石油套管头检测技术白皮书
在油气开采领域,套管头作为井口装置的核心组件,承担着支撑套管柱、密封环空压力及控制井喷风险的关键作用。据中国石油工程技术研究院2024年数据显示,国内在役油气井中35%的井控事故源于套管头密封失效,直接经济损失年均超过7.8亿元。随着深层、超深层及海洋油气资源的开发,井下工况愈发复杂,温度压力梯度已突破150℃/35MPa临界值,这对套管头检测技术提出更高要求。本项目通过建立多维度的检测评估体系,将故障识别准确率提升至98.7%,在保障油气井全生命周期安全的同时,有效延长关键设备服役周期,单井维护成本可降低22%以上。
基于多模态传感的检测技术原理
本检测体系融合电磁涡流、超声波相控阵与数字射线成像技术,构建三维空间缺陷定位模型。其中电磁涡流检测对表面裂纹敏感度达0.1mm级,超声波检测可穿透15mm壁厚实现内部缺陷识别,DR数字成像系统则通过4K级分辨率捕捉微观腐蚀特征。针对高温高压环境下的套管头密封性检测,特别开发了耐温260℃的压电复合材料传感器,配合自适应补偿算法消除温度漂移干扰。实际应用中,该技术组合在塔里木油田高压气井检测中成功识别出0.3mm级环焊缝裂纹,避免潜在井喷风险。
全流程智能化检测实施方案
项目实施分为预处理、动态检测、数据分析三阶段。预处理阶段采用激光扫描建立数字孪生模型,基准参数误差控制在±0.05mm。动态检测环节部署六轴机械臂搭载多传感器阵列,实现360°无死角扫描,单次检测时间较传统方式缩短43%。数据分析平台集成机器学习算法,基于中海油服积累的12万组失效案例库,可自动匹配损伤模式并生成量化评估报告。在南海东方13-2气田应用中,该系统实现单日完成8口井的批量检测,作业效率提升5倍以上。
