摩托车和电动自行车用镁合金车轮铸件检测
随着轻量化需求的提升,镁合金车轮凭借其高强度、低密度、优异的减震性和散热性能,在摩托车和电动自行车领域得到广泛应用。然而,铸造工艺的复杂性可能引发气孔、缩松、夹杂物等缺陷,直接影响车轮的力学性能和安全性。因此,对镁合金车轮铸件进行系统性检测是保障产品质量、提升使用寿命的核心环节。检测需覆盖材料成分、尺寸精度、机械性能及表面完整性等多个维度,确保符合行业标准(如GB/T 13820、ISO 16220等)及实际使用要求。
关键检测项目及方法
1. 化学成分分析
通过光谱分析仪(OES)或X射线荧光光谱仪(XRF),检测镁合金中镁(Mg)、铝(Al)、锌(Zn)、锰(Mn)等主元素及微量元素的含量,确保符合牌号要求(如AZ91D、AM60B等)。杂质元素(如铁、铜)需严格控制在标准限值内,以避免耐蚀性下降。
2. 机械性能测试
包括拉伸试验(检测抗拉强度、屈服强度、延伸率)、硬度测试(布氏硬度或洛氏硬度)及冲击韧性测试。试样需从铸件本体或同批次铸造试样中截取,模拟车轮实际受力条件下的性能表现。
3. 尺寸精度与几何公差检测
