不含气液体瓶装生产线检测的关键项目与流程
在食品、饮料、日化等行业中,不含气液体(如纯净水、果汁、食用油、乳制品等)的瓶装生产线对产品质量与安全性要求极高。为确保生产效率和产品合规性,生产线需进行系统性检测,涵盖设备性能、包装密封性、灌装精度、卫生安全等多个环节。检测过程需严格遵循国家标准(如GB 14881《食品生产通用卫生规范》)及行业规范,同时结合自动化技术实现高效监控。
核心检测项目分类
1. 容器完整性检测
包括瓶身外观检查(裂纹、变形)、瓶口平整度检测,以及瓶盖与瓶口的适配性测试。通过视觉检测系统或人工抽检,确保容器无缺陷,避免灌装后泄漏或污染。
2. 灌装精度与液位控制
使用高精度流量计或称重传感器,实时监测每瓶液体的灌装量,误差需控制在±1%以内。同时,液位一致性需通过光电传感器或图像分析技术验证,确保标签标示容量与实际一致。
3. 封口密封性测试
针对瓶盖的旋紧力度、密封圈贴合度等,采用负压检漏仪或压力衰减测试法。模拟运输环境下的振动与温度变化,检测是否发生渗漏。
4. 微生物与异物控制
通过在线金属探测仪、X射线检测设备筛查异物;定期对灌装头、管道、储罐进行微生物采样(如ATP荧光检测),确保清洁度符合卫生标准。
