钻杆接头检测的重要性及核心内容
钻杆接头作为石油钻采设备的关键部件,承担着连接钻杆、传递扭矩和承受复杂载荷的重要作用。在钻井作业中,钻杆接头长期处于高温、高压、腐蚀和交变应力的严苛环境下,极易出现磨损、裂纹、变形或螺纹失效等问题。一旦接头发生故障,轻则导致钻井效率下降,重则引发井控事故甚至人员伤亡。因此,通过系统化的检测项目对钻杆接头的性能状态进行科学评估,是保障钻井安全、延长设备寿命的核心手段。
钻杆接头检测的核心项目
1. 外观与几何尺寸检测
通过目视或显微镜观察接头表面是否存在划痕、凹坑、锈蚀等缺陷;使用卡尺、千分尺等工具测量接头的内径、外径、锥度等关键尺寸,确保其符合API 7-1或ISO 11961标准要求。重点关注螺纹区域的磨损情况,防止因尺寸偏差导致密封失效。
2. 无损探伤检测(NDT)
应用超声波探伤(UT)、磁粉探伤(MT)、渗透探伤(PT)等技术检测接头内部及近表面的裂纹、夹杂等缺陷。其中: • 超声波检测适用于检测深度超过3mm的内部缺陷; • 磁粉检测对表面及近表面裂纹敏感度高; • 渗透检测用于非磁性材料的表面开口缺陷排查。
3. 力学性能测试
通过拉伸试验、冲击试验和硬度测试评估接头的抗拉强度、屈服强度及韧性指标。典型要求包括: • 抗拉强度≥965 MPa; • 屈服强度≥862 MPa; • 硬度控制在HRC 22-35范围内,避免材料脆化或软化。
4. 螺纹密封性检测
