浮法玻璃退火窑检测技术全解析
浮法玻璃退火窑作为玻璃生产线的核心设备之一,承担着消除玻璃板内部残余应力、调整玻璃结构稳定性的关键任务。其运行状态直接影响玻璃的平整度、机械强度和成品率。随着现代玻璃工业对产品质量要求的不断提升,退火窑检测已成为生产过程中不可或缺的环节。通过系统化检测,企业不仅能够预防设备故障导致的非计划停机,还能优化能耗指标,确保玻璃产品达到严格的国际质量标准。
核心检测项目及技术要点
1. 温度场均匀性检测
采用红外热成像仪配合分布式热电偶网络,对退火窑各温区进行三维温度场测绘。重点检测横向温度偏差(控制在±2℃以内)、纵向温度梯度(不超过3℃/m),以及冷却区与缓冷区的温度过渡曲线。同时需验证温度控制系统的PID参数设定是否合理,确保温度波动范围符合ASTM C1048标准要求。
2. 应力分布检测
运用偏振光应力检测系统,对出窑玻璃板进行全幅面应力扫描。检测点密度应达到每平方米100个采样点,重点监控边部应力集中区域。依据ISO 12543标准,退火良好的玻璃表面压应力应≤7MPa,内部张应力≤3MPa。发现异常应力条纹需立即调整退火曲线参数。
3. 传动系统振动检测
使用激光测振仪对辊道传动机构进行频谱分析,检测轴承座振动速度(≤4.5mm/s RMS)、齿轮啮合频率异常。同步检查辊子圆跳动量(≤0.15mm)和同轴度偏差(≤0.1mm/m),预防因机械振动导致的玻璃表面划伤或波纹缺陷。
