螺杆空气压缩机检测的重要性与核心项目解析
螺杆空气压缩机作为工业生产中重要的动力设备,广泛应用于机械制造、化工、食品加工等领域。其运行状态直接影响生产效率、能源消耗及设备安全性,因此定期开展系统性检测是保障企业稳定生产的关键环节。通过科学规范的检测手段,可及时发现设备潜在隐患,延长使用寿命,降低维护成本,同时满足国家特种设备安全技术规范要求。
核心检测项目及实施要点
1. 气密性检测
使用高精度压力表测量系统保压能力,检查管路、接头、密封件等部位的泄漏情况。采用肥皂水检测法或专业检漏仪定位微漏点,确保压缩空气系统泄漏率低于行业允许标准(通常要求≤10%)。重点检测油气分离器、最小压力阀等关键部件密封性能。
2. 运行参数检测
通过在线监测系统记录运行时的压力、温度、电流等核心参数:
- 排气压力波动范围(应控制在额定值±0.1MPa内)
- 主机轴承温度(不超过95℃)
- 排气温度(风冷机型≤100℃,水冷机型≤90℃)
- 三相电流平衡度(偏差<5%)
3. 润滑油系统检测
提取油样进行实验室分析,检测:
- 运动粘度变化率(与新油对比不超过±15%)
- 酸值(≤0.5mgKOH/g)
- 金属磨粒含量(铁谱分析判断磨损程度)