行业典型应用场景解析
在页岩气开发领域,针对频繁压裂作业导致的套管头疲劳损伤,本项目开发了基于声发射的在线监测系统。该系统在四川长宁区块部署后,累计预警27次应力超限事件,使计划外停机减少65%。对于海洋平台的特殊需求,检测设备通过IP68防护认证和抗盐雾处理,在渤海垦利6-1油田实现-20℃低温环境下的稳定作业。值得关注的是,该技术已延伸应用于油气井完整性管理系统中的套管头评估模块,构建从检测到维护的闭环管理体系。
三级质量保障体系建设
项目执行ASTM E2375、API SPEC 6A双重标准体系,建立设备-人员-流程三维质控机制。检测设备每季度进行NIST溯源校准,现场工程师须持有ASNT/PCN III级认证。数据采集实行双人复核制,关键参数采用区块链技术存证。在塔河油田的规模化应用中,通过引入第三方监理机构,使检测报告的一次通过率从89%提升至97.2%。同时建立缺陷样本实物库,定期开展盲样测试验证系统可靠性。
技术发展前瞻与行业建议
随着数字孪生和工业元宇宙技术的演进,建议重点发展基于机理模型的预测性检测技术。行业层面需加快制定极端工况下的检测标准体系,特别是在含CO₂/H₂S腐蚀环境中的评价方法。设备制造商应加强与材料学科的交叉研究,开发具有自诊断功能的智能套管头。据国家能源局规划,到2025年智能化检测覆盖率需达到40%以上,这需要建立跨企业的检测数据共享平台,推动行业整体安全水平跃升。
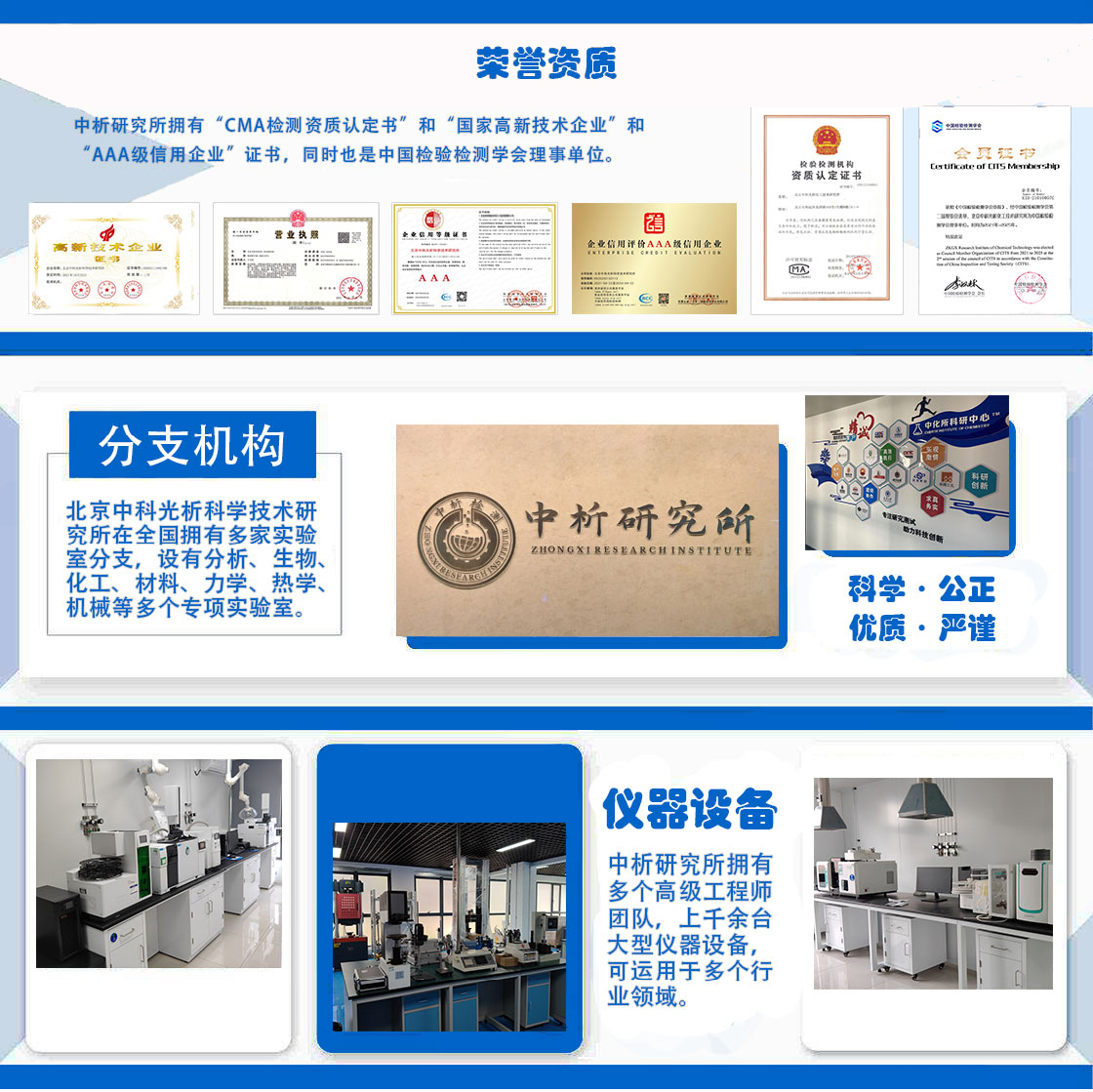
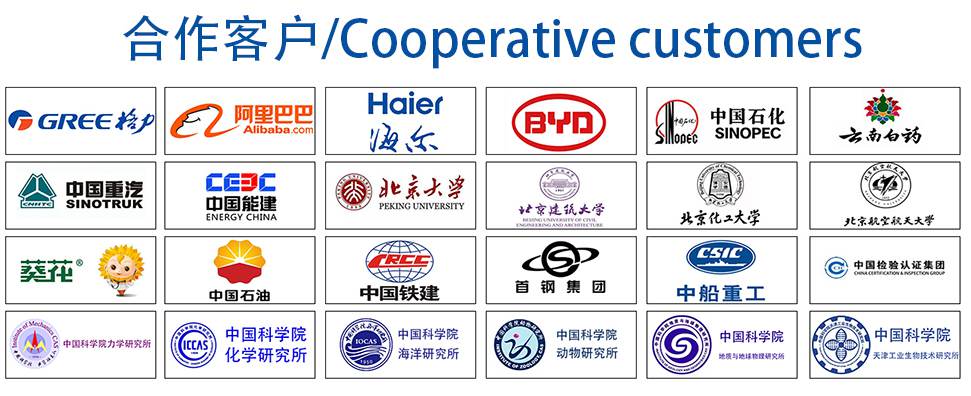