压铸机检测:保障生产效率与产品质量的关键环节
压铸机作为金属成型领域的核心设备,广泛应用于汽车零部件、电子元器件、家用电器等精密制造行业。其工作原理是通过高压将熔融金属注入模具型腔,快速冷却后形成高精度、高强度铸件。随着工业4.0发展,压铸机的性能稳定性、工艺参数控制能力直接决定了产品质量和生产效率。因此,定期的压铸机检测不仅是设备维护的必要手段,更是避免停机损失、降低废品率的核心措施。通过系统化检测,能够及时发现锁模力偏差、液压系统泄漏、温度控制异常等潜在问题,从而优化生产流程并延长设备使用寿命。
压铸机检测的核心项目解析
1. 整机性能检测
包括锁模力验证、射料压力精度测试、开合模速度稳定性分析。采用压力传感器与位移传感器实时监测锁模机构动态性能,确保压力误差≤1.5%,避免飞边或成型不足缺陷。
2. 关键部件状态检测
• 模具系统:检测型腔表面粗糙度(Ra≤0.8μm)、冷却水道堵塞及热平衡状态
• 压射系统:检查冲头与料筒间隙(标准0.08-0.12mm)、压射杆直线度偏差(≤0.02mm/m)
• 液压系统:油温控制精度(±2℃)、主泵容积效率(≥90%)、阀件响应时间(<50ms)
3. 工艺参数校准