辅助检测与工艺优化
4. 密封性能检测
通过烟雾示踪法结合差压计测量,评估窑体密封性。各段压力差应保持在设定值的±5Pa范围内,防止冷空气渗入导致温度场畸变。同时检查膨胀节密封件的磨损情况,对使用超过8000小时的密封组件进行预防性更换。
5. 能耗效率检测
采用热平衡分析法计算退火窑热效率,重点监测废气温度(应低于250℃)、烟气含氧量(控制在3-5%)及保温层表面温度(不超过环境温度+25℃)。通过能效检测可优化燃烧系统空燃比,实现单吨玻璃产品能耗降低8-12%的节能目标。
智能化检测技术应用
当前行业已广泛采用基于工业物联网的在线检测系统,集成温度、压力、振动等多维度传感器,实现退火窑状态的实时数字孪生建模。通过机器学习算法分析历史检测数据,可预测辊道轴承剩余寿命(精确度达±72小时)、自动生成退火曲线优化方案,使检测效率提升40%以上,缺陷预警准确率达到95%以上。
科学的检测周期建议为:日常点检(每班次)、全面检测(每月)、深度检测(年度大修)。所有检测数据应纳入MES系统建立设备健康档案,为预防性维护和工艺改进提供数据支撑。只有建立完善的检测体系,才能确保退火窑始终处于最佳工艺窗口,为生产高品质浮法玻璃提供坚实保障。
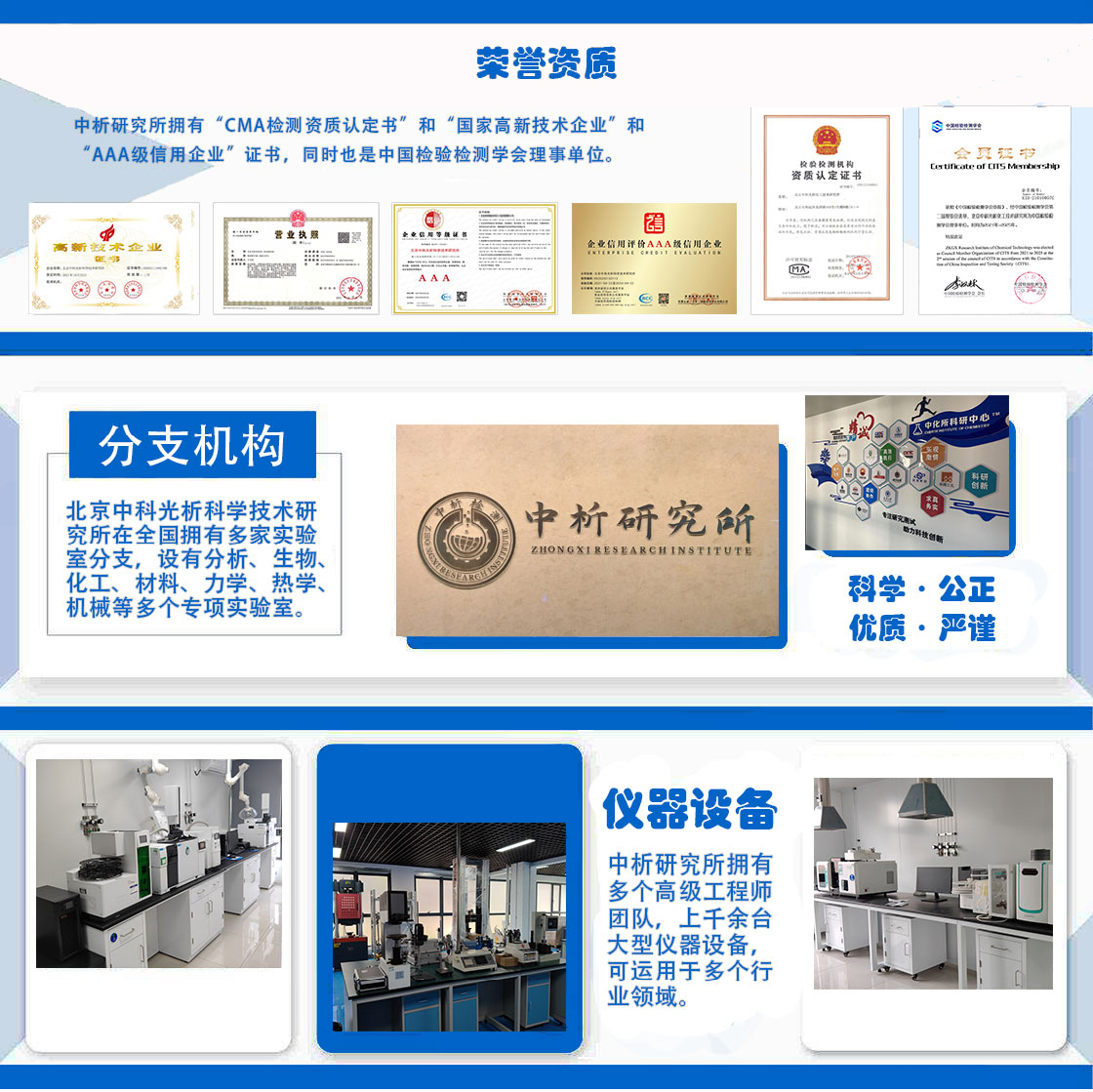
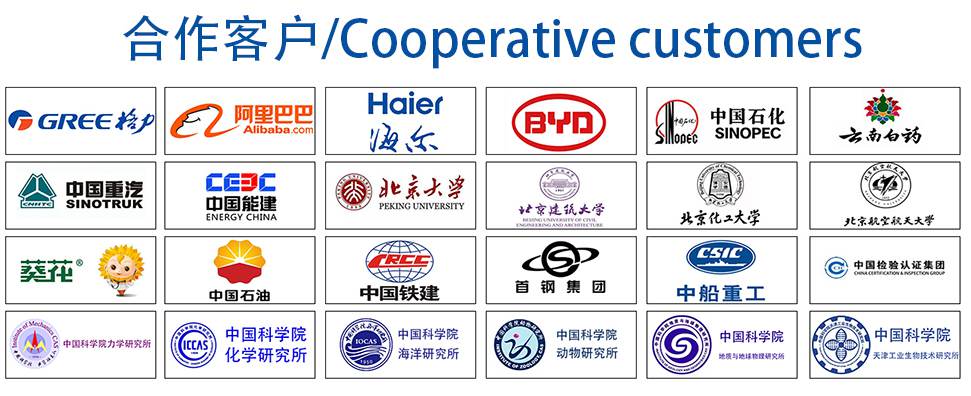