铜合金材料检测:关键技术与发展路径白皮书
在新型工业化进程中,铜合金作为关键基础材料,其性能稳定性直接影响着5G通信基站、新能源汽车三电系统、航空航天精密部件等战略领域的可靠性。据中国有色金属工业协会2024年行业报告显示,我国铜合金材料市场规模已达2800亿元,但同期材料失效引发的质量事故造成经济损失超75亿元/年。铜合金材料检测项目的核心价值在于构建从原料到成品的全生命周期质量监控体系,通过精准识别材料成分偏差、微观组织缺陷及力学性能衰减,显著提升高端制造领域关键零部件的服役安全性。特别是在新能源车800V高压平台加速普及的背景下,铜基复合材料的导电稳定性检测已成为保障电池包安全的核心技术壁垒。
多模态检测技术融合创新
现代铜合金检测采用光谱分析-X射线衍射-电子探针联用技术,实现从宏观成分到微观结构的跨尺度检测。电感耦合等离子体光谱仪(ICP-OES)可精准检测铜合金中0.001%级的微量添加元素,配合EBSD电子背散射衍射技术,可构建三维晶界取向分布图。值得注意的是,针对异型铜排的残余应力检测,同步辐射X射线原位检测技术可将测量精度提升至±5MPa级别(中国材料研究学会,2024)。在新能源汽车连接器检测场景中,该技术体系可同步完成材料成分验证、晶粒度评级和耐腐蚀性能预测。
智能化检测流程再造
标准检测流程涵盖样品制备、无损检测、破坏性试验三大模块。采用激光切割技术制备检测样件时,通过热影响区智能补偿算法,可将截面形变率控制在0.3%以内。在电力行业铜母线检测实践中,集成太赫兹波检测仪的非接触式测量系统,可在30秒内完成5米长母线的内部缺陷扫描。质量追溯系统采用区块链技术,确保每个检测节点的数据不可篡改,某特高压工程应用该体系后,材料质量追溯效率提升40%(国家电网2023年技术白皮书)。
