煤炭联合制样系统检测的重要性与核心内容
煤炭联合制样系统是煤炭检测流程中的核心设备,承担着破碎、缩分、干燥、混合等关键制样任务,其性能直接影响最终化验结果的准确性。由于煤炭具有成分复杂、粒度不均、易挥发等特点,制样系统必须满足密封性、精度控制、重复性等多项技术指标。通过系统化的检测验证,可确保设备符合国标(如GB/T 19494)和行业规范要求,规避因制样偏差导致的贸易纠纷、质量误判等问题。检测范围覆盖机械性能、功能模块、环境适应性等多个维度,是保障煤炭检测数据公信力的重要环节。
煤炭联合制样系统核心检测项目
1. 系统密封性检测
重点评估设备在运行过程中粉尘泄漏情况,使用颗粒物监测仪在破碎机、缩分器等关键节点进行动态测试。密封不良会导致样品交叉污染和重量损失,需确保各接口漏风率≤3%,粉尘浓度符合《煤炭制样室技术规范》要求。
2. 粒度分布均匀性检测
通过多级筛分实验验证破碎后物料粒度分布是否符合目标范围(如≤3mm或≤0.2mm)。采用激光粒度分析仪对比不同批次样本,要求95%以上颗粒满足设定标准,并核查破碎机刀片磨损对粒径的影响趋势。
3. 水分损失控制检测
针对干燥模块进行热稳定性测试,使用恒温烘箱对比干燥前后样品水分含量变化。要求全水分损失率≤0.5%,且干燥温度波动范围控制在±2℃内,避免因过热导致挥发分异常变化。
4. 缩分精度验证
通过对比缩分器留样与弃样的灰分、发热量等指标差异,计算缩分比误差。按照ISO 13909标准,要求缩分后子样间灰分差异≤0.3%,缩分器切割速度与样品流动速度的匹配度误差≤5%。
