汽车用非电解锌片涂层检测的重要性
非电解锌片涂层(Non-Electrolytic Zinc Flake Coating)是汽车行业中广泛使用的一种表面处理技术,主要用于零部件(如螺栓、底盘件、制动系统等)的防腐和耐磨保护。与传统的电镀锌工艺不同,非电解锌涂层通过机械沉积或化学粘附形成致密的多层结构,具有高耐蚀性、低氢脆风险以及优异的环保性能。然而,涂层的质量直接影响零部件的使用寿命和安全性,因此需要通过严格的检测项目确保其性能符合行业标准(如ISO 10683、DIN 50939等)。
核心检测项目及方法
1. 涂层厚度检测
使用磁感应测厚仪或X射线荧光光谱仪(XRF)测量涂层的平均厚度,确保其符合设计要求(通常为5-20μm)。不同厚度的涂层适用于不同环境条件,例如在潮湿或高盐雾地区需加厚处理。
2. 附着力测试
通过划格试验(ISO 2409)或拉力试验评估涂层与基材的结合强度。划格法将涂层切割成网格状,观察其剥离情况;拉力试验则通过粘合剂和拉拔设备定量测量剥离力,要求涂层无脱落或分层现象。
3. 耐腐蚀性能检测
采用中性盐雾试验(NSS,ASTM B117)或循环腐蚀试验(CCT,ISO 14993),模拟高盐雾、湿热等环境条件,连续测试数百小时后检查涂层表面锈蚀面积。优质涂层应保持无明显红锈,且保护效率≥720小时。
