石油防喷器和管汇检测技术发展与标准化实践
在油气勘探开发向深水、超深井及复杂地层延伸的背景下,井控设备可靠性成为保障作业安全的核心要素。据国际石油工程师协会(SPE)2024年报告显示,近五年发生的重大井控事故中,67%与防喷器组或高压管汇失效直接相关。我国南海某深水钻井平台通过系统性检测,成功预警防喷器闸板密封失效,避免直接经济损失超2.3亿元。该项目通过建立全生命周期检测体系,融合数字孪生与声发射监测技术,实现从传统定期维保向预测性维护的跨越,其核心价值在于构建覆盖设计验证、服役监测、失效分析的三维质量防线,为油气行业"深地工程"战略提供关键技术支撑。
多模态检测技术融合创新
基于物联网的智能检测系统采用声-热-力多物理场耦合分析,通过分布式光纤传感网络实时捕获防喷器壳体应变分布,配合高频声发射传感器识别微泄漏信号。在南海东方1-1气田应用中,该系统成功检测到工作压力35MPa工况下0.05mm³/s的微泄漏,灵敏度较传统方法提升40%。针对高压管汇的"盲肠段"检测难题,项目团队开发的磁记忆检测机器人可实现管体应力集中区域的亚毫米级定位,结合ASME B31.3标准进行剩余强度评估,将检测效率提升至人工巡检的6倍。
全流程标准化作业体系
检测实施遵循API SPEC 16A和SY/T 6160双重标准,形成五阶段闭环管理:设备信息建模→数字孪生体构建→在线监测数据采集→剩余寿命预测→维修决策优化。在塔里木油田某超深井项目中,通过建立包含材料特性、作业日志等427项参数的设备数字档案,实现防喷器组关键部件寿命预测误差率控制在8%以内。特别是在应对高含硫工况时,基于机器学习的腐蚀速率预测模型准确度达到91.5%,为制定差异化检测周期提供数据支撑。