使用气密性试验台模拟井下高压环境(通常≥70 MPa),检测螺纹连接的密封性能。同时采用三维光学扫描仪对螺纹轮廓精度进行数字化分析,确保啮合度误差小于0.05mm,防止刺漏风险。
5. 疲劳寿命评估
通过有限元分析(FEA)模拟交变载荷下的应力分布,结合旋转弯曲疲劳试验机进行实物验证。重点关注应力集中区域的疲劳裂纹萌生周期,为制定预防性维护策略提供数据支持。
6. 腐蚀与磨损分析
采用金相显微镜观察接头材料的微观组织变化,结合能谱分析(EDS)检测硫化物、氯化物等腐蚀产物的成分。对于表面硬化层,需检测渗碳/氮化层深度(通常要求0.3-0.8mm)以确保耐磨性。
检测技术与标准的匹配性
检测过程中需严格遵循API RP 7G、SY/T 5561等行业标准,同时结合数字孪生、物联网传感器等智能化技术实现实时状态监测。建议每完成800-1200小时钻井作业或每口井结束后进行全面检测,并根据检测结果建立全生命周期管理档案。
结语
钻杆接头检测是一项多学科交叉的系统工程,需综合运用机械、材料、传感等领域的齐全技术。通过标准化检测流程与预防性维护策略的结合,可显著降低钻井作业风险,提升经济效益。未来随着人工智能和机器人检测技术的普及,钻杆接头检测将向更高精度、更高效率方向持续发展。
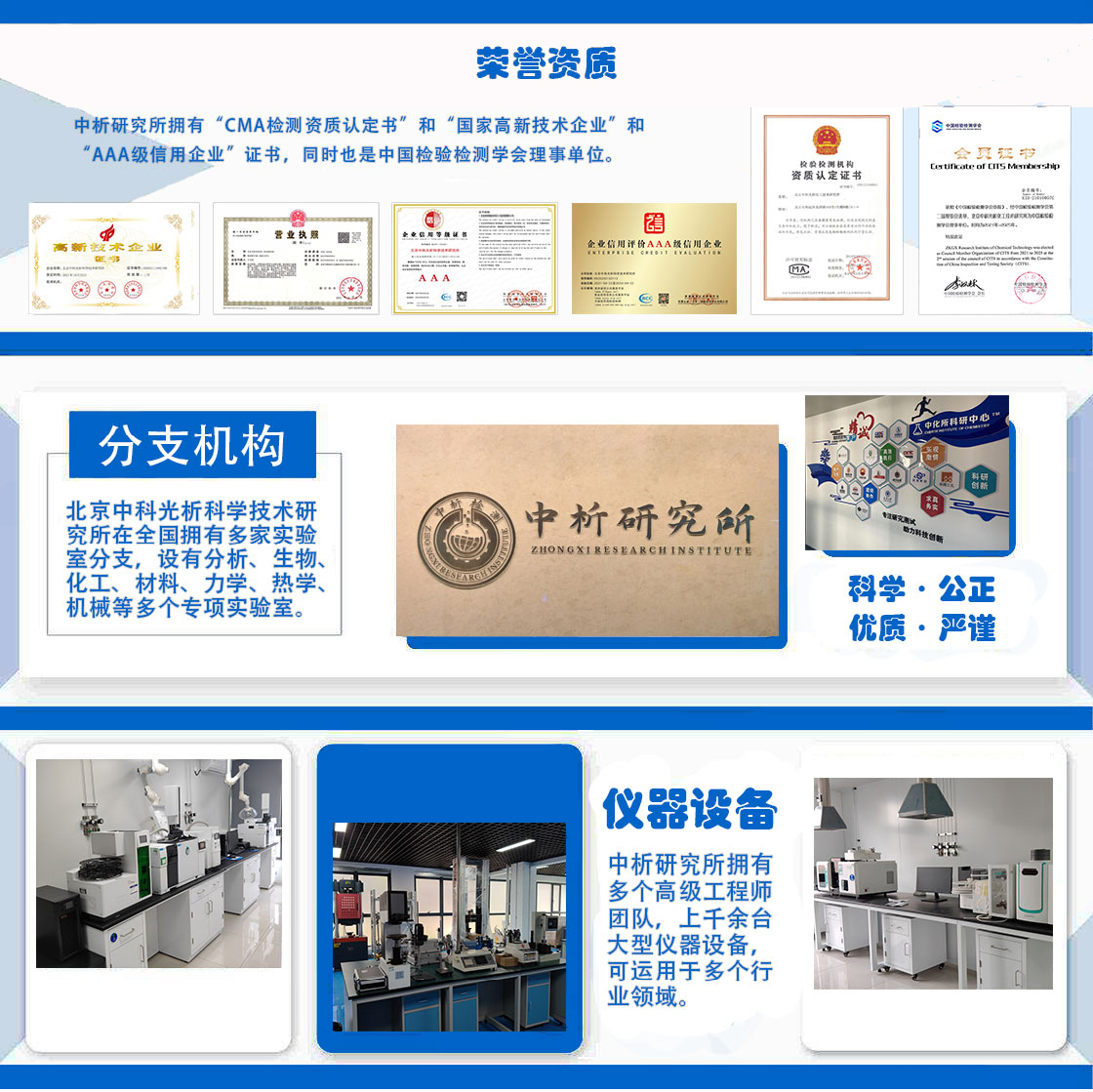
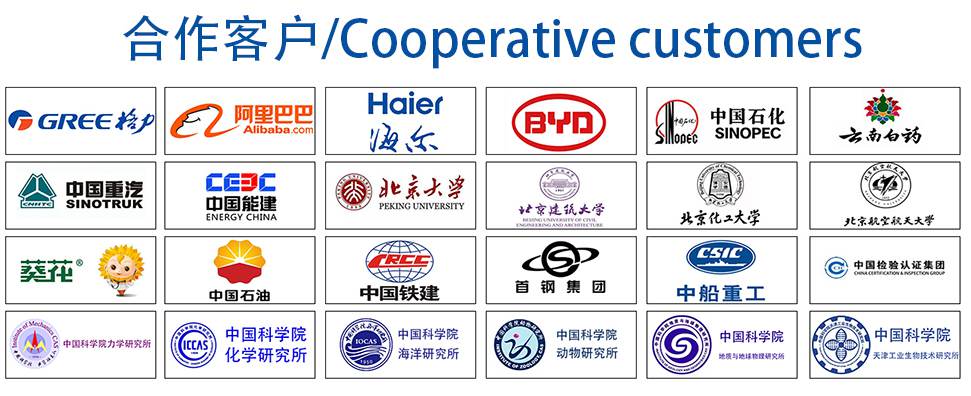