转盘钻孔机检测的重要性与核心项目解析
转盘钻孔机作为基础建设、矿山开采及桩基施工的关键设备,其性能稳定性和安全性直接影响工程质量和作业效率。随着设备长期处于高负荷运转状态,动力系统磨损、机械结构变形、液压元件老化等问题可能引发安全隐患。因此,系统化的检测项目成为设备维护管理的核心环节。通过定期开展专业检测,既能预防突发性故障导致的生产停滞,又能延长设备使用寿命,同时满足《建筑施工机械安全技术规范》等法规要求。
核心检测项目清单
1. 动力系统检测
重点检查发动机/电机输出功率稳定性,通过转速传感器监测空载与负载状态下的扭矩波动,同步检测燃油管路密封性(柴油机型)或电缆绝缘电阻(电动型)。需用振动分析仪监测曲轴、连杆等核心部件的异常振动频谱。
2. 传动结构检测
针对齿轮箱、离合器及主轴传动系统,采用工业内窥镜检查齿轮啮合面的磨损情况,使用红外热像仪监测轴承温升异常。同步进行润滑油金属颗粒分析,判断齿轮箱内部磨损程度。
3. 钻头总成检测
运用三维测量仪检测钻头同轴度偏差,评估切削刃口的磨损指数。通过超声波探伤仪排查钻杆内部裂纹,结合动态平衡测试仪检测旋转部件的动平衡参数,确保钻孔垂直精度达标。
4. 液压系统专项检测
使用液压测试台对主泵、换向阀进行压力-流量特性曲线分析,检测油缸密封件的泄漏率。同步监测液压油污染度(NAS等级),采用红外测温技术排查管路局部过热点,预防系统效率衰减。
