舰船液压设备检测体系解析
在现代化舰船装备体系中,液压系统作为动力传输的核心载体,其可靠性直接关系到船舶运行安全与作战效能。针对液压泵、液压马达、液压阀三大核心部件,建立科学系统的检测体系已成为船舶维护保障的重要环节。根据国际海事组织(IMO)MSC/Circ.1134号通函及国军标GJB 6388-2008要求,液压设备检测项目需覆盖性能参数、材料特性、环境适应性等28个技术维度,通过三级检测制度确保设备在极端工况下的稳定表现。
液压泵检测项目
1. 容积效率检测:采用高精度流量计对比理论流量与实际输出流量,要求额定压力下效率不低于92%
2. 压力脉动测试:使用动态压力传感器捕捉0.1Hz-1000Hz频段压力波动,峰值应控制在系统压力的±5%以内
3. 空载排量验证:在50rpm低速工况下进行排量标定,偏差不超过公称值的±1.5%
4. 轴向力平衡检测:通过应变片测量轴承负载,确保最大轴向力小于设计值的85%
5. 高温耐久性试验:在110℃油温条件下连续运行500小时,检测容积效率衰减不超过2%
液压马达检测项目
1. 启动力矩测试:采用扭矩传感器测定最低启动压力对应的输出扭矩,应符合ISO 4391标准要求
2. 低速稳定性验证:在5rpm工况下连续运转2小时,转速波动率应<0.5%
3. 泄漏量监测:使用同位素示踪法检测内泄量,每转泄漏不超过0.1ml/rev
