电站管道检测的重要性
在电站运行中,管道系统承担着输送高温、高压蒸汽、水、燃料及化学介质的重要任务。由于长期承受极端工况和腐蚀性介质的侵蚀,管道易出现壁厚减薄、裂纹、焊缝缺陷等问题,一旦发生泄漏或爆裂,可能导致机组停机、安全事故甚至环境污染。因此,电站管道检测是保障设备安全运行、延长使用寿命、优化维护计划的核心环节。通过科学的检测手段,可精准评估管道健康状态,提前发现潜在风险,为制定维修策略提供数据支撑。
电站管道检测的主要项目
1. 管道壁厚测量
采用超声波测厚仪或射线检测技术,对管道关键部位(如弯头、焊缝、腐蚀高危区)进行壁厚扫描。通过对比历史数据与设计标准值,判断材料损耗程度,评估剩余使用寿命。尤其对高温高压蒸汽管道需进行定期连续性监测。
2. 焊缝质量检测
使用X射线探伤、超声波探伤或磁粉检测,检查焊缝内部气孔、夹渣、未熔合等缺陷。对已运行管道还需检测应力腐蚀裂纹和疲劳裂纹,重点关注热影响区及异种钢焊接部位。
3. 腐蚀与结垢评估
通过内窥镜(CCTV)或管道机器人进行内壁可视化检查,结合涡流检测技术,分析管道内部的点蚀、均匀腐蚀和化学沉积情况。对循环水管道需重点监测微生物腐蚀(MIC)和垢层厚度。