5. 安全装置功能性验证
全面测试过载保护系统响应阈值,模拟触发紧急制动装置并记录动作时间。检查限位开关位置精度及防倾覆传感器的校准状态,确保自动锁止系统在坡度超限时可靠触发。
6. 控制系统精度校准
通过激光跟踪仪验证钻孔定位精度,使用多通道数据采集器记录PLC控制信号的时序准确性。针对数字化操作界面,需开展HMI人机交互响应测试及参数存储功能的完整性验证。
检测周期与实施标准
建议每500工作小时开展常规检测,大修周期不超过2000小时。检测过程应严格参照GB/T 20862-2018《旋挖钻机》及ISO 10987-3工程机械检测标准,关键参数偏差超过设备手册允许值10%时需立即停机检修。
结语
系统化的转盘钻孔机检测不仅是设备管理的法定要求,更是实现精准施工和成本控制的技术保障。通过建立包含12大类38项指标的检测体系,可显著降低设备故障率。最新案例显示,实施标准化检测的项目中设备综合效率(OEE)提升达27%,真正实现了预防性维护向预测性维护的跨越。
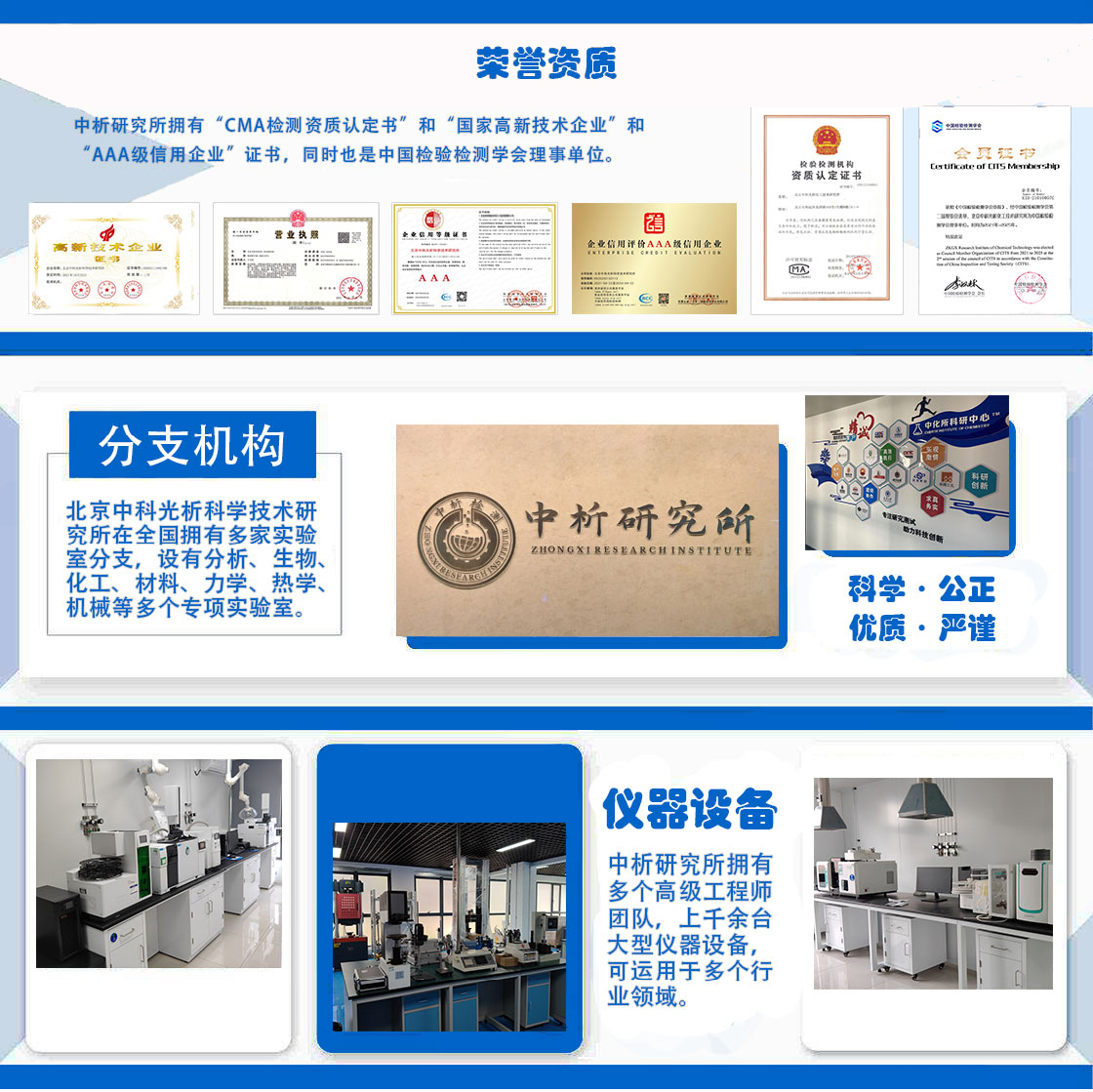
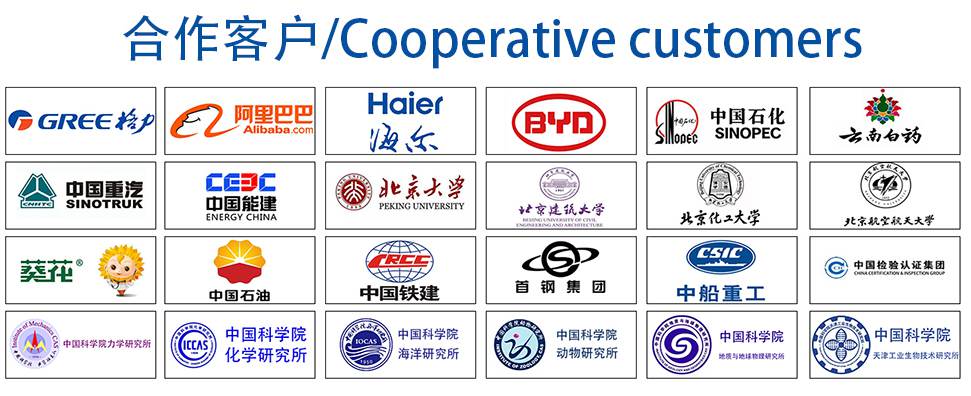