加热炉节能监测检测的重要性与实施要点
在冶金、化工、建材等工业领域,加热炉作为核心热工设备,其能耗占比普遍达到企业总能耗的30%-50%。随着国家"双碳"目标的持续推进,开展加热炉节能监测检测已成为企业降低生产成本、提升能效水平的关键举措。通过系统化的检测与评估,不仅能发现设备运行中的能源浪费点,更可为后续节能技术改造提供科学依据。目前国内重点用能单位已逐步将加热炉能效监测纳入常态化管理,部分省市更将其作为强制性节能审查项目。
核心检测项目体系
热效率专项检测
采用热平衡法对加热炉整体热效率进行测算,重点监测有效热负荷与供给总热量的比值。通过红外热像仪检测炉体表面散热损失,结合烟气分析仪测定排烟温度和氧含量,准确计算排烟热损失。典型案例显示,当排烟温度每降低20℃,热效率可提升1.2%-1.8%。
燃烧系统性能检测
使用烟气成分分析仪检测CO、O₂、NOx等参数,评估燃烧完全度与空气过剩系数。对燃烧器进行火焰形态检测,确保燃料与空气的混合比例达到最佳状态。某钢铁企业通过优化燃烧系统,使空气过剩系数从1.4降至1.2,年节省天然气达120万m³。
炉体保温性能检测
采用表面温度法评估炉墙、炉顶等部位的保温性能,检测点间距不超过2m。重点监测高温段保温层厚度与导热系数,要求炉体外表面温度不超过环境温度+50℃。某玻璃窑炉改造后,外壁温度下降40℃,年节能量达2600吨标煤。
