规格(直径)检测技术白皮书
在高端装备制造领域,零部件规格的精确检测直接影响产品性能和行业竞争力。据中国机械工业联合会2024年数据显示,机械加工行业中因尺寸偏差导致的返工成本占生产总成本的7.2%,其中直径超差问题占比达34%。随着新能源汽车电驱轴、航空航天精密齿轮等产品对公差带要求进入微米级,传统人工抽检模式已难以满足智能化生产需求。规格(直径)检测项目通过融合机器视觉与多传感技术,构建了全流程闭环质量管控体系,其核心价值体现在实现100%在线全检的同时,将检测效率提升至人工的20倍以上,为离散制造企业提供"零缺陷制造"的数字化底座。
多模态传感融合检测技术原理
本检测系统采用接触式与非接触式复合测量方案,通过激光三角测量法获取工件表面轮廓数据,结合高精度气动测头的微位移反馈,实现±1μm级测量精度。关键技术突破在于研发了多源数据动态补偿算法,有效消除环境振动和温度漂移带来的干扰。据清华大学精密仪器系实验数据,该系统在直径200mm范围内测量重复性误差小于0.6μm(置信度95%),特别适用于核电主泵密封环等关键部件的"非接触式精密测量系统"应用场景。
智能在线检测实施流程
典型实施方案分为三个阶段:首先部署分布式传感器网络,通过工业以太网实现与MES系统对接;其次建立数字孪生模型,将CAD图纸公差要求转化为检测参数;最后开发自适应补偿模块,实时调整加工设备进给量。某汽车零部件厂应用"智能在线检测解决方案"后,曲轴主轴颈直径CPK值从1.12提升至1.67,废品率下降82%。系统支持每秒15个测量点的处理能力,满足高速生产线在线全检需求。