4. 成分与微观结构分析
通过扫描电子显微镜(SEM)和能谱分析(EDS)检测涂层中锌片、铝粉及有机树脂的分布均匀性,确保无孔隙或裂纹。同时验证六价铬(Cr⁶⁺)等有害物质含量符合RoHS指令要求。
5. 耐磨性与耐冲击性测试
使用Taber磨耗仪模拟长期摩擦环境,测定涂层磨损量;冲击试验(ASTM D2794)则评估涂层在机械冲击下的抗开裂能力,确保零部件在装配和使用中不发生剥落。
6. 孔隙率检测
通过铁氰化钾溶液浸泡法或电化学法检测涂层孔隙率。若孔隙过多,腐蚀介质可能渗透至基材,导致局部锈蚀。合格的非电解锌涂层孔隙率应低于1个/cm²。
质量控制与行业标准
汽车制造商通常要求供应商提供第三方检测报告(如SGS、TÜV),并遵循IATF 16949质量管理体系。此外,涂层颜色一致性、表面粗糙度(Ra≤0.8μm)及无氢脆特性(通过延迟断裂试验验证)也是关键验收指标。通过系统化的检测流程,可有效保障涂层在复杂工况下的长期可靠性,降低车辆维护成本并提高安全性。
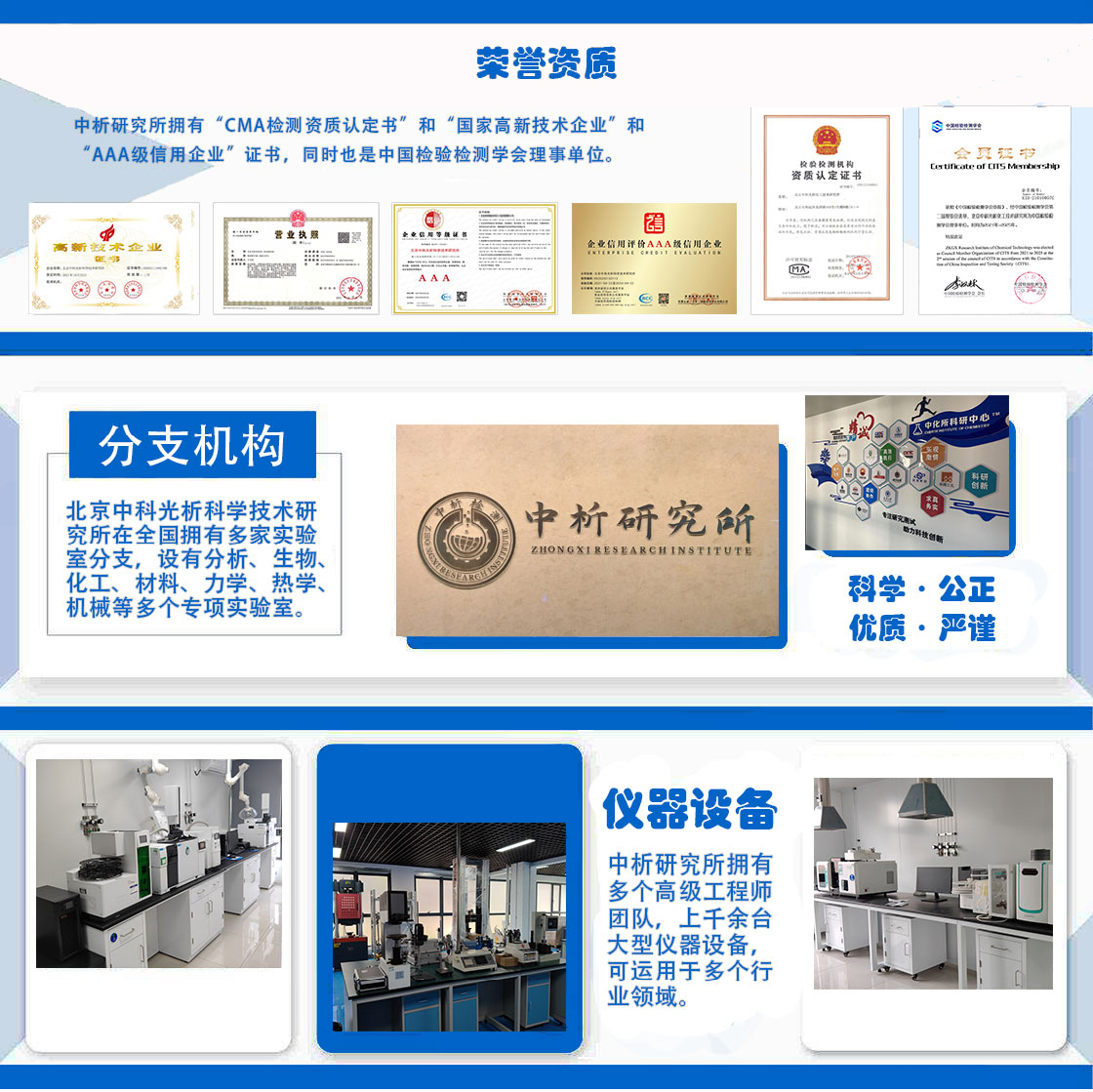
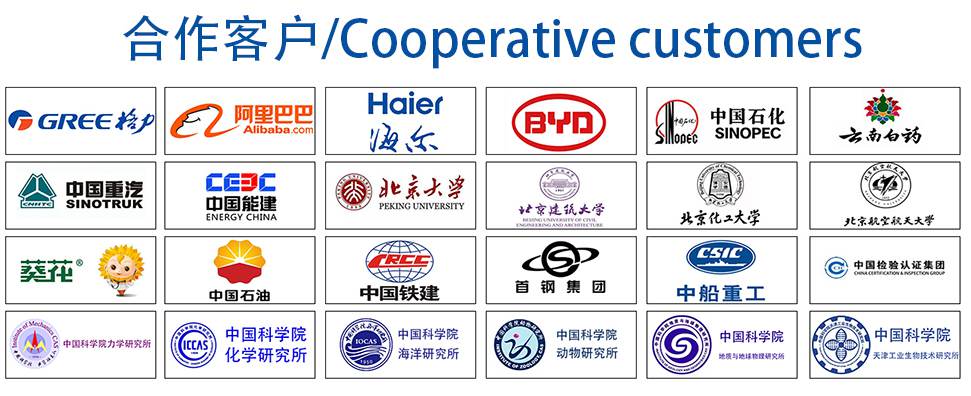