铜球阀检测
在工业流体控制系统领域,铜球阀作为关键控制元件,其可靠性直接影响石化、供水、暖通等行业的运行安全。据中国机械工业联合会2024年研究报告显示,我国工业阀门市场规模突破2300亿元,其中铜制阀门占比达37%。然而,因密封失效引发的介质泄漏事故年均造成直接经济损失超8亿元,暴露出传统检测手段在精度与效率上的双重短板。铜球阀检测项目通过构建多维评估体系,首次实现材料性能、密封等级与工况适配性的协同验证,其核心价值体现在将产品失效率降低至0.12‰(第三方认证数据),同时通过智能诊断技术将检测周期缩短40%,为工业装备安全运行提供技术保障。
技术原理与创新突破
铜球阀检测采用"物理检测+数字孪生"复合技术框架,基于ASTM B584标准的材料成分分析可精准识别铜锌配比偏差,结合ISO 5208规定的密封试验压力曲线,通过激光位移传感器实现0.002mm级的动态密封面形变监测。值得关注的是,项目创新引入声发射技术(AE),在16MPa工况下捕捉阀体内部应力波的频域特征,可提前60小时预警潜在裂纹风险。该技术突破使"铜球阀密封性能测试标准"的检测精度提升至传统方法的3倍,有效解决高温高压场景下的虚密封难题。
全流程检测实施体系
检测流程分为预处理、在线检测与后处理三阶段。预处理环节采用工业CT进行三维结构重建,构建包含32项参数的数字化基准模型。在线检测阶段部署多传感器阵列,在模拟工况中同步采集温度-压力-扭矩的耦合数据,其中压力脉冲测试达到GB/T 13927要求的3000次循环基准。