余热回收系统检测
对预热器、余热锅炉等装置进行热交换效率测试,检测烟气余热回收率是否达到设计值。通过流量计和温度传感器监测介质进出口参数,核算实际回收热量。某石化企业加装热管换热器后,余热回收率提升至68%,年创效超500万元。
自动化控制系统检测
验证温度控制系统精度是否在±1%范围内,检测氧含量闭环控制响应时间是否达标。对燃烧控制系统进行阶跃扰动试验,评估PID参数设置的合理性。某陶瓷厂实施智能控制改造后,产品单位能耗下降12%。
检测实施规范与标准
执行检测时应严格遵循GB/T 15318《工业加热炉节能监测方法》、GB 17167《用能单位能源计量器具配备和管理通则》等标准要求。检测周期建议每季度开展1次运行监测,每年进行1次全面检测。对检测发现的排烟温度超标、保温层破损等问题,应及时制定整改方案并跟踪验证。
企业通过建立常态化的加热炉能效监测体系,可系统性地挖掘节能潜力。实践表明,规范的节能检测可帮助典型加热炉装置实现8%-15%的节能效益,投资回收期普遍在2年以内,具有显著的经济效益和环境效益。
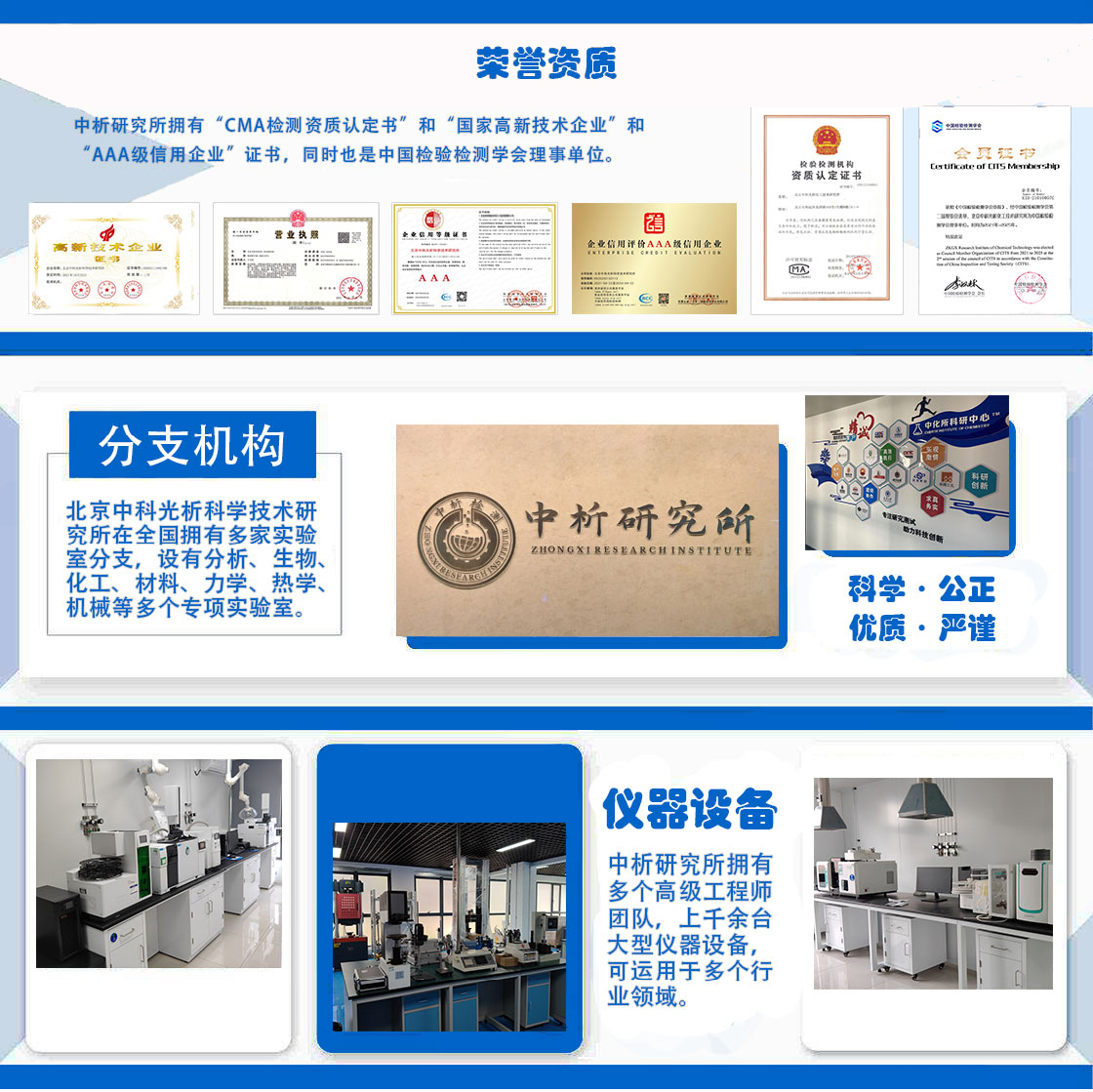
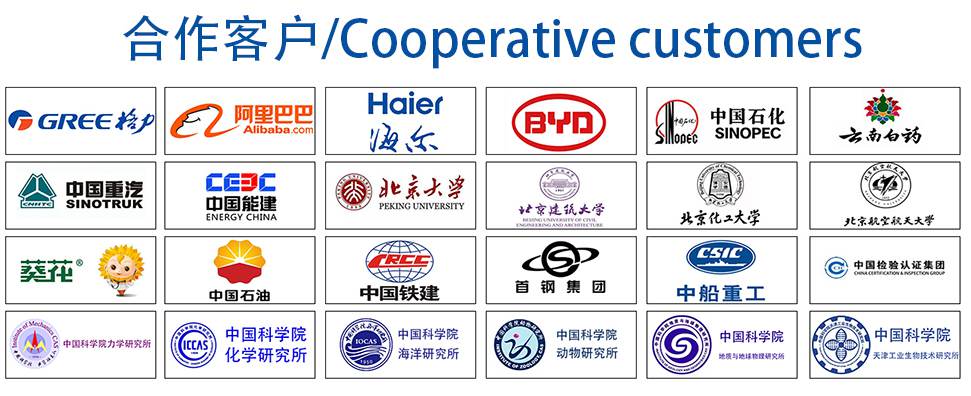