离线编程式机器人检测项目的关键技术与应用场景
在智能制造和工业4.0的快速发展背景下,离线编程式机器人因其高效、灵活的特点,已成为现代工厂自动化改造的核心设备。这类机器人通过虚拟仿真环境完成程序设计与优化后,再将代码直接部署到实体机器人执行任务,极大减少了生产线停机时间。然而,为确保离线编程结果的可靠性,必须建立完善的检测体系,涵盖从仿真精度到实际运行的全流程验证。
核心检测项目及实施方法
离线编程机器人检测体系包含五大关键模块,每个模块对应特定的技术指标和验证标准:
1. 虚拟仿真精度检测
通过激光跟踪仪与数字孪生系统比对,验证虚拟环境中机器人运动轨迹与实际物理空间的偏差值。要求重复定位精度误差≤0.05mm,关节运动角度偏差≤0.1°,符合ISO 9283标准中的B级精度要求。
2. 路径规划合理性检测
采用动态碰撞检测算法(如GJK算法)与动作连贯性分析工具,确保程序路径不存在冗余动作或逻辑冲突。典型测试案例包括多机器人协同焊接路径的避让验证,需满足节拍时间预设值±5%的波动范围。
3. 碰撞干涉检测
基于三维点云扫描技术构建高精度环境模型,在DELMIA/Visual Components等仿真平台中进行多维度碰撞预演。重点检测工具坐标系(TCP)与夹具、工件的最小安全距离,要求静态干涉余量≥3mm,动态运动过程≥5mm。