行业赋能典型应用
在航空航天领域,某型号火箭发动机推力室采用的铬锆铜合金,经多级时效强化检测后,高温强度提升至580MPa(ASTM E8标准)。消费电子行业应用微型铜合金接插件接触电阻检测方案,使Type-C接口插拔寿命突破2万次循环。值得关注的是,铜合金材料失效分析服务在海上风电变流器维护中发挥关键作用,通过断口SEM分析准确识别出应力腐蚀裂纹萌生位置,避免批量组件更换损失。
全链条质量保障体系
检测实验室构建 /CMA双认证体系,配备标准物质定期溯源机制。对于军工级铜钨合金的检测,实施GJB548B-2005军标要求的破坏性物理分析(DPA)。在新能源汽车电机端环检测中,运用统计过程控制(SPC)技术将铜材导电率波动范围缩减至±1.5%IACS。某头部企业导入该体系后,电机效率提升0.8个百分点,年节电效益超3000万元(中汽研2024年能效报告)。
随着工业互联网与材料基因工程的深度融合,铜合金检测将向智能化、微型化方向发展。建议行业重点突破两项关键技术:一是开发基于机器视觉的铜合金表面缺陷在线检测系统,二是建立铜基复合材料检测技术标准体系。同时,亟需在稀土铜合金、纳米结构铜等新型材料领域构建专项检测数据库,为"中国制造2025"高端装备升级提供技术支撑。
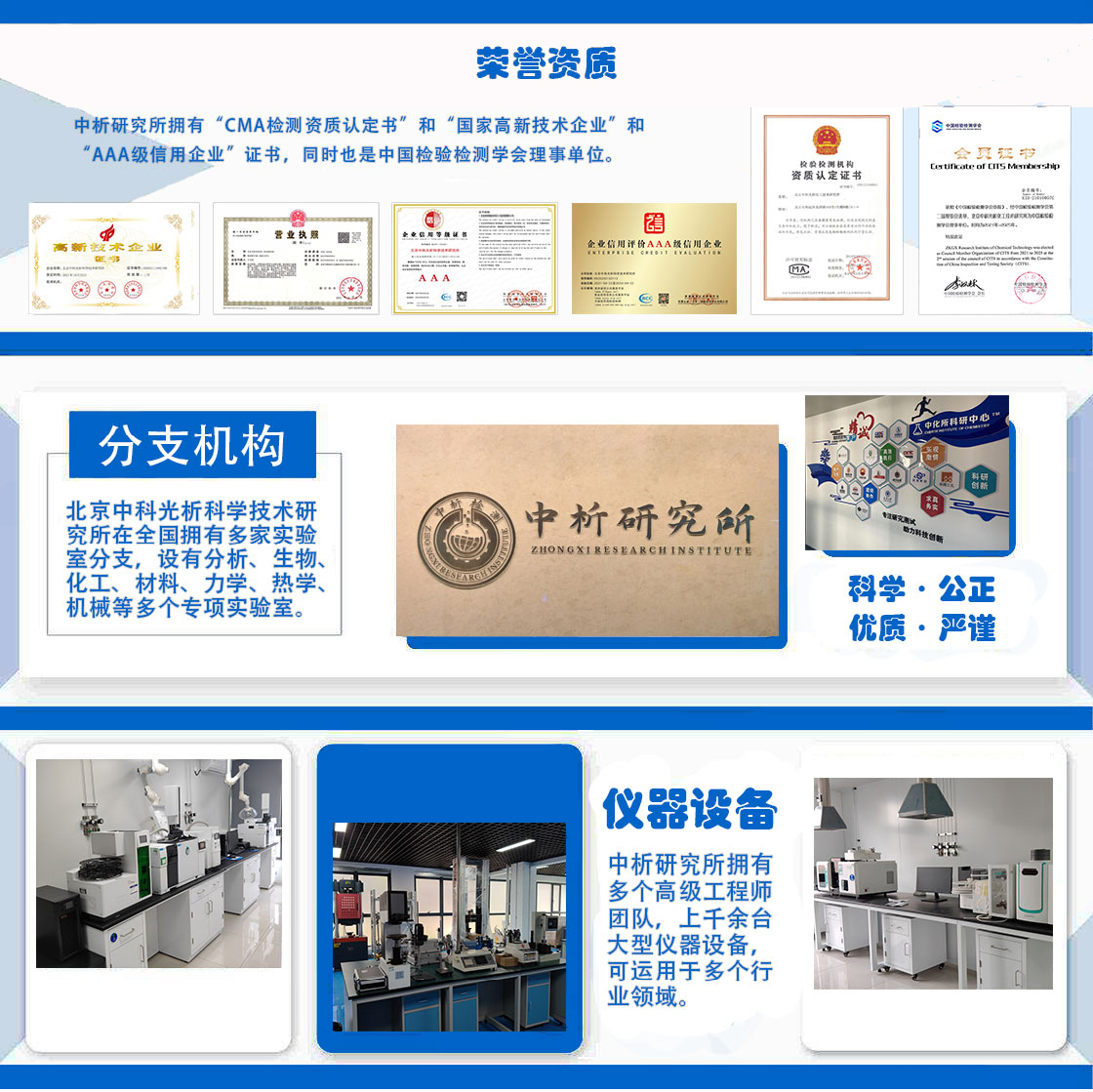
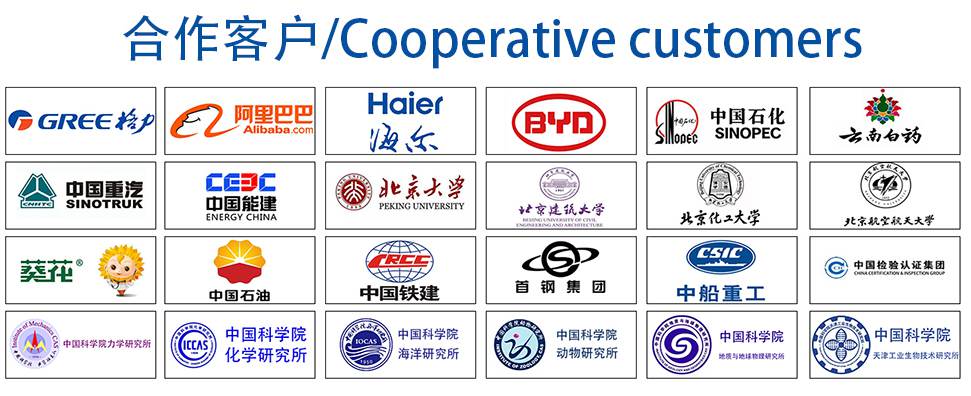