机车、动车组用活塞空气压缩机组检测技术解析
活塞空气压缩机组作为机车与动车组制动系统、车门控制、辅助设备供气的核心动力源,其运行状态直接影响列车安全性与稳定性。随着铁路运输向高速化、智能化发展,对压缩机组的性能、可靠性及能效提出了更高要求。通过系统化的检测项目,能够有效评估机组在振动、温升、排气量、密封性等关键指标上的表现,确保其在复杂工况下的长期稳定运行。
一、基础性能检测项目
1. 气密性测试:采用压力衰减法检测机组整体密封性,要求30分钟内压力降不超过设计值的5%
2. 排气量检测:通过流量计测量额定转速下的实际排气量,比对标称值偏差需控制在±3%以内
3. 工作压力测试:验证最高工作压力下的持续运行能力,监测压力波动是否在允许范围
二、关键部件专项检测
1. 活塞环磨损检测:使用内窥镜配合激光测微仪测量环槽间隙,磨损量超过0.15mm需更换
2. 气阀组效能测试:采用声发射技术监测阀片启闭状态,检测泄漏率是否达标
3. 润滑系统检测:分析润滑油金属颗粒含量,当铁元素浓度>80ppm时预警异常磨损
三、工况适应性检测
1. 低温启动测试:在-40℃环境下模拟冷启动,记录达到额定转速所需时间及压力建立曲线
2. 高频振动试验:施加50Hz/5g振动载荷,检测螺栓紧固件松动及壳体共振现象