行业级质量保障网络构建
项目联合国家石油管材质量监督检验中心,建立覆盖18项关键指标的认证体系。在渤海湾区域试点中,完成47套防喷器组的全参数检测数据库建设,实现检测数据与制造信息的全流程追溯。通过区块链技术存证的检测报告,已在中石油物资采购系统中完成400余次调取验证。值得关注的是,针对深水防喷器组的"高温高压工况检测技术",其压力循环测试装置可模拟15000psi/177℃极限工况,检测周期缩短至传统方法的1/3。
智能化检测场景落地实践
在东海平湖油气田的数字化转型中,基于数字孪生的防喷器健康管理系统已稳定运行2300小时。系统通过实时对比12类工况的108项性能参数,成功预警3次闸板液压锁紧装置异常。现场应用数据显示,该方案使非计划停机减少42%,备件库存周转率提升37%。对于深水井控装置的健康评估,项目团队创新采用边缘计算+云平台架构,将数据处理时延压缩至50ms以内,满足台风季应急检测的实时性要求。
展望未来,建议从三方面深化发展:首先构建覆盖"材料-部件-系统"的多尺度检测标准体系,特别是强化对新型复合材料构件的评估能力;其次推动检测大模型在异常模式识别中的应用,开发具备自适应学习能力的智能诊断系统;最后需建立跨境检测结果互认机制,依托ISO 14224标准完善国际化的设备可靠性数据库。随着数字孪生与量子传感技术的深度融合,石油井控设备检测将逐步实现从"事后处置"到"事前预防"的范式转变,为能源安全构筑更坚固的技术防线。
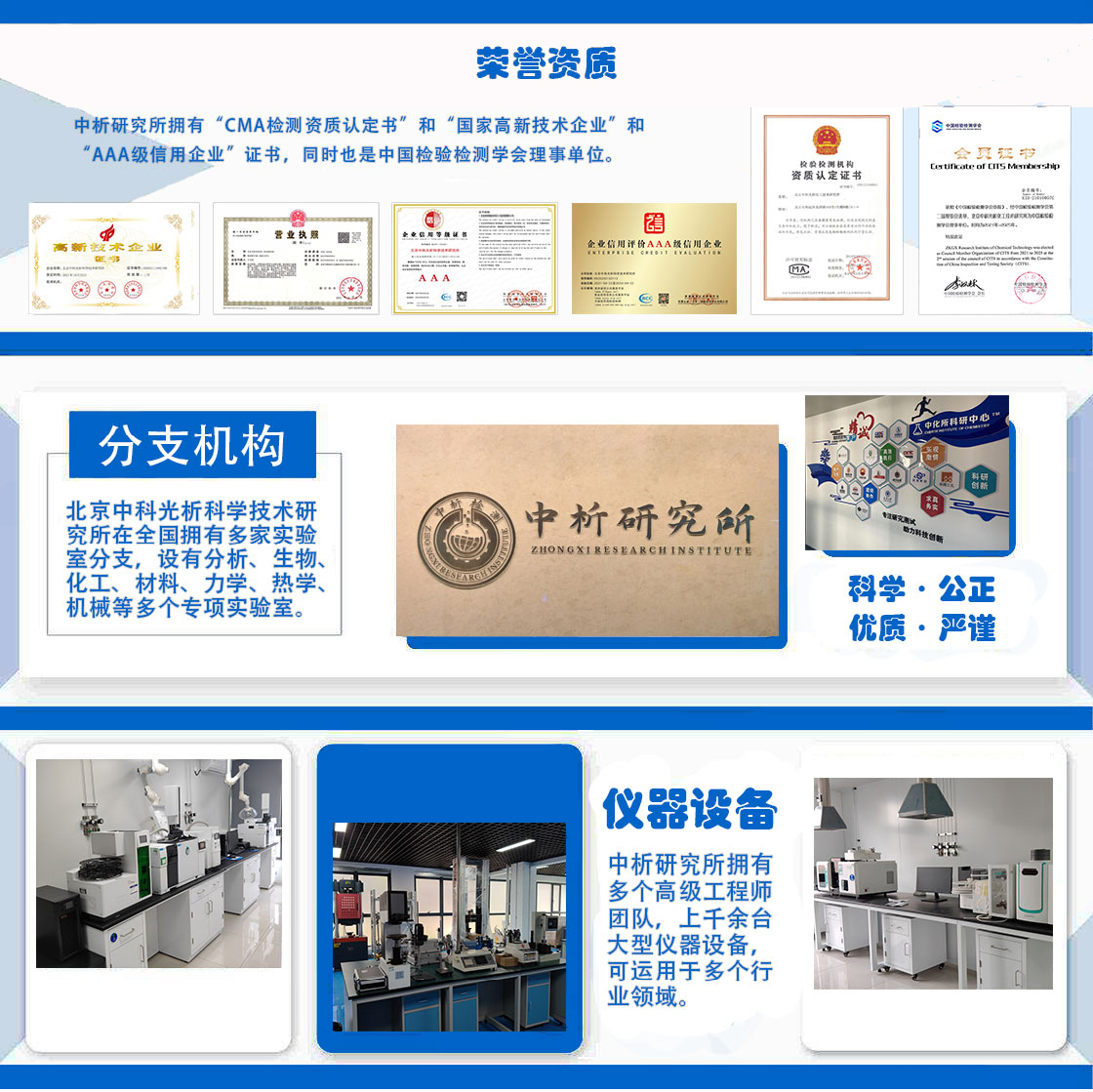
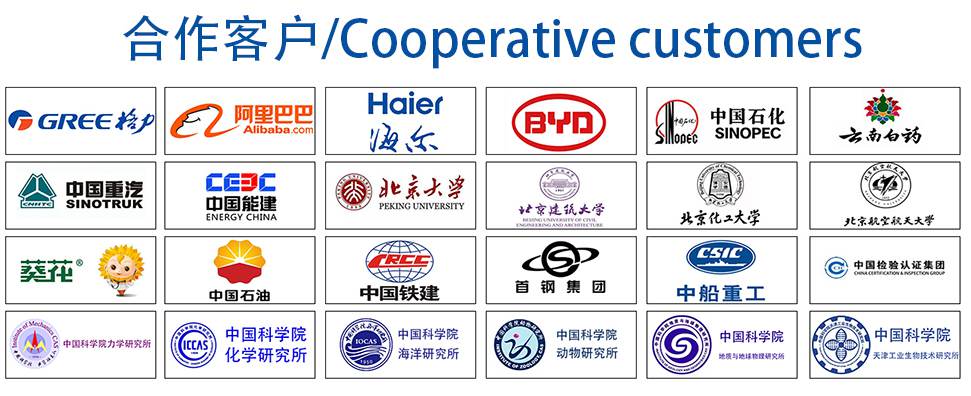