油气井用传爆管检测的重要性
油气井用传爆管是油气开采过程中实现射孔作业的核心部件,其性能直接关系到井下作业的安全性和有效性。作为连接起爆装置与射孔弹的关键媒介,传爆管需具备高可靠性、耐高温高压及稳定传爆能力。在复杂的地下环境中,任何材料缺陷、密封失效或结构损伤都可能导致传爆失败,甚至引发井控风险。因此,系统化的检测项目不仅是行业规范要求,更是保障油气开采安全、提升作业效率的基础环节。通过科学的检测手段,可有效预防因传爆管失效造成的经济损失和安全隐患,同时为设备选型与维护提供数据支撑。
核心检测项目及技术标准
1. 物理结构完整性检测
采用工业内窥镜对传爆管内部通道进行可视化检查,结合三维测量仪评估管体尺寸公差。重点检测螺纹连接部位的磨损程度、管壁厚度均匀性以及是否存在裂纹、变形等缺陷,确保符合API RP 67等行业标准要求。
2. 材料性能分析
通过光谱分析仪检测合金材料的元素配比,使用金相显微镜观察微观组织结构。开展硬度测试(布氏/洛氏硬度计)和拉伸试验,验证材料在高温(最高180℃)高压(≥100MPa)环境下的抗蠕变性能和抗冲击韧性。
3. 密封性及耐压测试
