石油化工离心泵能效检测的重要性
石油化工生产过程中,离心泵作为输送液体介质的核心设备,其能效水平直接关系到能源消耗、运营成本和环境保护。随着能源紧缺问题的加剧以及“双碳”目标的推进,对离心泵的能效检测成为石油化工企业优化工艺流程、实现节能降耗的关键环节。能效检测不仅有助于评估设备的运行状态,还能通过数据反馈指导设备选型、维护和改造,最终提升整体生产效率。当前,国际和国内标准(如ISO 5198、GB 19762等)对离心泵能效提出了明确要求,企业需通过科学检测手段确保设备符合规范,同时挖掘节能潜力。
离心泵能效检测的核心项目
1. 运行参数监测
包括流量、扬程、转速、轴功率等基础参数的测量。通过对比设计值与实际值,判断泵是否处于高效区运行。例如,流量偏离额定值可能导致效率下降,需调整工况或优化控制策略。
2. 机械效率测试
利用扭矩仪、功率分析仪等设备测量泵的输入功率和输出功率,计算机械效率(ηm)。机械损耗主要来源于轴承摩擦、密封件阻力和转子不平衡等,效率值低于标准时需排查部件磨损情况。
3. 流体特性分析
检测介质的黏度、密度、含气率等物性参数,评估其对泵效的影响。例如,高黏度液体会增加流动阻力,需结合介质特性重新核定泵的扬程-流量曲线,必要时调整叶轮设计。