3. 湿热循环测试:85%RH湿度环境下进行100次热冲击循环,评估绝缘性能劣化程度
四、能效与环保检测
1. 比功率检测:基于ISO1217标准计算单位排气量的能耗值,新一代机组需≤5.2kW/(m³/min)
2. 噪声频谱分析:采用声压级计在1m距离多方位测量,A计权噪声值应低于85dB(A)
3. 排放物检测:检测曲轴箱废气中的颗粒物浓度,满足GB20891非道路移动机械排放限值
五、智能检测技术应用
1. 在线监测系统:集成压力、温度、振动传感器,实现实时数据采集与趋势分析
2. 数字孪生诊断:建立三维仿真模型,通过运行数据比对预测剩余使用寿命
3. AI故障识别:利用深度学习算法分析异常波形,诊断准确率可达92%以上
根据TB/T 2711-2015《铁路机车车辆用空气压缩机试验方法》,检测周期应结合运行里程和工况强度制定。建议每15万公里或12个月开展全面检测,高速动车组需缩短至8个月。通过科学的检测体系与智能化技术融合,可将压缩机故障率降低67%,显著提升列车运维经济性与安全性。
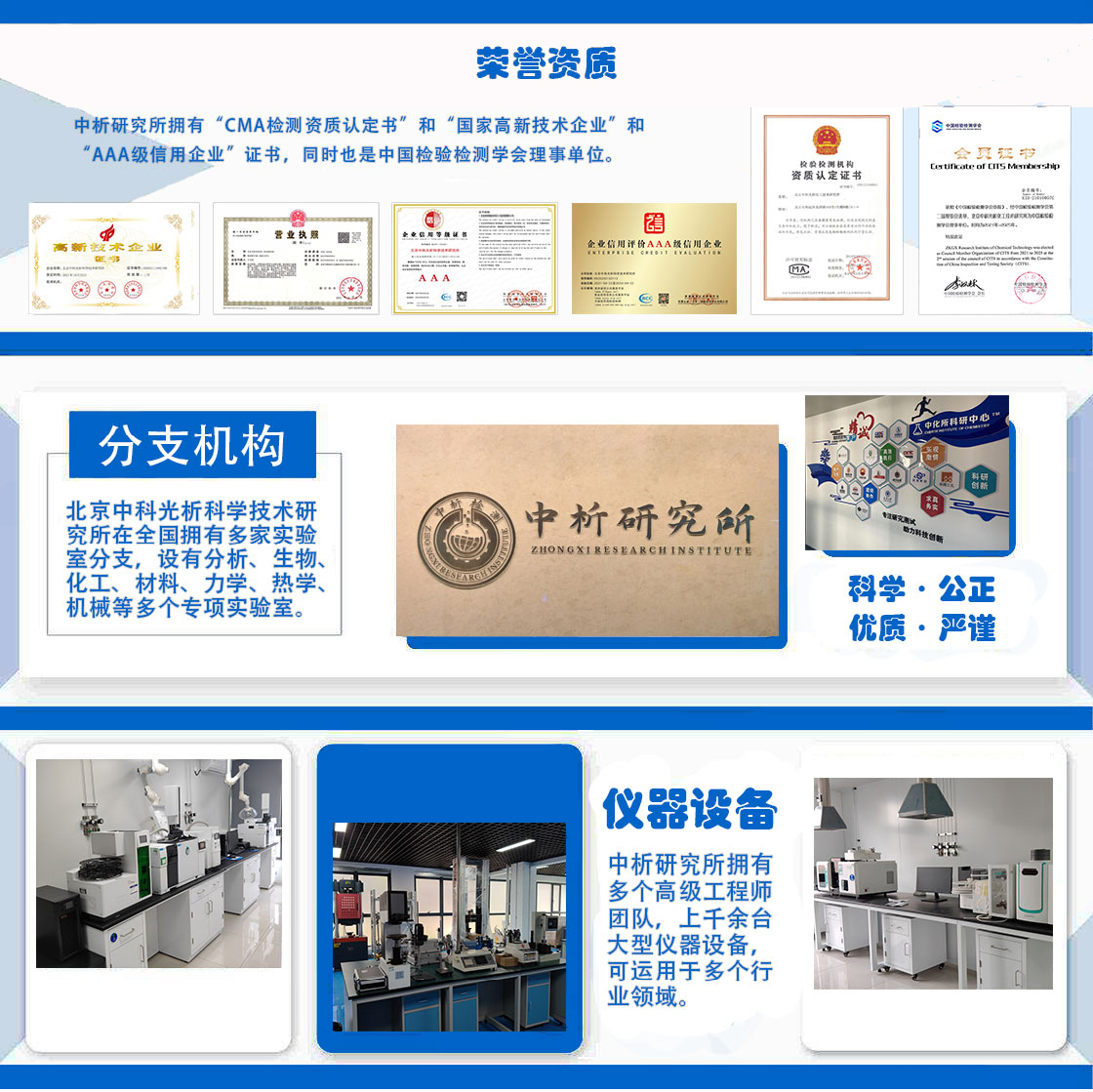
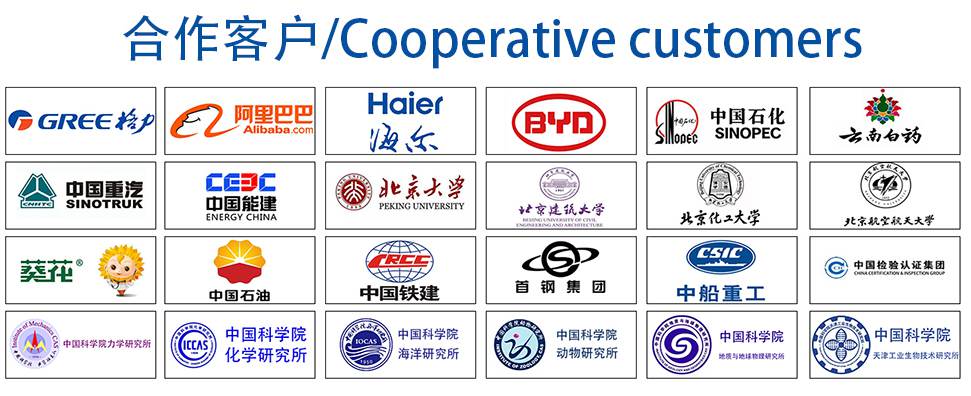