4. 通信协议兼容性测试
针对EtherCAT、Profinet等工业总线协议,使用Packet Analyzer进行数据包完整性验证。测试项目包括指令延迟(≤2ms)、数据传输丢包率(<0.01%)以及异常中断恢复能力,确保程序传输过程稳定可靠。
5. 程序运行稳定性验证
在实体机器人上连续运行200次完整工作循环,记录关键参数波动情况。考核指标包含定位精度衰减率(≤3%)、伺服电机温升(ΔT≤15℃)以及故障停机次数(≤1次/千循环),通过Weibull分析评估系统可靠性。
行业应用与价值提升
在汽车制造领域,某知名车企通过实施该检测体系,将新车型焊接机器人调试周期从28天缩短至9天,路径规划效率提升40%,每年减少因程序错误导致的停产损失超120万元。检测数据的深度分析还为工艺优化提供了量化依据,帮助产线整体OEE提升12.6%。
随着数字孪生与AI技术的融合,离线编程机器人检测正朝着智能诊断方向发展。未来将通过机器学习算法建立偏差预测模型,实现检测流程的自主优化与异常预警,为智能制造提供更强大的技术支撑。
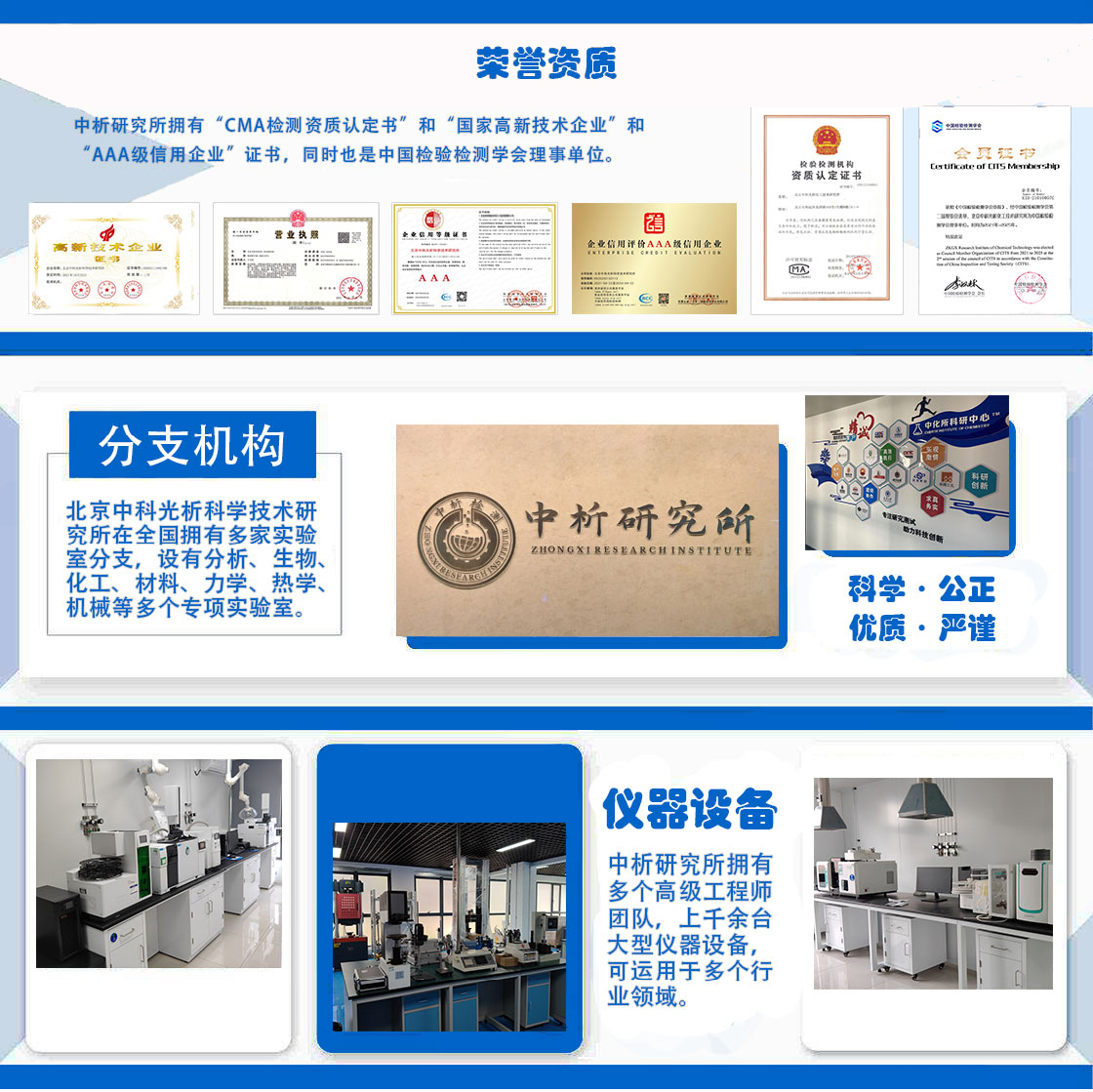
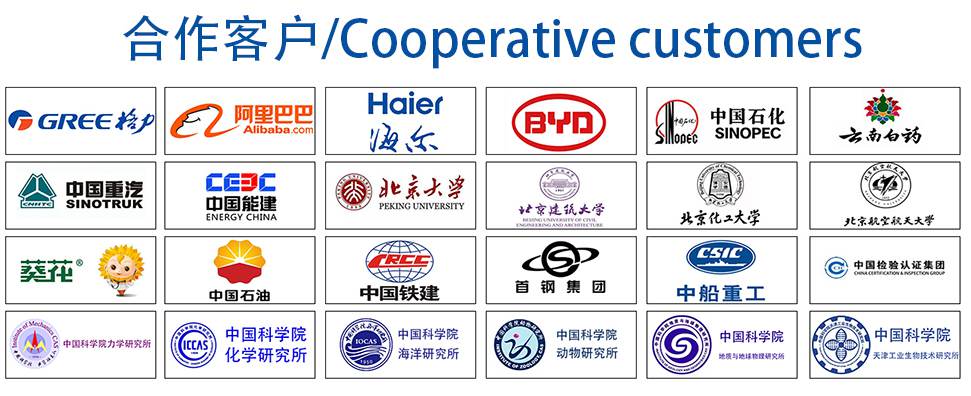