同时检查油滤器压差报警功能有效性,确保油路通畅。
4. 振动与噪音检测
使用振动分析仪测量主机、电机轴承部位的振动速度值(应≤4.5mm/s),频谱分析判断转子对中状态。声级计检测机组整体噪音(距离1米处≤85dB(A)),异常声响应排查轴承磨损或啮合间隙问题。
5. 电气系统安全检测
检测电机绝缘电阻(≥1MΩ)、接地电阻(≤4Ω),验证过载保护装置动作灵敏度。使用热成像仪扫描电气柜,发现接触器、接线端子等部位异常发热点。
6. 排气质量检测
依据ISO 8573-1标准检测压缩空气:
- 含油量(1级标准≤0.01mg/m³)
- 固体颗粒物浓度(1级标准≤0.1μm/0.1mg/m³)
- 露点温度(根据工艺要求检测压力露点值)
检测周期与结果应用
常规检测建议每2000小时/次,特殊工况应缩短至1000小时。检测数据需建立动态档案,结合历史记录分析劣化趋势,制定预防性维护计划。对于检测发现的异常参数,需按照"停机排查→部件更换→性能复测"流程处理,确保设备恢复最佳状态。
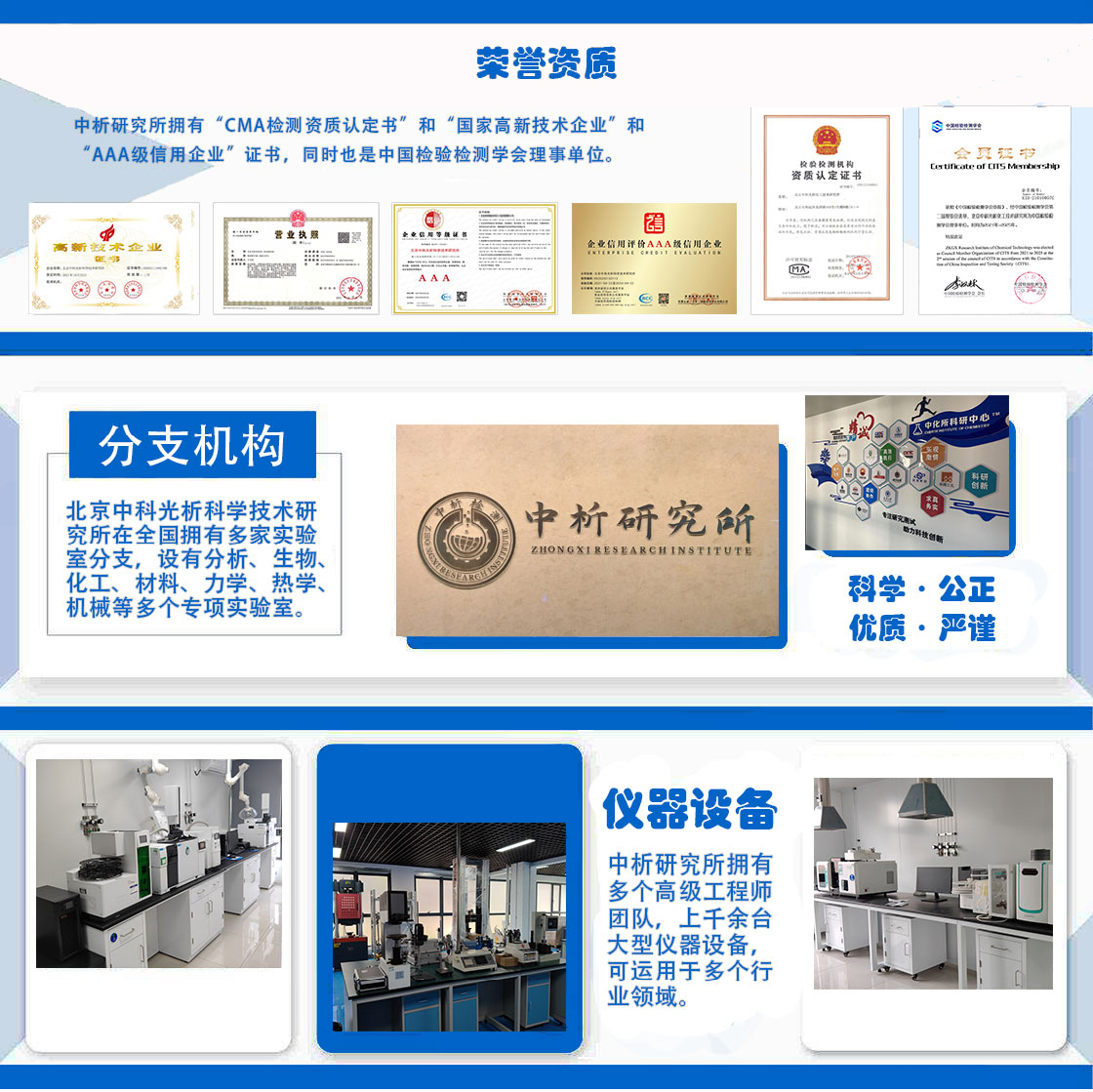
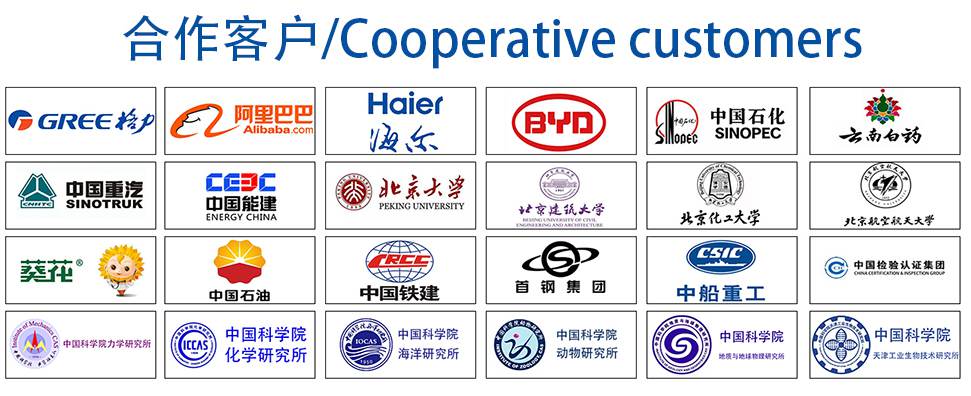