采用氦质谱检漏仪进行气密性检测,灵敏度需达到1×10⁻⁹ Pa·m³/s级别。动态压力测试模拟井下实际工况,通过液压试验台实施循环压力加载(0-150MPa),持续监测泄漏量并记录形变数据,确保在极端压力下保持结构密封。
4. 传爆可靠性验证
搭建模拟井筒试验装置,使用高速摄影机(帧率≥100,000fps)记录爆轰波传递过程。通过冲击波传感器阵列测量爆速(要求≥8000m/s)和压力峰值,结合雷管起爆同步性测试(误差<0.1μs),验证传爆序列的精确性和稳定性。
5. 环境适应性测试
在H2S/CO₂腐蚀模拟舱中进行30天加速腐蚀试验,检测管体耐酸性。开展温度冲击测试(-40℃至200℃快速循环),评估材料热膨胀系数和绝缘层性能。盐雾试验(按ASTM B117标准)验证表面防护体系的耐久性。
智能检测技术应用趋势
随着数字化技术的发展,基于AI的缺陷自动识别系统已开始应用于X射线探伤图像分析,检测效率提升40%以上。无线传感器网络可实现井下实时状态监测,结合大数据平台对历史检测数据进行趋势预测。激光诱导击穿光谱(LIBS)技术为现场材料成分分析提供了非破坏性解决方案,推动检测流程向智能化、高精度方向演进。
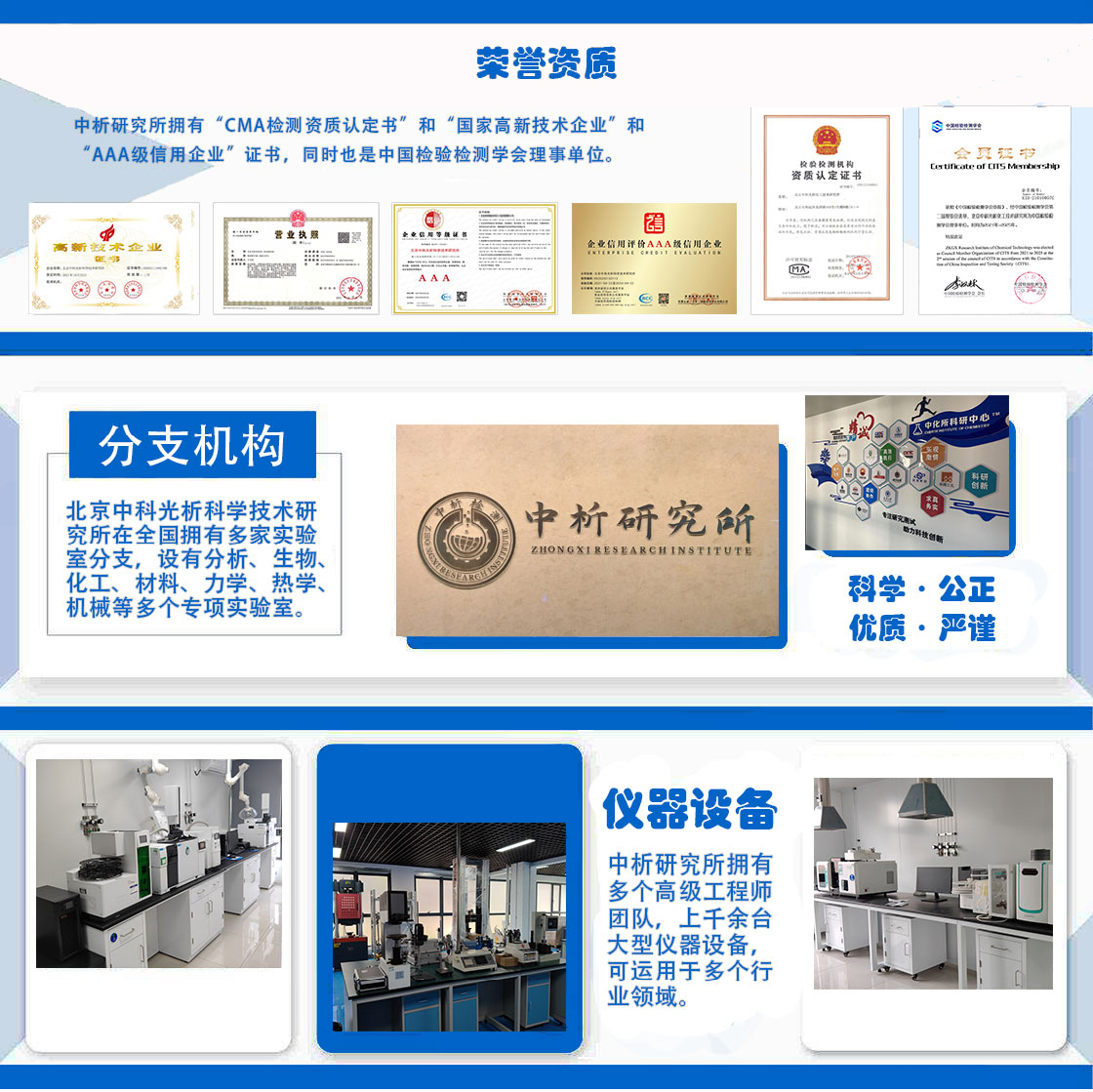
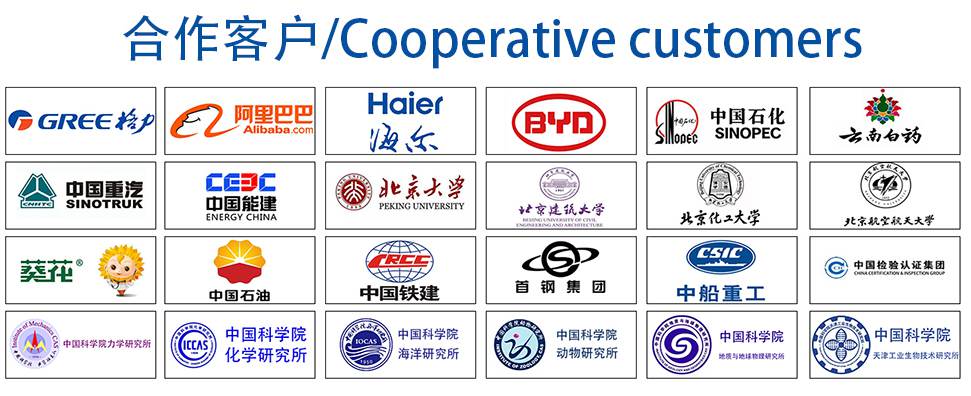