液压泵检测的重要性与必要性
液压泵作为液压系统的核心动力元件,其性能直接关系到工程机械、工业设备及生产线的运行效率与安全性。据统计,液压系统约70%的故障源于液压泵异常,因此定期开展液压泵检测是保障设备可靠运行的关键措施。通过专业检测能有效评估液压泵的工作效率、泄漏情况、磨损状态及使用寿命,避免因泵体故障导致的停机损失甚至安全事故。检测过程需结合国家标准(如GB/T 17446)和行业规范,涵盖外观检查、性能测试、油液分析等多个维度。
液压泵核心检测项目详解
1. 外观与结构检测
通过目视检查泵体表面是否有裂纹、腐蚀或异常变形,确认密封件完整性及紧固件状态。使用激光测量仪检测安装平面度误差(要求≤0.05mm),同时检查轴封处是否存在渗漏痕迹。
2. 性能参数测试
• 容积效率测试:在额定压力下测量实际流量与理论流量的比值(正常值应≥90%)
• 总效率测试:计算机械效率与容积效率的乘积(ISO 4409标准要求≥85%)
• 压力脉动检测:采用高频压力传感器测量压力波动(允许值<±2.5%)
3. 油液污染度分析
使用颗粒计数器检测油液清洁度(NAS 1638等级需≤8级),油液含水量应<0.1%。铁谱分析可检测磨损金属颗粒的尺寸和浓度,判断轴承、齿轮等部件的磨损趋势。
齐全检测技术应用
现代化检测手段为液压泵评估提供精准支撑:
• 振动频谱分析:通过FFT变换识别异常振动频率,定位故障源(如气穴现象特征频率)
• 红外热成像:监测泵体温度分布,温差>15℃时提示内部异常
• 超声波检测:发现早期气蚀和泄露(声发射值>60dB需预警)
检测周期与注意事项
建议每运行2000小时或每年至少进行1次全面检测,恶劣工况下应缩短至1000小时。检测时需注意:
1. 使用经校准的专用检测设备
2. 确保测试油温控制在40±5℃
3. 严格执行安全操作规程(如先泄压后检测)
4. 建立完整的检测数据档案,实现状态趋势分析
结语
科学的液压泵检测体系不仅能预防突发故障,还可延长设备使用寿命30%以上。随着智能传感技术的发展,基于物联网的在线监测系统正在成为行业新趋势,推动液压系统维护进入预测性维护新阶段。
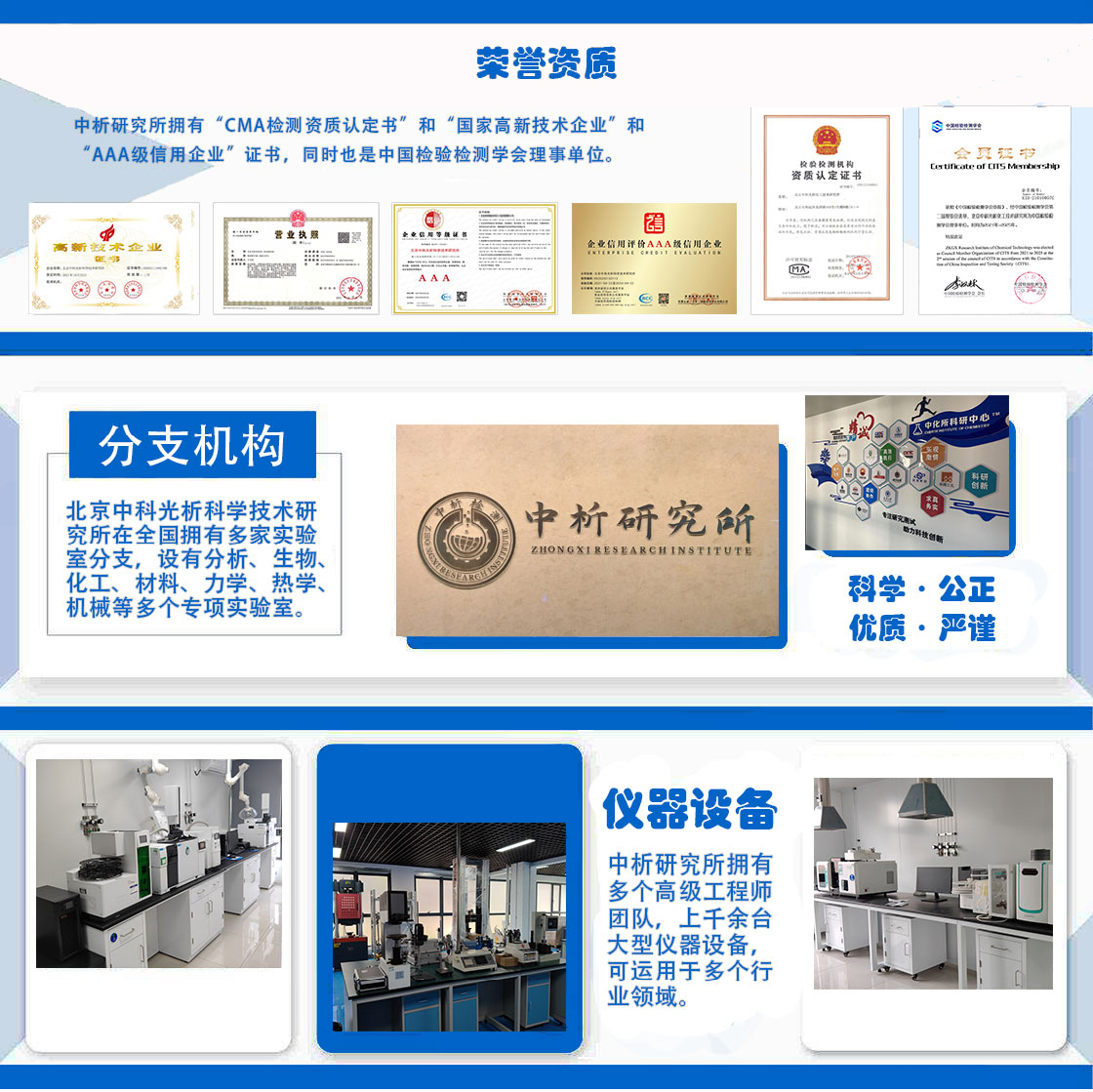
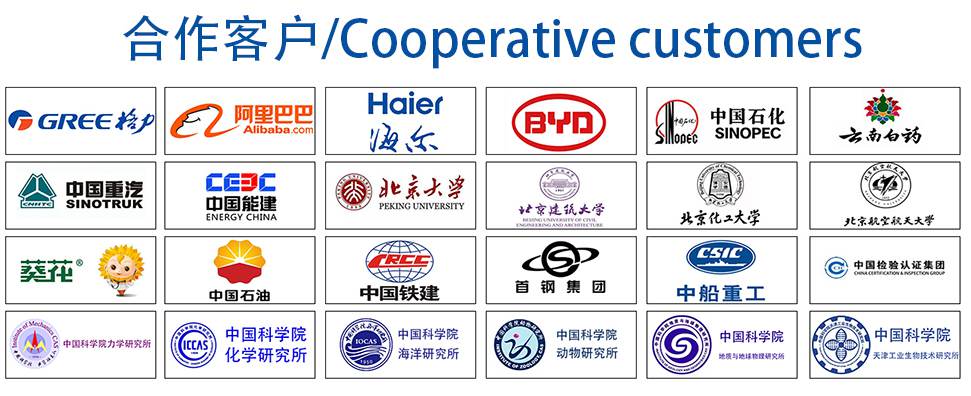