5. 系统残留率测试
采用示踪法(如荧光标记颗粒)测定设备内部残留物料量,单次运行后残留率应≤0.1%。对于连续作业系统,还需模拟72小时运行后的累积残留情况,防止陈旧样本污染新批次样品。
6. 自动化功能验证
检测PLC控制系统对参数(破碎时间、缩分频率等)的精确执行能力,包括异常工况下的报警响应、故障自诊断功能。要求程序控制误差≤1%,紧急停机响应时间≤2秒,确保无人值守时的运行可靠性。
7. 环境适应性检测
模拟高湿度(RH≥85%)、低温(-20℃)等极端工况下的设备性能,评估电气元件防护等级(需达到IP54以上)、防冷凝设计有效性,以及振动噪声是否符合≤75dB(A)的环保标准。
检测方法与标准依据
检测过程需严格参照GB/T 211-2017《煤中全水分的测定方法》、GB/T 474-2008《煤样的制备方法》等标准,结合JJF(煤炭) 01-2018《煤炭制样设备校准规范》开展仪器校准。第三方检测机构还需通过CMA/ 认证,确保检测报告的法律效力。
结语
定期开展煤炭联合制样系统检测,不仅可及时发现设备老化、参数漂移等问题,更能从源头上提升煤炭质检数据的可信度。建议企业建立季度巡检制度,重点监控破碎模块磨损率、缩分器机械间隙等易损部件,配合大数据分析实现预测性维护,为煤炭贸易、燃烧优化及清洁利用提供坚实的技术支撑。
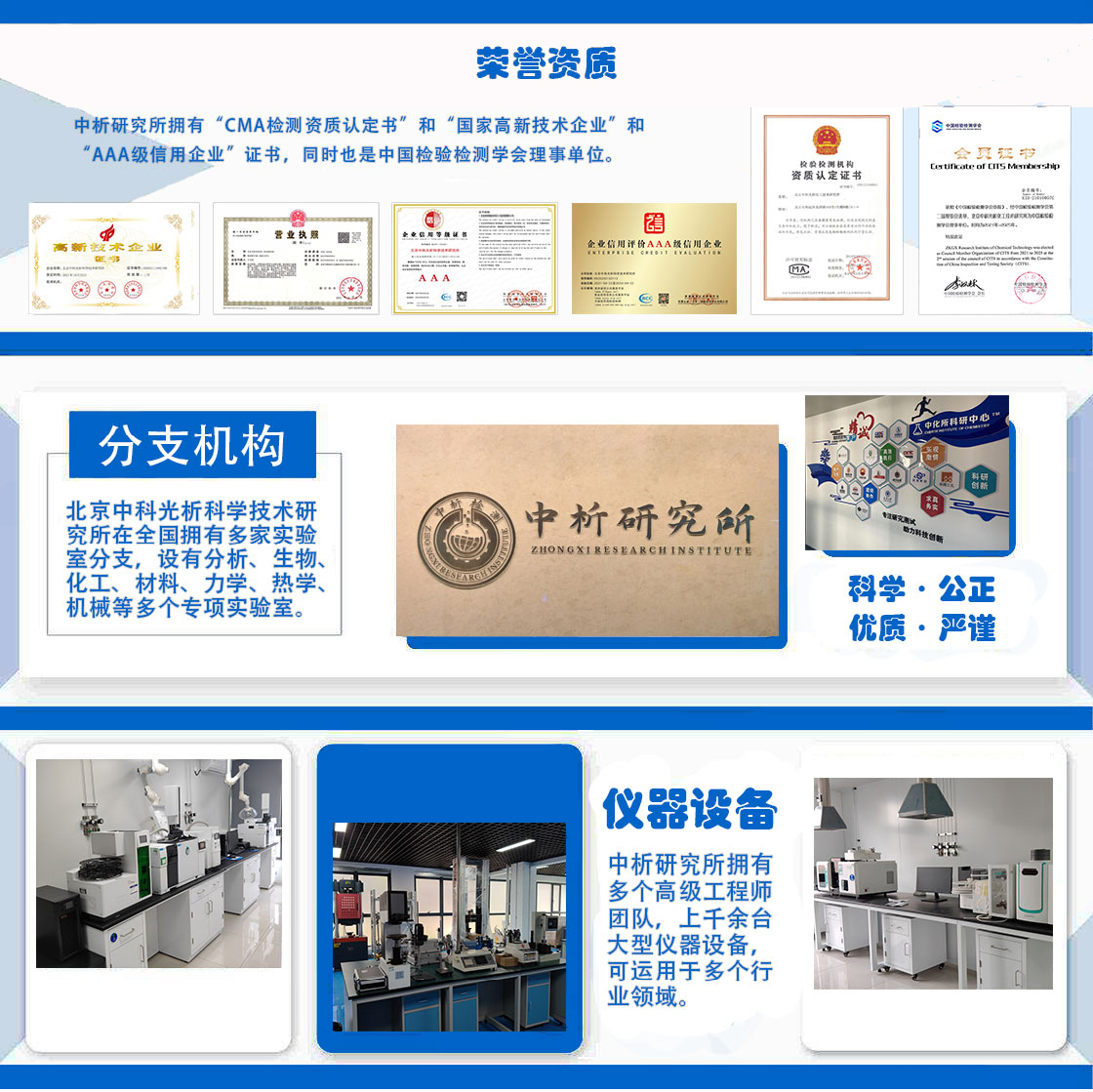
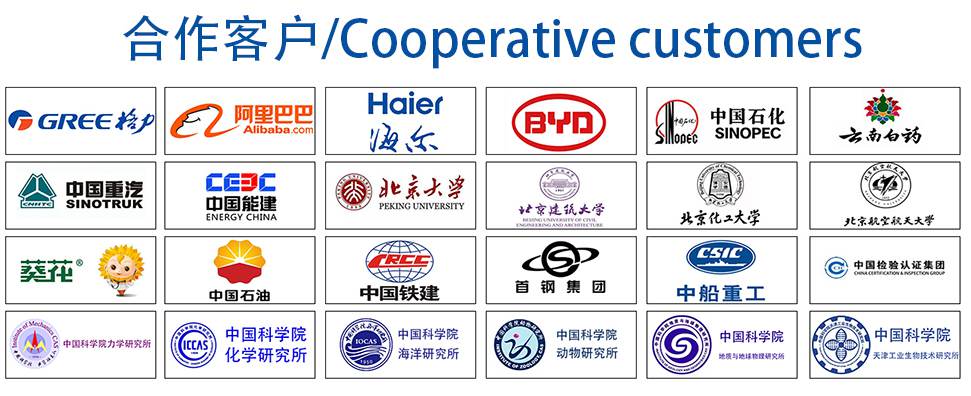