使用三坐标测量仪(CMM)或激光扫描技术,对轮毂的直径、轮辐间距、中心孔尺寸等关键参数进行测量。同时检查动平衡性,避免因尺寸偏差导致高速行驶时的振动问题。
4. 表面及内部缺陷检测
• 表面检查:目视或渗透探伤(PT)检测裂纹、冷隔、氧化夹杂等缺陷;
• 内部检测:X射线探伤(RT)或超声波探伤(UT)识别气孔、缩孔、疏松等内部缺陷,缺陷等级需符合ASTM E505等标准要求。
5. 耐腐蚀性与涂层检测
通过盐雾试验(如中性盐雾NSS、铜加速醋酸盐雾CASS)评估基体及表面处理层(如微弧氧化、电泳涂层)的耐蚀性。结合附着力测试(划格法)验证涂层结合强度。
6. 动态性能验证
在专用试验台架上模拟实际负载工况,进行径向疲劳试验、冲击试验和高速旋转试验,验证车轮在长期交变应力下的抗疲劳能力及结构稳定性。
检测结果的意义
系统性检测不仅确保镁合金车轮满足轻量化与安全性的双重需求,还能优化铸造工艺参数、降低废品率。通过数据化分析缺陷成因,企业可针对性改进模具设计、熔炼温度控制及后处理流程,推动行业向高可靠性、低成本化方向发展。
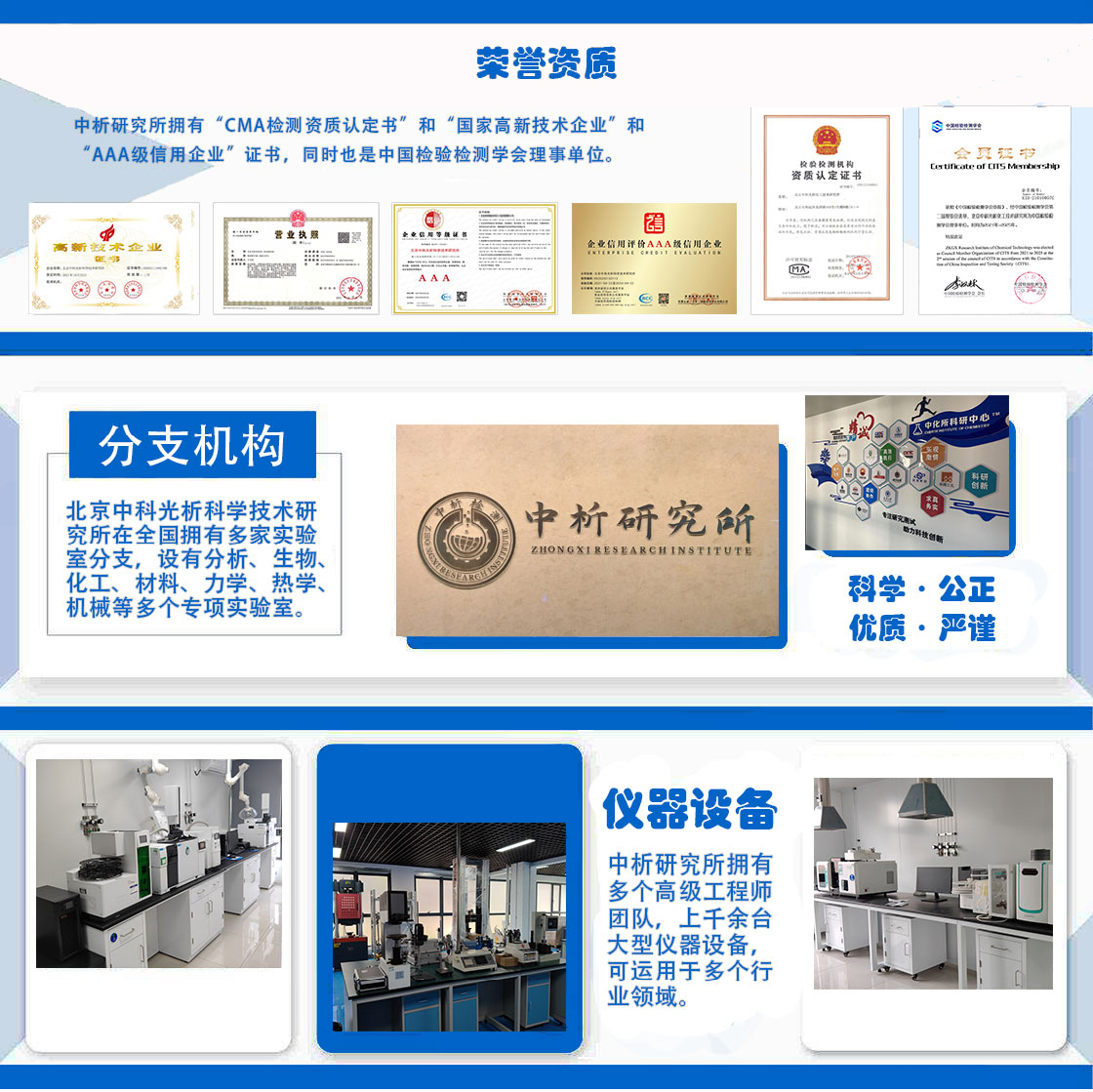
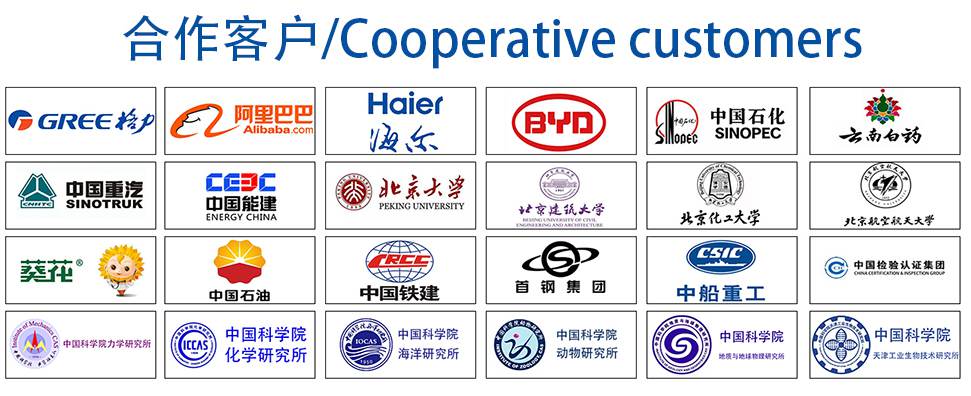