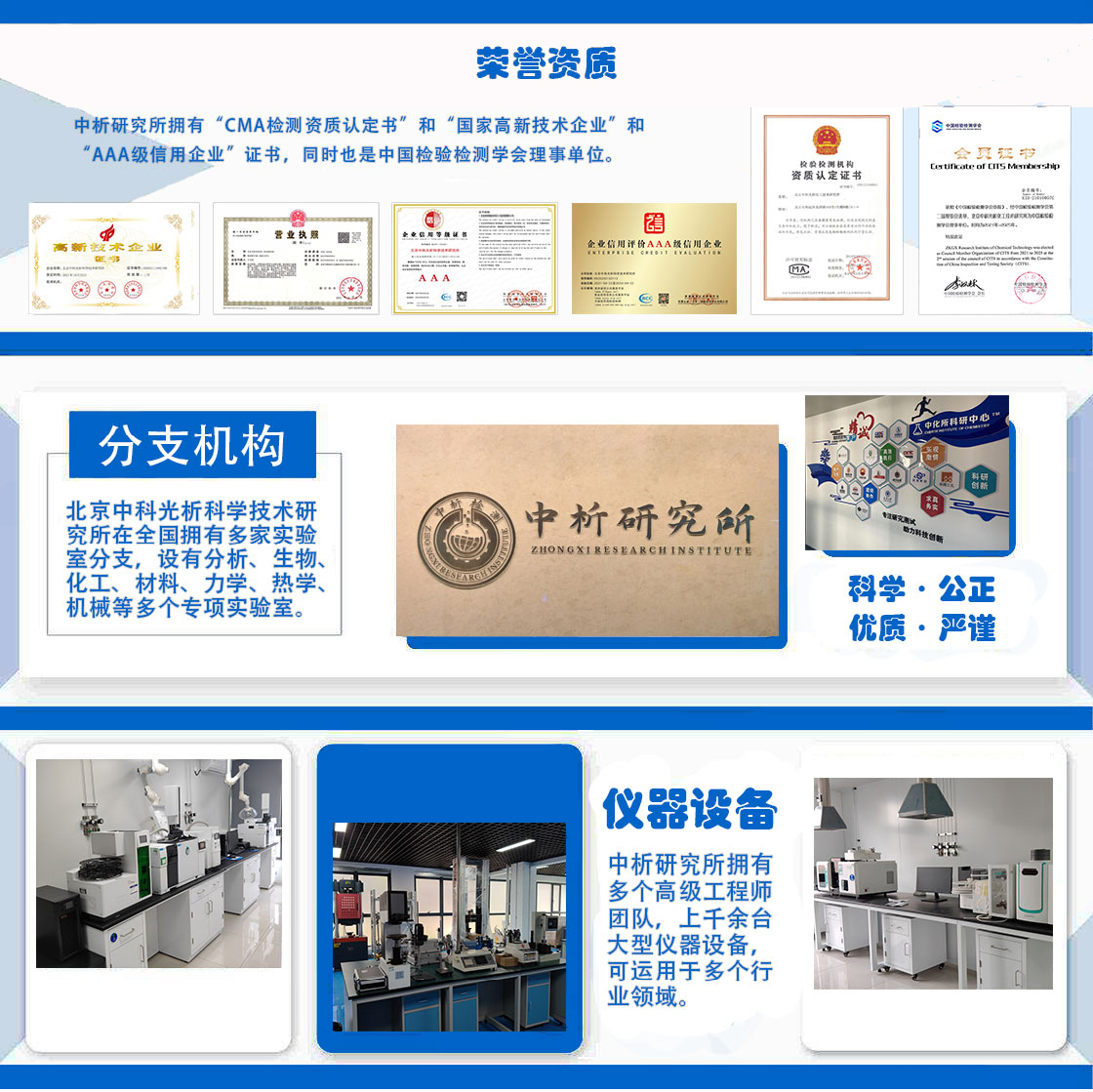
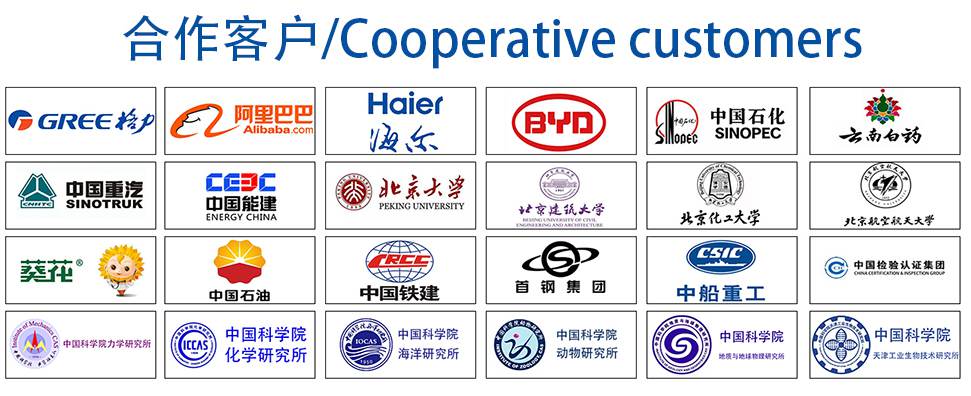