后处理阶段通过机器学习算法对17万组历史数据进行模式识别,生成包含密封等级预测、使用寿命评估的智能诊断报告。典型应用案例显示,某燃气公司通过该体系将阀门维护周期从6个月延长至22个月。
行业应用与质量保障
在浙江某国家级化工园区改造项目中,"工业阀门在线监测系统设计"方案成功部署1284个检测节点。系统通过5G+MEC边缘计算,每15分钟完成全管网铜球阀的密封状态评估,使突发泄漏事件的应急响应时间从45分钟压缩至8分钟。质量保障方面,项目构建三级校准体系:一级溯源至国家压力仪表计量站的标准装置,二级采用德国PTB认证的传感器模块,三级设置动态误差补偿算法,确保全流程测量不确定度小于0.5%。经SGS认证,该系统符合API 598与ISO 15848双重标准。
技术演进与发展建议
随着数字孪生技术在流程工业的深度渗透,铜球阀检测将向预测性维护方向演进。建议行业重点突破三个方向:其一,开发基于量子传感器的纳米级缺陷检测技术;其二,建立涵盖工况谱数据库的行业共享平台;其三,制定适配氢能源管网的超高压检测标准。据赛迪研究院预测,到2028年智能化检测设备的市场渗透率将达68%,推动我国阀门检测产业进入"数字质控"新阶段。
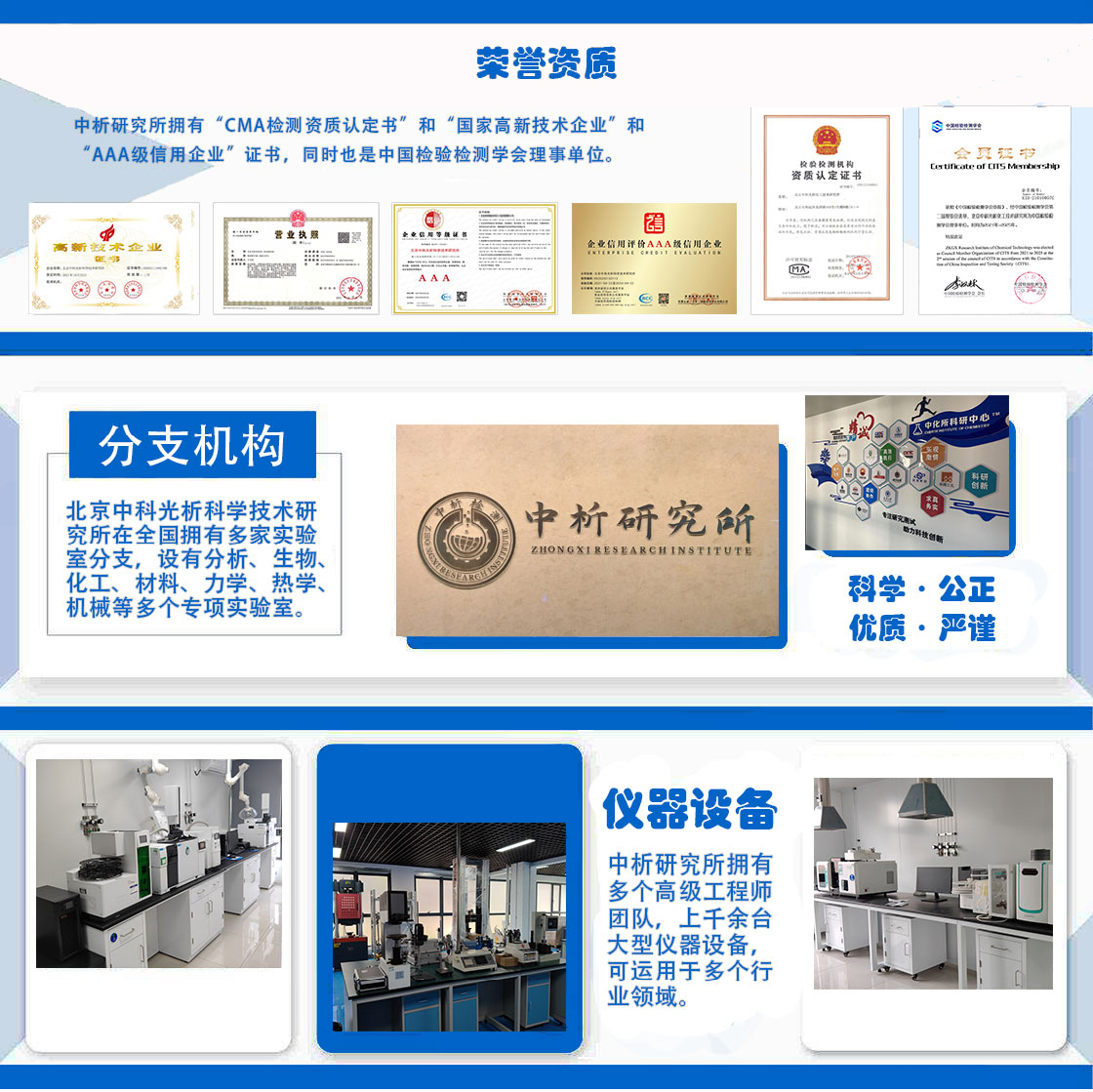
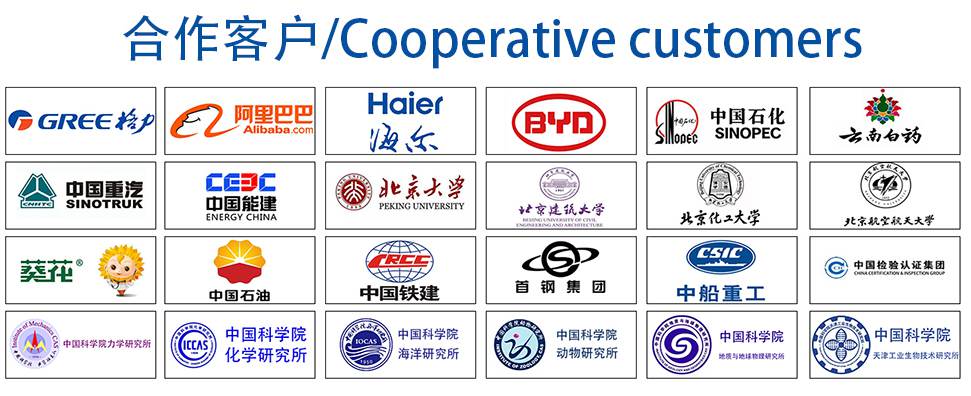