4. 泄漏与应力分析
使用红外热成像仪检测热力管道的保温层破损和微小泄漏,配合声发射技术定位气体管道的泄漏点。同时通过应力应变测试仪器,评估管道振动、支撑位移引起的附加应力是否超标。
5. 材料性能检测
对服役多年的管道取样进行金相分析、硬度测试和冲击试验,验证材料是否发生蠕变脆化、老化或强度退化。尤其需关注高温部件材料的微观组织变化。
智能化检测技术的应用
近年来,电站管道检测逐步向智能化方向发展。搭载激光扫描和AI算法的检测机器人可自动生成3D管道模型;分布式光纤传感系统能实现全管段实时应力监测;大数据平台则通过历史数据对比预测剩余寿命,显著提升了检测效率和准确性。
结语
电站管道检测需结合目视检查、无损检测和破坏性试验等多维度手段,依据管道介质特性、运行参数及历史缺陷定制检测方案。通过科学的检测体系与预防性维护策略,可最大限度降低管道失效风险,确保电力生产安全经济性。
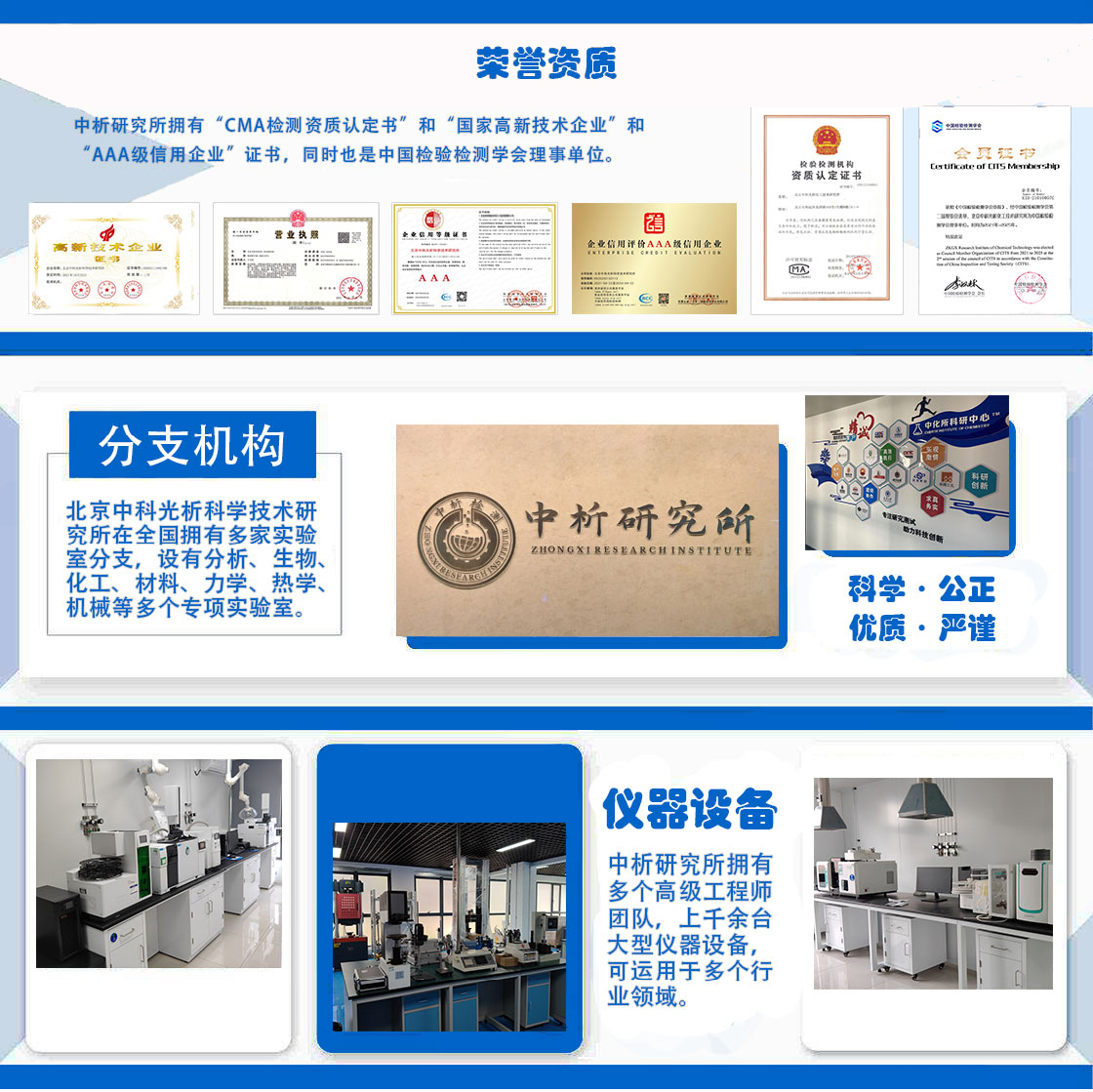
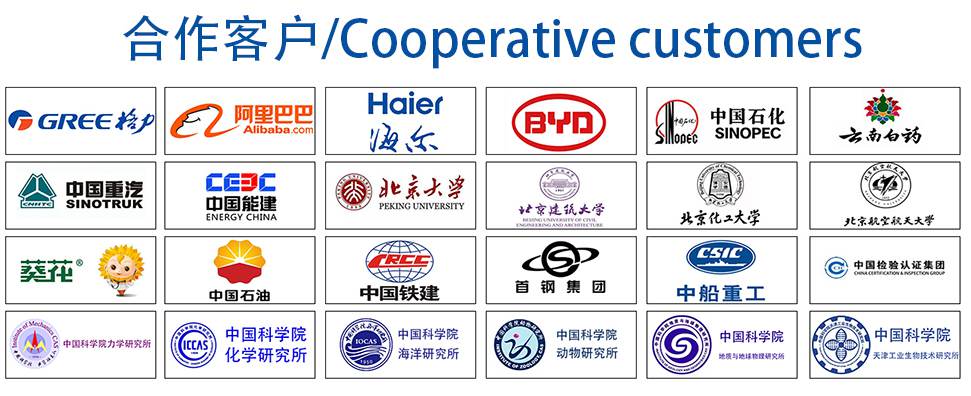