5. 标签与喷码质量检测
利用OCR(光学字符识别)技术核对生产日期、批次号等信息准确性,同时检查标签位置、粘合强度及印刷清晰度,避免信息缺失或脱落。
自动化检测技术的应用
现代生产线普遍集成PLC控制系统、机器视觉和物联网(IoT)技术,实现实时数据采集与异常报警。例如,智能摄像头可同步完成瓶身缺陷、液位高度、标签贴附等多目标检测,效率较人工提升80%以上。检测数据云端存储并生成报告,便于质量追溯与工艺优化。
检测标准与合规性管理
企业需定期校准检测设备(如压力表、传感器),并通过第三方认证(如ISO 22000、HACCP)。针对出口产品,还需符合FDA(美国)或EU 1935/2004(欧盟)等国际法规,重点关注材料迁移测试与化学残留限值。
不含气液体瓶装生产线的检测既是质量保障的核心,也是企业降本增效的关键。通过科学的检测体系与智能化技术,可最大限度降低人为误差,提升产品市场竞争力。
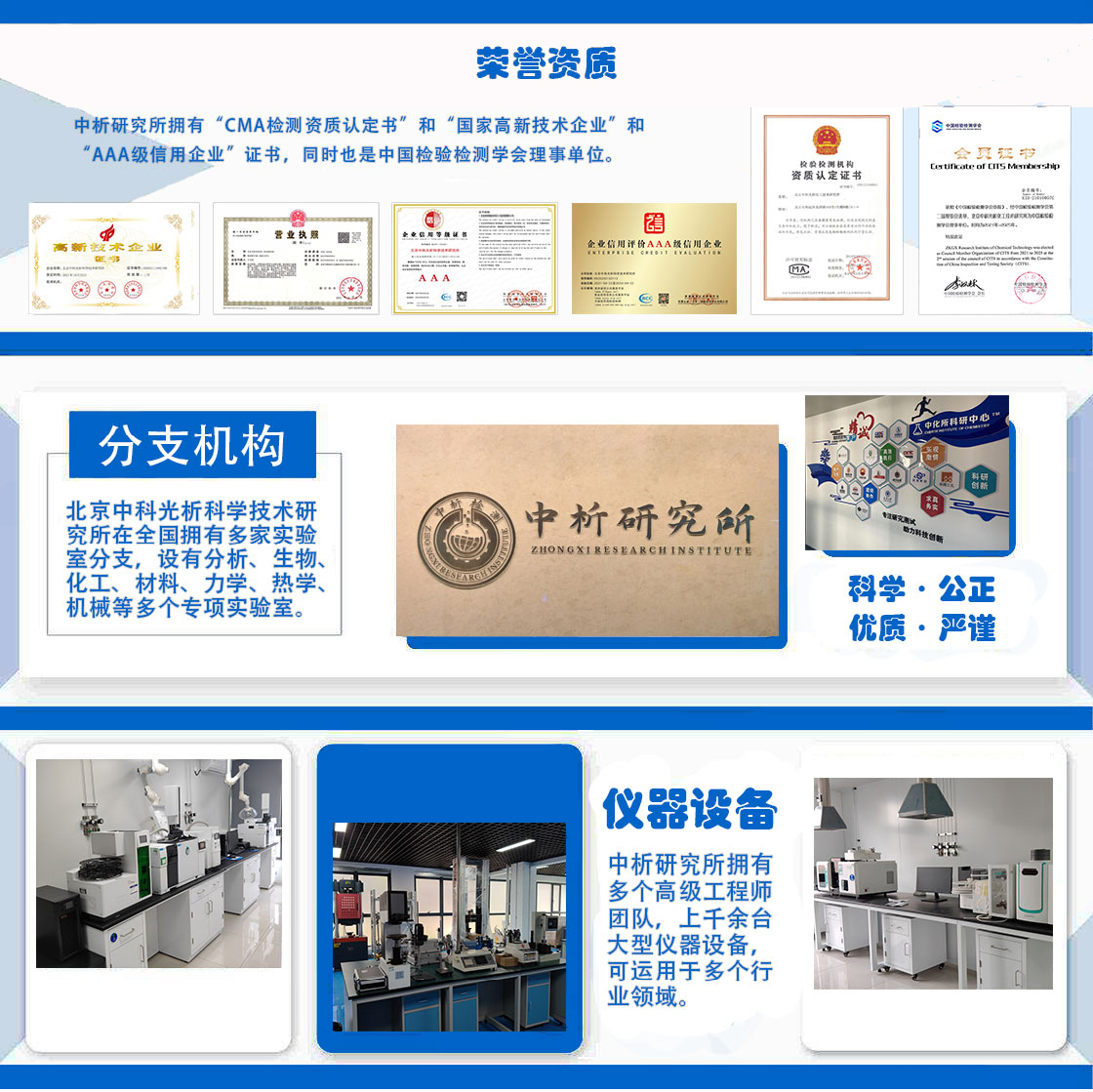
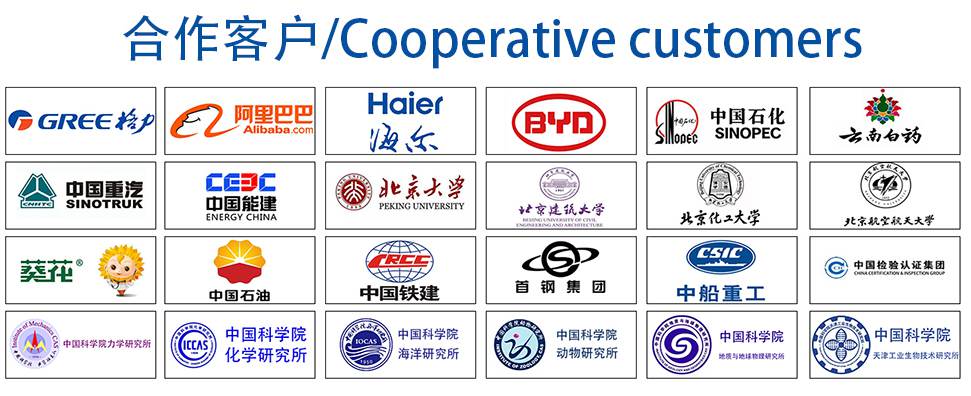