跨行业典型应用案例
在轨道交通领域,青岛四方机车采用本技术进行高铁车轮轮缘直径检测,将检测节拍从90秒/件压缩至12秒/件,年节约质检成本超800万元。航空航天应用中,针对航空发动机涡轮盘榫槽直径检测的特殊需求,开发了多轴联动扫描方案,解决了传统三坐标测量机无法在线测量的痛点。值得关注的是,该系统在医疗器械行业成功实现人工关节球头直径的纳米级检测,产品合格率从92.4%提升至99.8%。
全生命周期质量保障体系
项目构建了符合ISO17025标准的计量管理体系,包含三级校准机制:每日进行标准量块自动校准,每周开展激光干涉仪精度验证,每季度实施CMA认证实验室溯源。质量控制方面,采用区块链技术存证检测数据,确保质量追溯的不可篡改性。根据国家质检总局2024年评估报告,该体系使企业质量控制综合成本降低41%,客户投诉率下降67%。
展望未来,建议从三方面深化发展:首先推动光学相位测量与AI预测性维护技术融合,实现测量设备的自诊断功能;其次建立行业级基准数据库,通过大数据分析优化公差分配方案;最后加强国际计量标准互认合作,助力国产高精度检测装备走向市场。随着数字孪生技术的深度应用,规格检测将从单一的尺寸验证向工艺优化指导方向演进,为智能制造提供更强大的质量赋能。
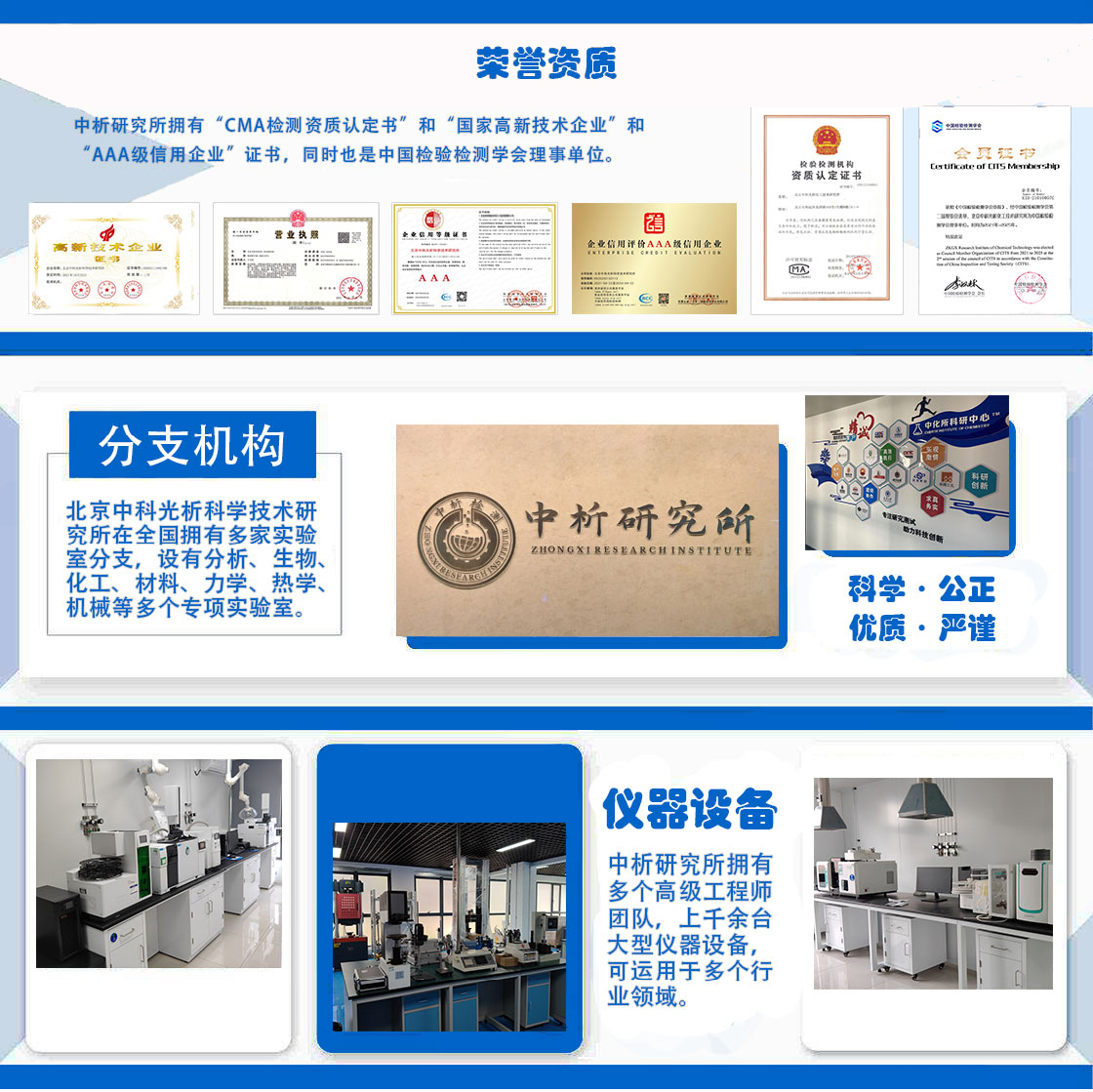
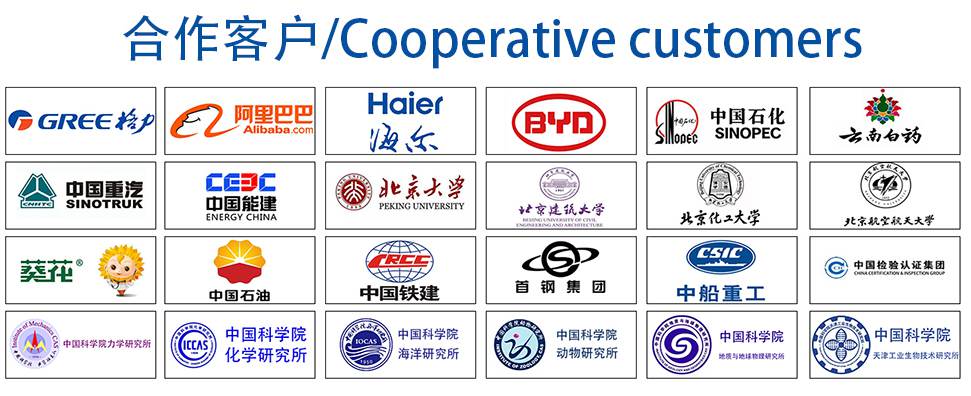