建立压力-时间曲线(P-T图)与速度-行程曲线(V-S图)的数字化模型,对比理论参数与实际值的吻合度。重点监控慢压射阶段(0.2-0.5m/s)与快压射阶段(3-6m/s)的过渡平稳性。
智能化检测技术的创新应用
现代压铸机检测已融合物联网(IoT)与人工智能算法,通过部署振动分析传感器和热成像仪,实现:
• 实时监测曲肘机构磨损趋势(振动频率>200Hz时预警)
• 智能诊断液压油污染度(NAS 1638标准8级以下)
• 自动优化工艺参数组合(基于深度学习的历史数据挖掘)
这些技术使设备故障预测准确率提升至95%以上,同时减少30%的非计划停机时间。
检测标准与周期规划建议
依据JIS B8655和GB/T 25712标准,建议执行:
• 日常检测:每班次检查液压油位、润滑系统供油量(≥0.5mL/次)
• 月度检测:全面校准压力/温度传感器、验证安全门联锁响应时间(<0.5s)
• 年度大检:进行系统效率测试(≥75%)、电气绝缘电阻测量(>5MΩ)
通过构建科学的检测体系,可确保压铸机持续处于最佳工作状态,为企业创造更大经济效益。
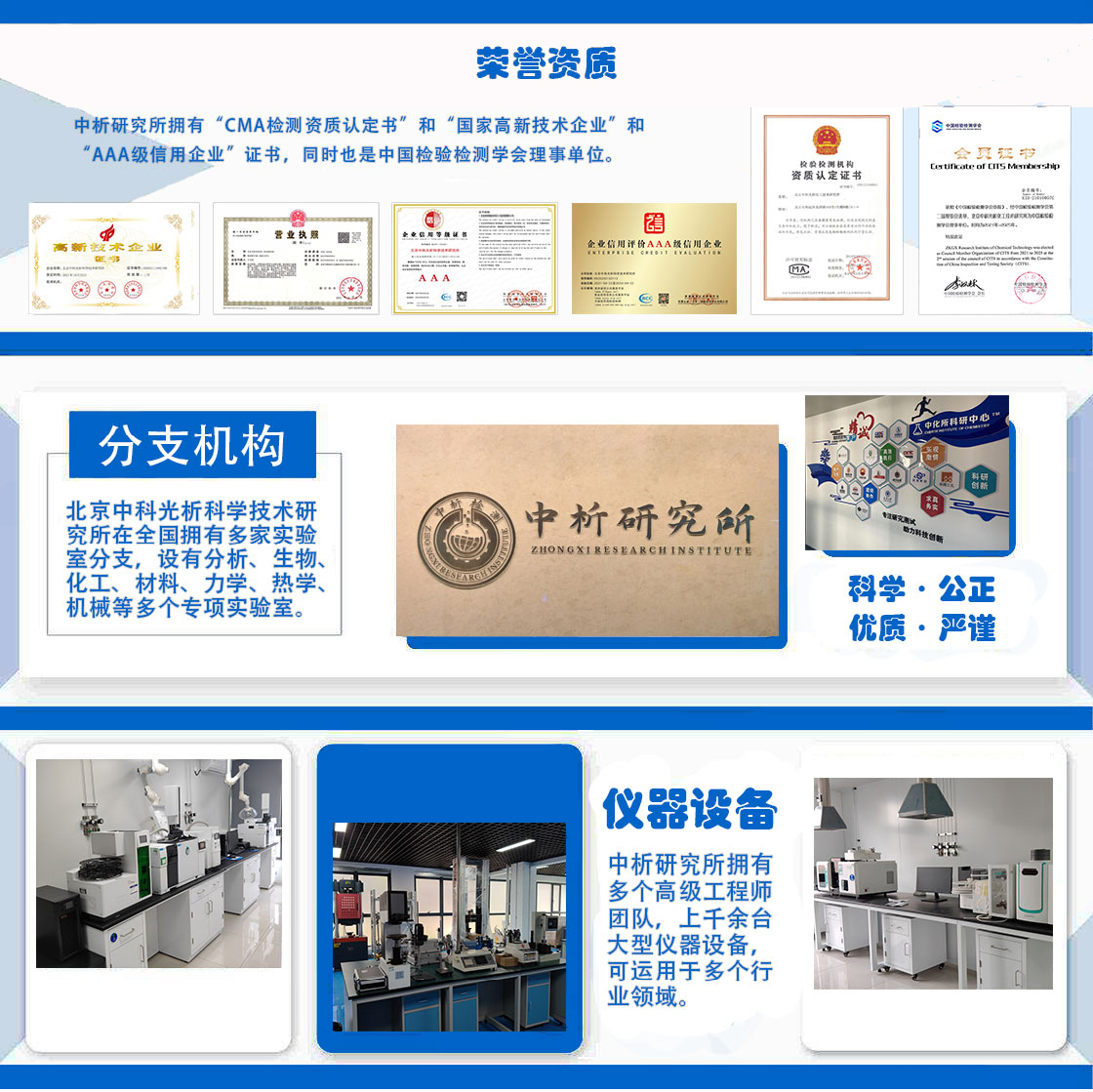
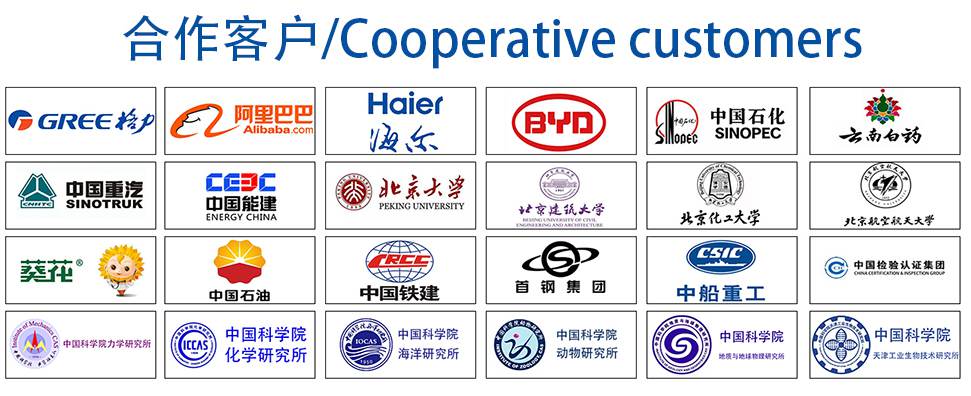