4. 冲击载荷试验:模拟螺旋桨突然卡滞工况,检测缓冲阀响应时间≤10ms
5. 盐雾腐蚀测试:按GJB 150.11A标准进行96小时盐雾试验,关键部件无可见腐蚀
液压阀检测项目
1. 阀芯换向特性:采用高速摄像系统记录换向时间,先导式换向阀应≤25ms
2. 压力超调量检测:在阶跃响应测试中,系统压力超调不得超过设定值的15%
3. 微泄漏检测:使用氦质谱检漏仪检测密封面,泄漏率≤1×10^-6 Pa·m³/s
4. 抗污染能力测试:在NAS 1638 8级污染油液中持续工作200小时,性能参数波动<3%
5. 振动疲劳试验:按MIL-STD-810G方法进行三轴随机振动测试,持续6小时无结构损伤
检测技术创新方向
当前业内正推进基于数字孪生的预测性检测技术,通过植入式传感器采集压力脉动、温度梯度等128维特征数据,结合神经网络算法实现故障早期预警。某型舰用液压系统已实现关键部件剩余寿命预测精度达到±5%,大幅降低非计划性维护频次。同时,微型内窥检测机器人、太赫兹无损探伤等新技术正在改变传统检测模式,可使阀体内部缺陷检出率提升至99.7%。
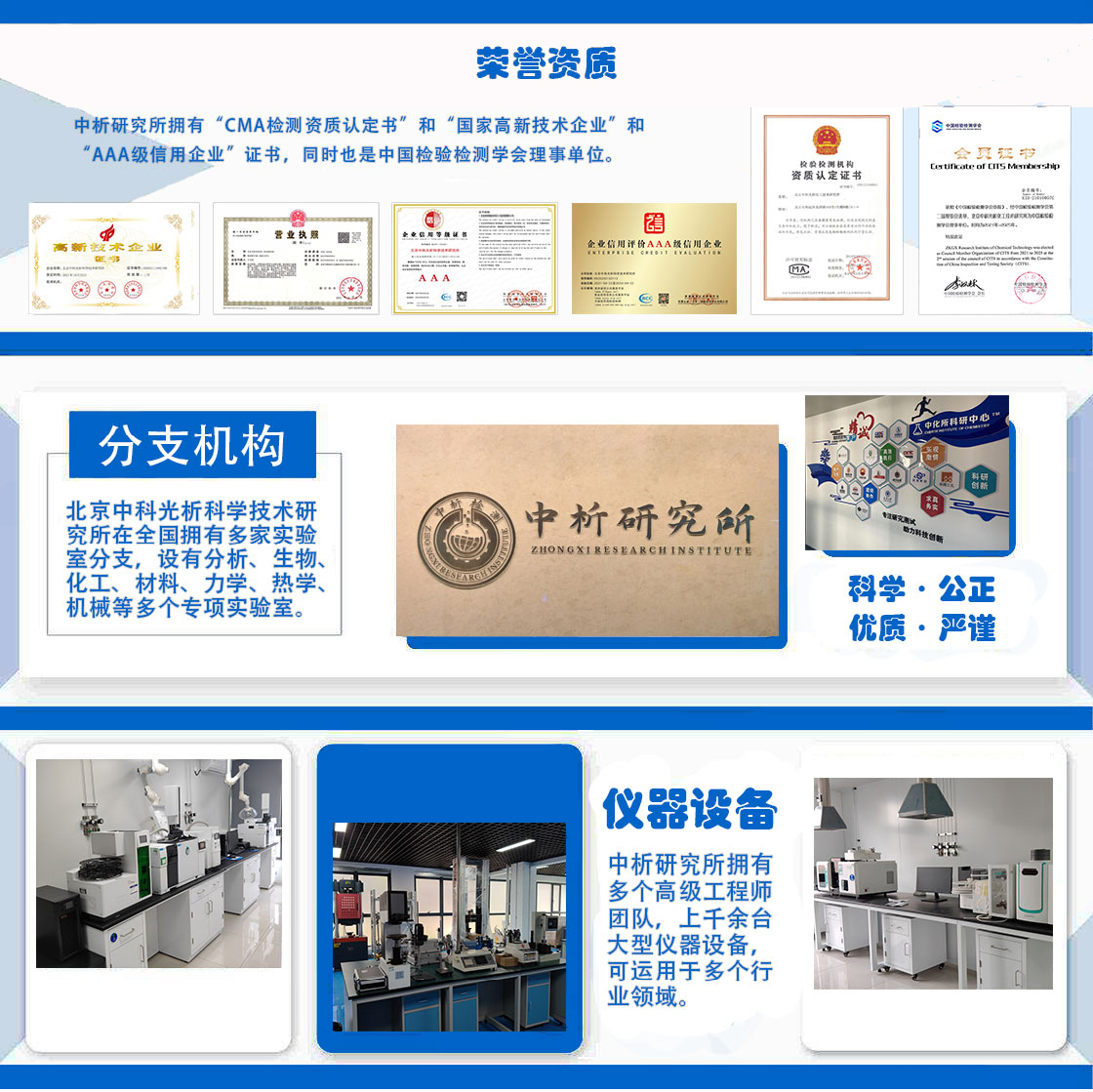
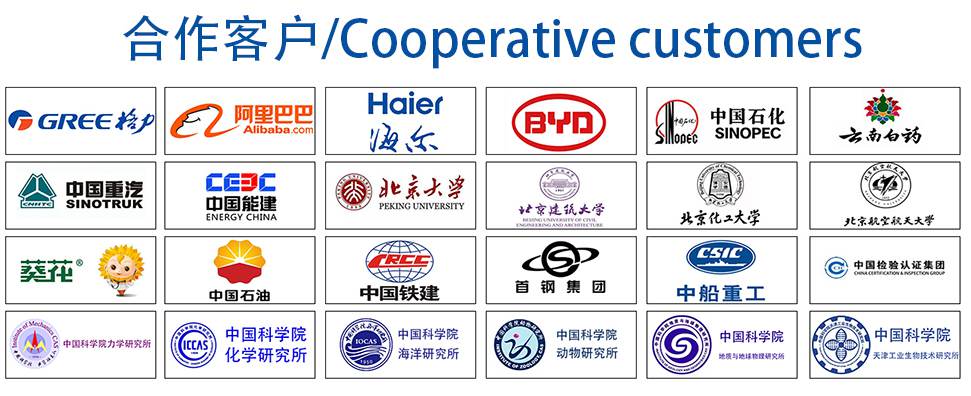