4. 系统匹配度评估
检查泵与管道系统的匹配性,包括进出口管路阻力、阀门开度合理性以及NPSH(净正吸入压头)是否满足要求。系统设计不当会导致泵的扬程浪费或汽蚀风险,显著降低能效。
5. 能源消耗计算
通过实时监测电能消耗,结合运行时间与工况,计算单位流量或单位扬程的能耗指标。对比行业标杆值或历史数据,识别异常能耗点并制定改进措施。
6. 维护保养状态检测
定期检查密封件、轴承、叶轮等关键部件的磨损程度,避免因机械故障导致的效率损失。例如,叶轮腐蚀或结垢会改变流道形状,直接影响泵的水力性能。
能效检测结果的应用与优化
检测数据需形成动态分析报告,指导企业进行设备升级、变频改造或替换为高效节能泵。例如,采用CFD(计算流体力学)模拟优化叶轮结构,或引入智能控制系统实现工况自适应调节。此外,建立能效检测数据库可为设备全生命周期管理提供依据,助力石油化工行业实现绿色低碳转型。
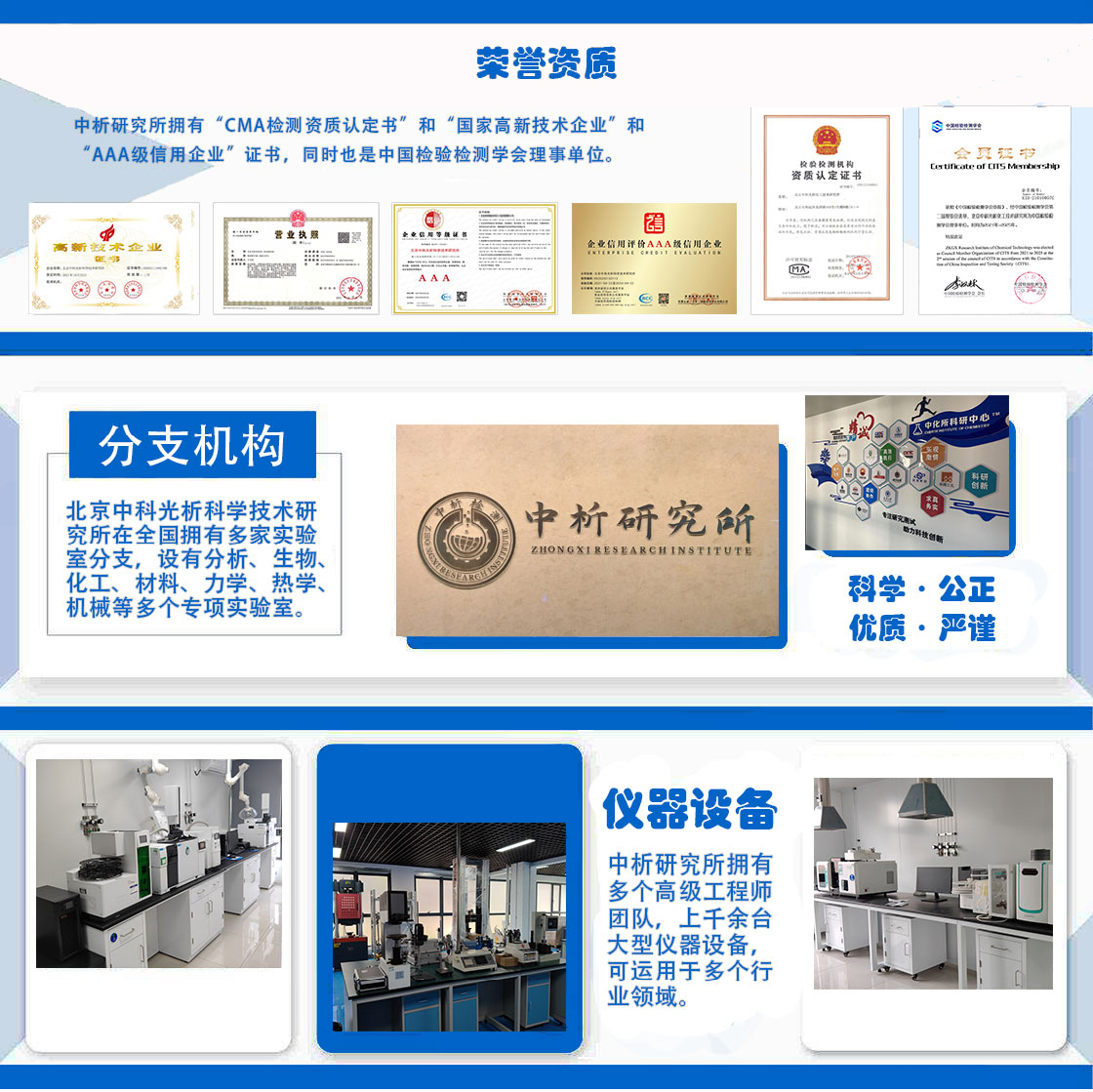
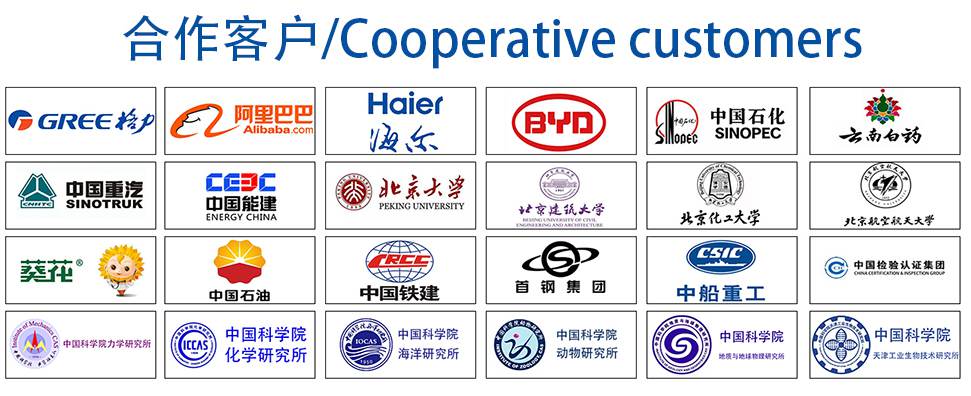